Metal Mickey
Well-Known Member
- Joined
- Jul 5, 2008
- Messages
- 612
- Reaction score
- 6
The main target to day was to complete the machining of the motor pulley and start rebuilding the Myford ML7 lathe. Boring of the 0.750 diameter hole proceeded with little drama if a little slowly. Once done to a nice snug fit, the next task was to cut the key way. Now I must admit that whilst I have read about the procedure in the past I have not had cause to cut one.
My starting point was to finds some tool steel of the same width as the key on the motor shaft, then grind the end of the tool steel to my own cutting profile. When done, I started by isolating the lathe from the power supply, to make sure I didnt do anything silly! I placed the tools steel in the same position on the tool post as a boring bar but the cutting face on its side facing me.
I thought it would be useful to make a mark on the pulley of where the key way was to be made and proceeded to make the first cut using the top slide. By only moving the cross slide out by 1 thou (0.001)of an inch made another cut.
After a short time a nice keyway started to be formed but I was concerned as the amount of pressure being placed on the top slide. So I decided to use the cross slides main hand wheel instead, and keep the top slide closed. This certainly helped to speed up the process and felt a more comfortable a solution.
I will make a fixture for future use (add it to the ever growing list of tools to make!) which isolates the need to cross or top slide to be used. There are various examples in books and magazines and no doubt there will be many more keyways out there waiting to be made
One silly mistake I made was to just cut the keyway where the pulley ended up when secured in the 3 jaw chuck. When trying the fit I was pleased, only then to find that the keyway position meant the grub screw used to secure the pulley was now partly over the pulley key! All I had to do was to take note BEFORE I made the keyway of where the tapped hole was. Not a great problem, but now I needed to drill and tap for a new grub screw.
After the pulley was cleaned up a little it was provisionally fitted to the motor on its bracket. What next I asked myself? Well there were several boxes holding various screws, bolts and other fixtures so I though a general reorganization of parts would be useful. So I set up a table and sorted out all the parts of the great mechanical puzzle so I could see what was what to re-assemble the lathe.
When the parts were sorted I thought the best way forward now was to put together as much as I could even if it had to come apart again when the parts from Myford arrive. A start was made by putting the tailstock back onto the lathe and its a part I think I will have to have another look at as it could be better. The next item assembled was the cross slide and saddle. The lead screw lock nuts were oiled up and the gib strip fitted. When looking at the cross slide I decided that since the fixings are metric (!) I would treat the lathe to new bolts. A new handle was fitted (not impressed with the handles sourced from a non Myford source) and I may have to make a small sleeve to match the difference between the handle bore and the saddle pin. Not a great difference and the handle tightens with the grub screw, but not really satisfactory. Another add it to the list item.
I have thought several times that the lathe has had work done on her before, and now I am certain. When I took the lathe apart I religiously kept everything in different small containers. Now putting the cross slide back together I couldnt find any laminate shims that fit between the cross slide and two plates that fit under the top of the lathe bed and the base of the cross slide. There must have been something because the cross slide will not move if the securing bolts are fully tightened, and I remember it moving when the lathe arrived (or at least I think it did )
So they will need to be purchased (that will be the third order!) and because of this omission I have decided that the lathe will be completely re-assembled and only then will I make the 3rd order from Myford. When the parts arrive the relevant parts will be disassembled and new ones fitted. So thats what I will do.
So far the tailstock has been fitted along with the motor bracket and cross slide and saddle. The lead screw has also be partly fitted.
All in all not too bad a day for a change.
My starting point was to finds some tool steel of the same width as the key on the motor shaft, then grind the end of the tool steel to my own cutting profile. When done, I started by isolating the lathe from the power supply, to make sure I didnt do anything silly! I placed the tools steel in the same position on the tool post as a boring bar but the cutting face on its side facing me.
I thought it would be useful to make a mark on the pulley of where the key way was to be made and proceeded to make the first cut using the top slide. By only moving the cross slide out by 1 thou (0.001)of an inch made another cut.
After a short time a nice keyway started to be formed but I was concerned as the amount of pressure being placed on the top slide. So I decided to use the cross slides main hand wheel instead, and keep the top slide closed. This certainly helped to speed up the process and felt a more comfortable a solution.
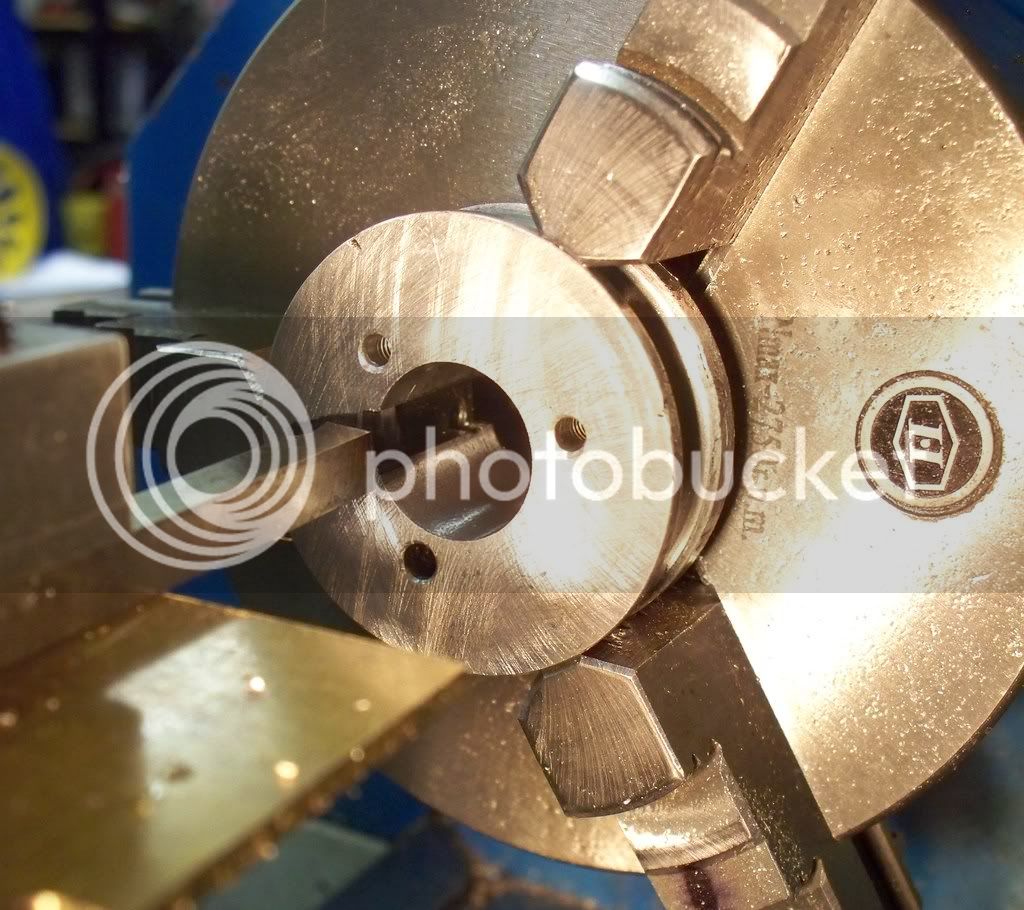
I will make a fixture for future use (add it to the ever growing list of tools to make!) which isolates the need to cross or top slide to be used. There are various examples in books and magazines and no doubt there will be many more keyways out there waiting to be made
One silly mistake I made was to just cut the keyway where the pulley ended up when secured in the 3 jaw chuck. When trying the fit I was pleased, only then to find that the keyway position meant the grub screw used to secure the pulley was now partly over the pulley key! All I had to do was to take note BEFORE I made the keyway of where the tapped hole was. Not a great problem, but now I needed to drill and tap for a new grub screw.
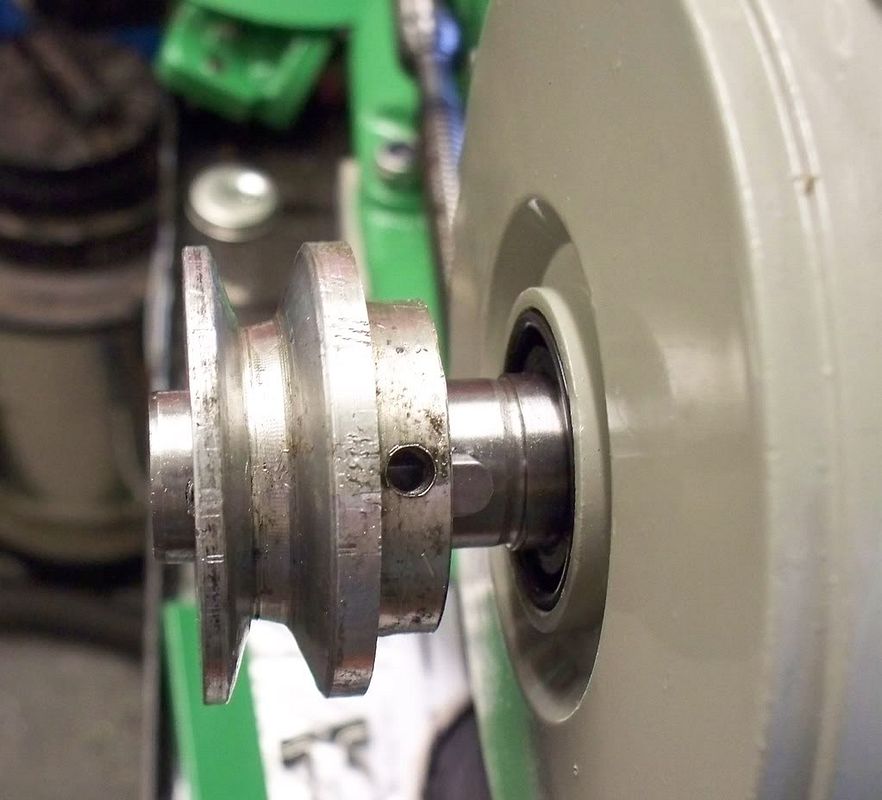
After the pulley was cleaned up a little it was provisionally fitted to the motor on its bracket. What next I asked myself? Well there were several boxes holding various screws, bolts and other fixtures so I though a general reorganization of parts would be useful. So I set up a table and sorted out all the parts of the great mechanical puzzle so I could see what was what to re-assemble the lathe.
When the parts were sorted I thought the best way forward now was to put together as much as I could even if it had to come apart again when the parts from Myford arrive. A start was made by putting the tailstock back onto the lathe and its a part I think I will have to have another look at as it could be better. The next item assembled was the cross slide and saddle. The lead screw lock nuts were oiled up and the gib strip fitted. When looking at the cross slide I decided that since the fixings are metric (!) I would treat the lathe to new bolts. A new handle was fitted (not impressed with the handles sourced from a non Myford source) and I may have to make a small sleeve to match the difference between the handle bore and the saddle pin. Not a great difference and the handle tightens with the grub screw, but not really satisfactory. Another add it to the list item.
I have thought several times that the lathe has had work done on her before, and now I am certain. When I took the lathe apart I religiously kept everything in different small containers. Now putting the cross slide back together I couldnt find any laminate shims that fit between the cross slide and two plates that fit under the top of the lathe bed and the base of the cross slide. There must have been something because the cross slide will not move if the securing bolts are fully tightened, and I remember it moving when the lathe arrived (or at least I think it did )
So they will need to be purchased (that will be the third order!) and because of this omission I have decided that the lathe will be completely re-assembled and only then will I make the 3rd order from Myford. When the parts arrive the relevant parts will be disassembled and new ones fitted. So thats what I will do.
So far the tailstock has been fitted along with the motor bracket and cross slide and saddle. The lead screw has also be partly fitted.
All in all not too bad a day for a change.