A rare configuration in I/C engines is the square four. From the motorcycling world in the form from the British Ariel S/F classic for three decades.......
.....to Suzuki in their GP500 racing campaign years in the '70s thru 1990.
Can I do this configuration as my usual industrial utility builds?
Longboy's S/F build log starting next week!
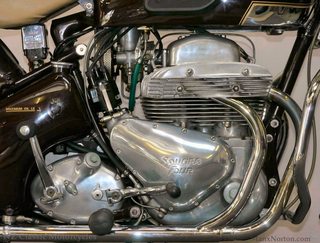
.....to Suzuki in their GP500 racing campaign years in the '70s thru 1990.
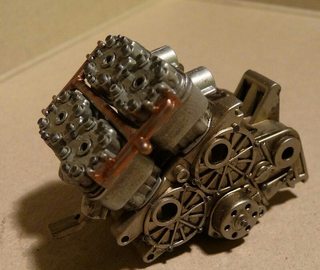
Can I do this configuration as my usual industrial utility builds?
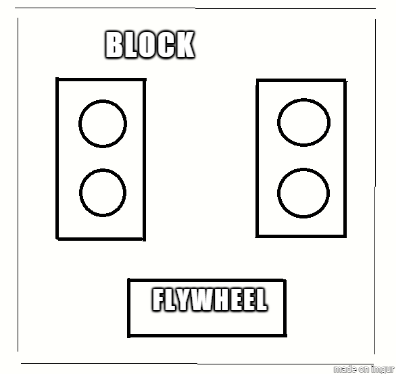
Longboy's S/F build log starting next week!
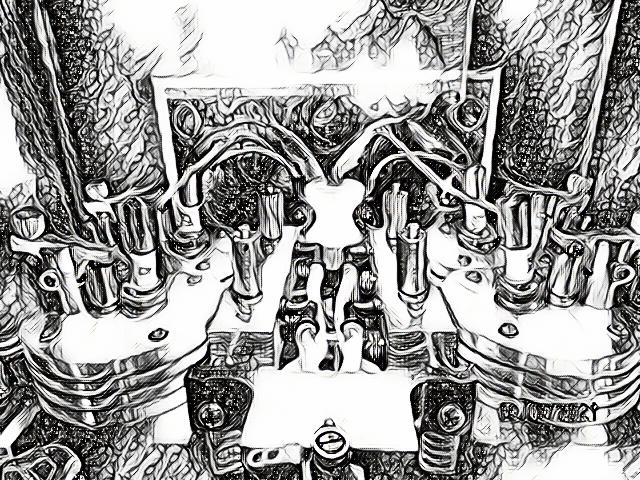