idahoan
Well-Known Member
- Joined
- Oct 7, 2008
- Messages
- 594
- Reaction score
- 210
Hi Everyone
I wanted to post a picture of a large Pacific that currently lives at Antique Powerland near Brooks Oregon. This is the engine that caused me fabricate the brass upper swing arm bracket and soon to follow brass valve lifter assembly. This is a large engine (I'm not sure of the horse power but it stands well over 6ft. Tall) so some of the proportions are different than the model.
This engine also has the hit & miss dog bone governor.
As I think I may have indicated before; at this time I'm not planning on using the governor on my engine because it occupies space on the crankshaft that I have other plans for.
Thanks for checking in,
Dave
I wanted to post a picture of a large Pacific that currently lives at Antique Powerland near Brooks Oregon. This is the engine that caused me fabricate the brass upper swing arm bracket and soon to follow brass valve lifter assembly. This is a large engine (I'm not sure of the horse power but it stands well over 6ft. Tall) so some of the proportions are different than the model.
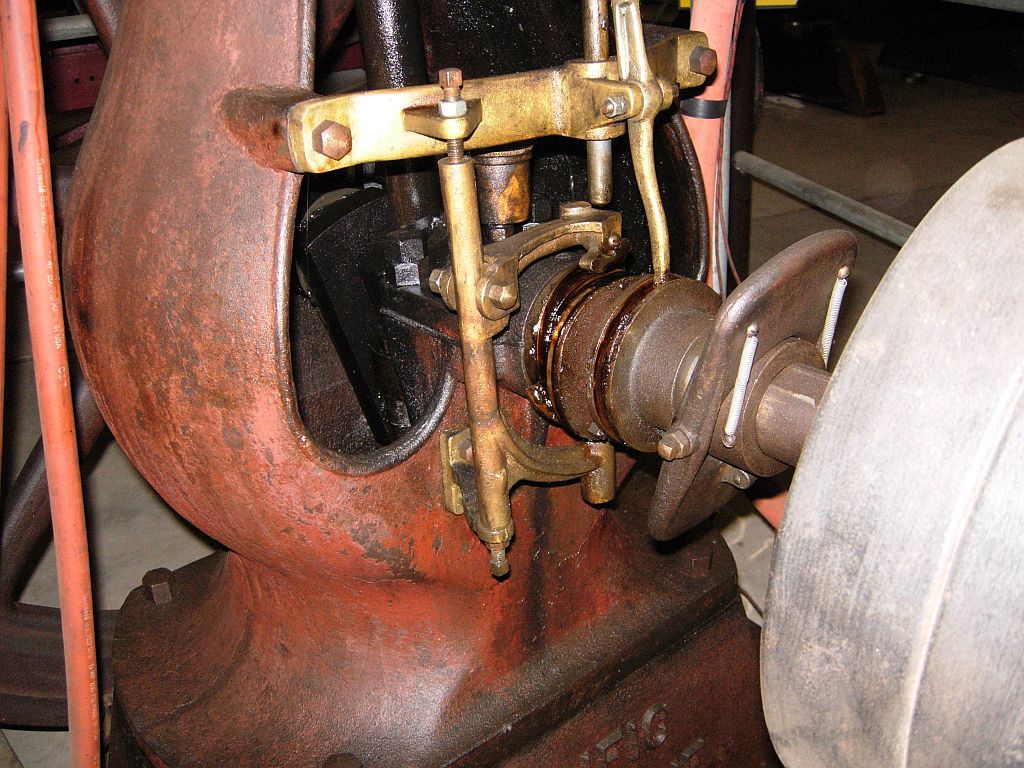
This engine also has the hit & miss dog bone governor.
As I think I may have indicated before; at this time I'm not planning on using the governor on my engine because it occupies space on the crankshaft that I have other plans for.
Thanks for checking in,
Dave