ChooChooMike
Well-Known Member
- Joined
- Jan 5, 2008
- Messages
- 863
- Reaction score
- 13
Here's my version of "Millie" that I finished a couple of months ago.
Millie is a single-acting oscillator or "wobbler" engine. Runs like a champ in either direction using about 10-15psi from a small paint brush compressor. The frame is 1-1/4" high, flywheel is 3/4" diameter, pistion is 1/8" diameter with a stroke of about 1/4". Made of brass/steel with aluminum for the tubing nipples.
This is my 5th running engine, if you count my finger powered one
This is the 1st that I built entirely on my Sherline mill and lathe at home. Perfect size equipment for this engine. The rest were 97.4% built on conventional sized equipment in my shop classes over the past few years.
This was a great build for me, complete with a number of screwups (who hasn't !) and a great experience in learning to use my Sherlines. Yup, I've got tons of pix along the way and will post build thread.
Plans from Sherline's Tabletop Machining book - originally published in Modeltec, May 1997.
Mike
Listen for the "revving" sound !! :big:
[ame]http://www.youtube.com/watch?v=VCgqIxOxoZo[/ame]
[ame]http://www.youtube.com/watch?v=QQNhOfvQ8hU[/ame]
[ame]http://www.youtube.com/watch?v=MFYT8ULMPB4[/ame]
The engine looks a little rough and acquired some "patina" ... ok a tad bit of rust from sitting around. I have most of the tooling marks sanded out, but I gotta git out the Dremel and clean up some of the gunk (oil/dirt), especially on the flywheel. I had Millie running on my paintbrush compressor for over an hour at one point just for kicks !! My very poor attempt at hand stamping "Millie" on the base turned out pretty bad, gotta laugh about it now !!
The parts :
11/12/11 Edit: added 2 more short videos I found laying around.
Millie is a single-acting oscillator or "wobbler" engine. Runs like a champ in either direction using about 10-15psi from a small paint brush compressor. The frame is 1-1/4" high, flywheel is 3/4" diameter, pistion is 1/8" diameter with a stroke of about 1/4". Made of brass/steel with aluminum for the tubing nipples.
This is my 5th running engine, if you count my finger powered one
This was a great build for me, complete with a number of screwups (who hasn't !) and a great experience in learning to use my Sherlines. Yup, I've got tons of pix along the way and will post build thread.
Plans from Sherline's Tabletop Machining book - originally published in Modeltec, May 1997.
Mike
Listen for the "revving" sound !! :big:
[ame]http://www.youtube.com/watch?v=VCgqIxOxoZo[/ame]
[ame]http://www.youtube.com/watch?v=QQNhOfvQ8hU[/ame]
[ame]http://www.youtube.com/watch?v=MFYT8ULMPB4[/ame]
The engine looks a little rough and acquired some "patina" ... ok a tad bit of rust from sitting around. I have most of the tooling marks sanded out, but I gotta git out the Dremel and clean up some of the gunk (oil/dirt), especially on the flywheel. I had Millie running on my paintbrush compressor for over an hour at one point just for kicks !! My very poor attempt at hand stamping "Millie" on the base turned out pretty bad, gotta laugh about it now !!
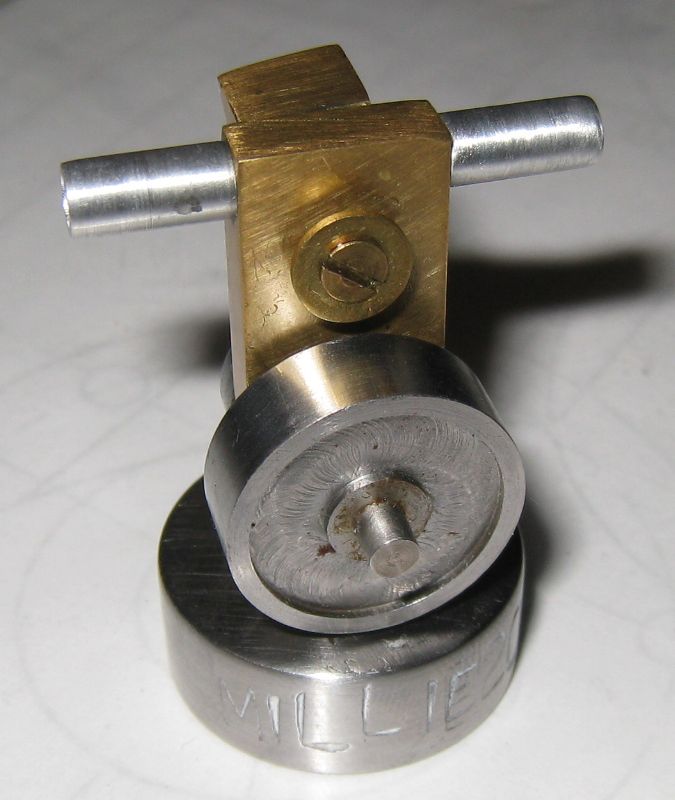
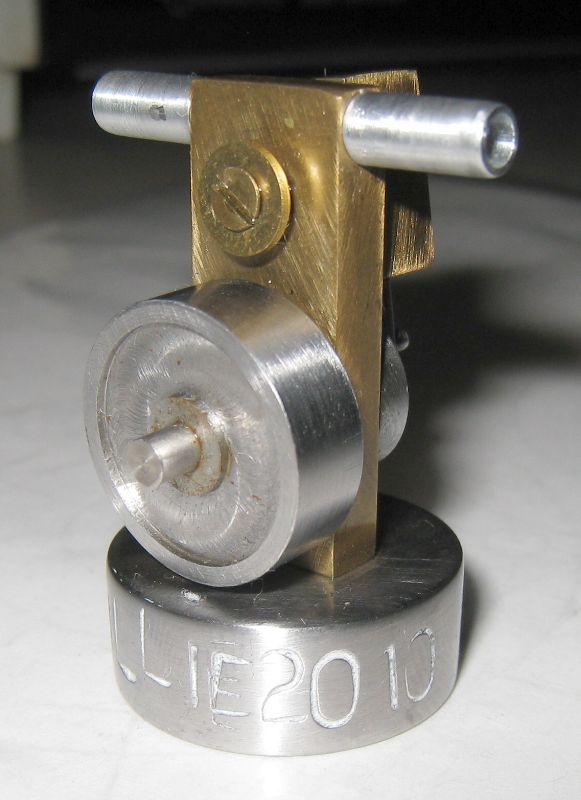
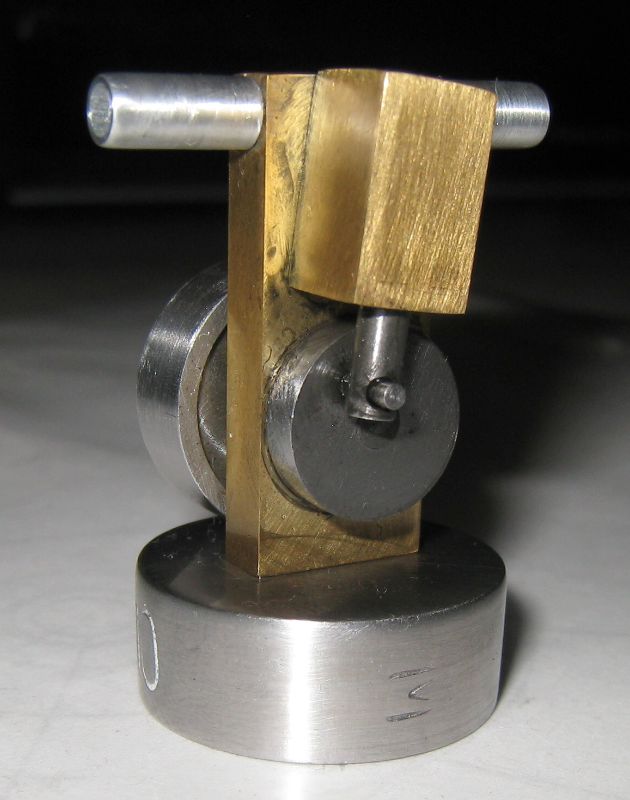
The parts :
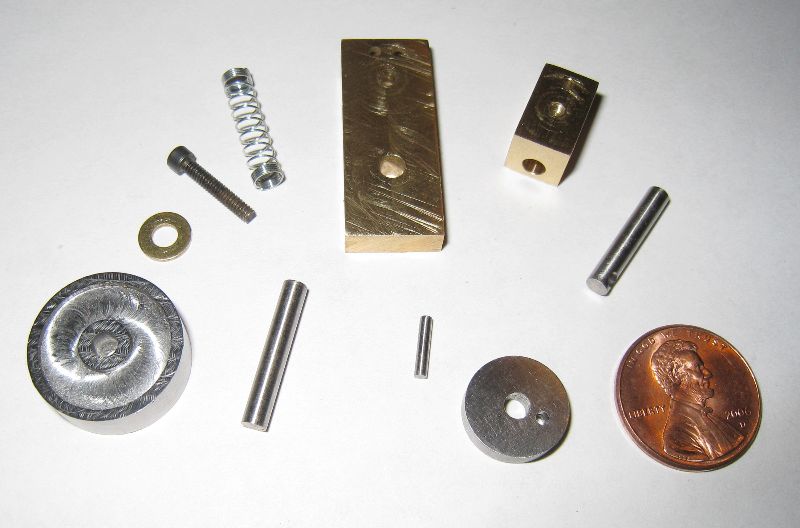
11/12/11 Edit: added 2 more short videos I found laying around.