So next I made the liner. This needs a 1" hole bored in it that is 3.2" long. I started by putting some cast iron in the lathe and drilling it with a 7/8" drill. Note the use of the lathe carrier to eliminate the chance of the drill spinning in the Morse taper
Then I bored the liner out to about 50 thou undersize using a carriage stop to get the depth right
The outside diameter of the liner was made to about 2.5 thou bigger than the housing inside diameter.
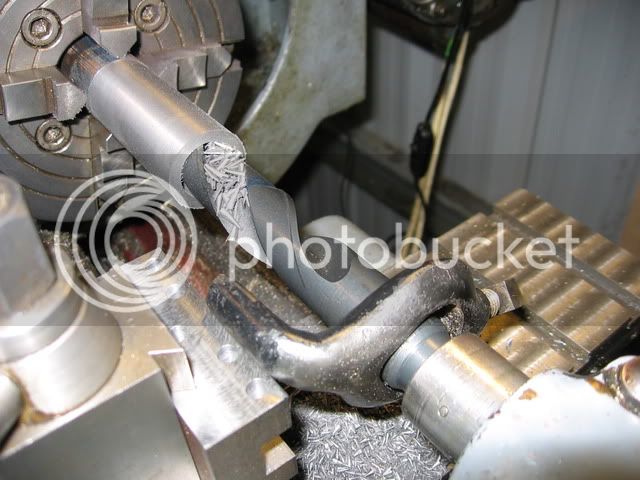
Then I bored the liner out to about 50 thou undersize using a carriage stop to get the depth right
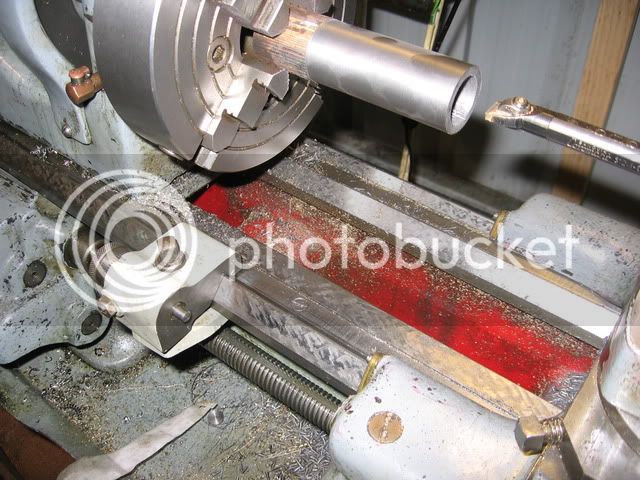
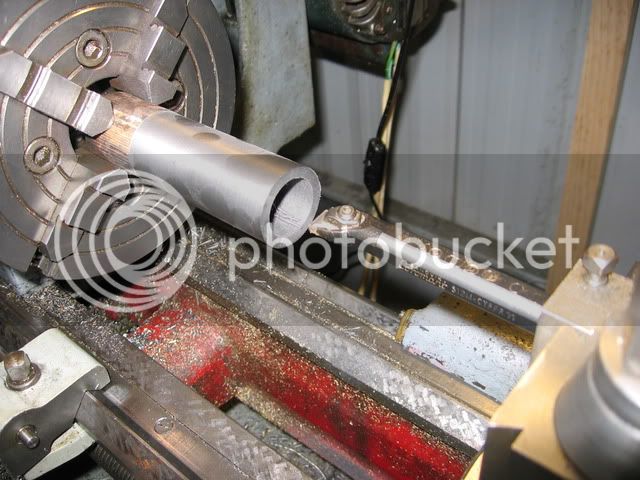
The outside diameter of the liner was made to about 2.5 thou bigger than the housing inside diameter.