- Joined
- Jun 4, 2008
- Messages
- 3,294
- Reaction score
- 636
I recently bought some 1-1/4" brass round via eBay for the cylinders, and since they arrived I decided to make the first one to see if my imagined machining sequence would work. It's a bit different from John's, but doesn't require any jigs.
The first step is to turn the basic shape. First turn the 3/4" upper section, then drill and ream the bore, and part off at 1" of length. I then reversed the piece in the chuck and faced the cut end. After measuring, I rechucked on the 3/4" section and turned the bottom to 1/2" diameter leaving .100" for the flange. That completes the lathe work for now.
I chucked the 3/4" end in a 5C collet block, mounted the block horizontally in the mill vise, and milled the flange to 3/4" square.
Next I mounted collet block vertically, located the center, and drilled the 4 mounting holes in the corners.
A quick test fit onto the crankcase:
Finally I reversed the piece in the collet block using a 1/2" collet, squared the flanges to the block using my height gauge, and drilled the mounting holes for the head.
Given that I have too many balls in the air project-wise, I probably won't make the other 4 anytime soon. In any case, I still need to tap the holes on the top, and cut the fins. I will definitely be following John's process for setting up the parting tool in the lathe for that. Once the fins are cut, the only remaining worj will be to shorten the 1/2" spigot to .100"; it's made ~2.5" initially to give more surface for chucking in the collet and lathe.
The first step is to turn the basic shape. First turn the 3/4" upper section, then drill and ream the bore, and part off at 1" of length. I then reversed the piece in the chuck and faced the cut end. After measuring, I rechucked on the 3/4" section and turned the bottom to 1/2" diameter leaving .100" for the flange. That completes the lathe work for now.

I chucked the 3/4" end in a 5C collet block, mounted the block horizontally in the mill vise, and milled the flange to 3/4" square.
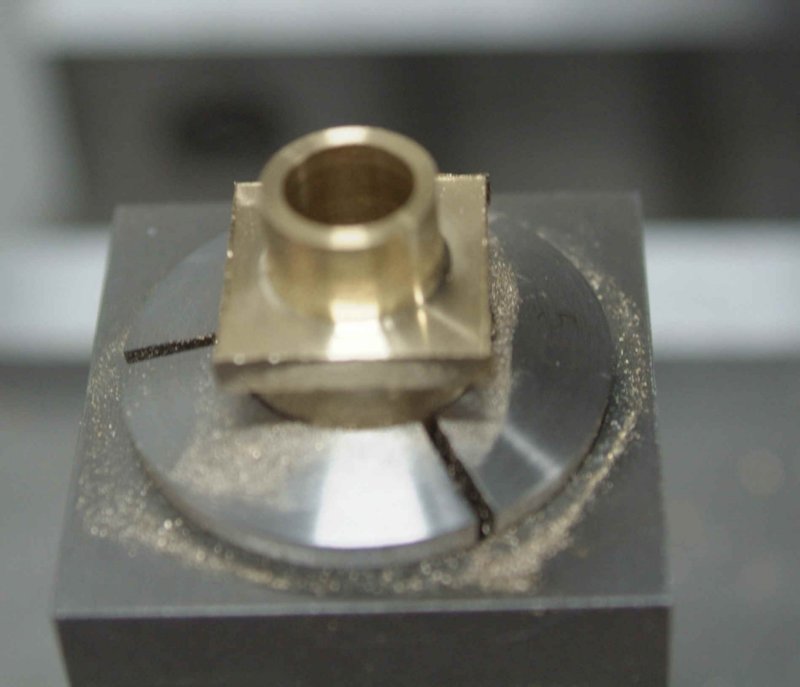
Next I mounted collet block vertically, located the center, and drilled the 4 mounting holes in the corners.
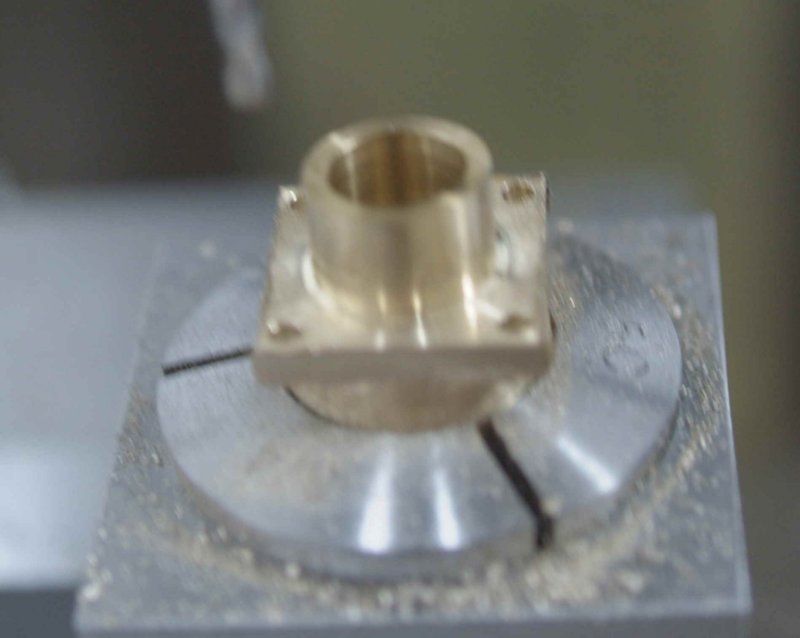
A quick test fit onto the crankcase:
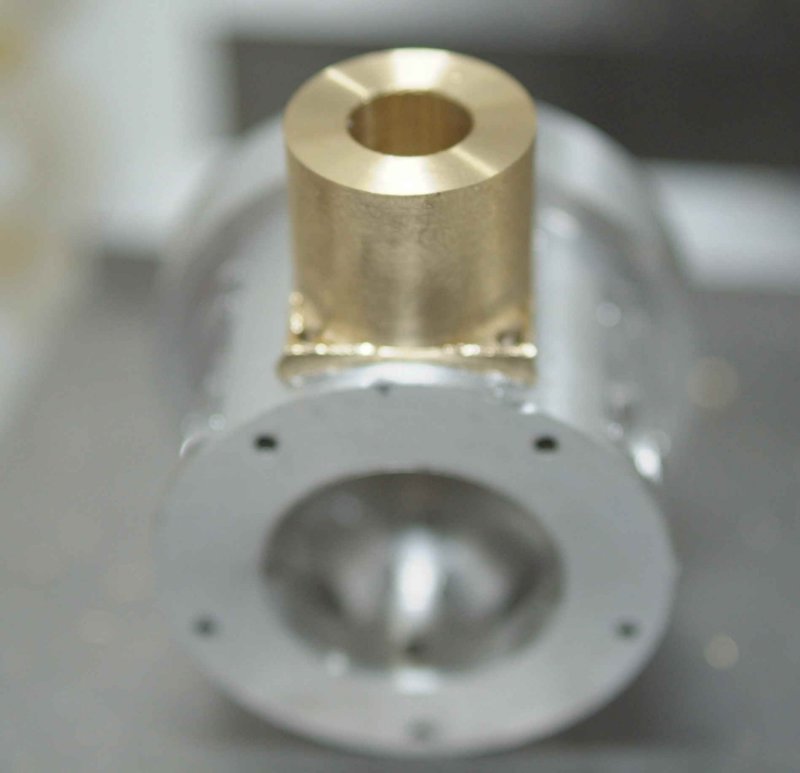
Finally I reversed the piece in the collet block using a 1/2" collet, squared the flanges to the block using my height gauge, and drilled the mounting holes for the head.
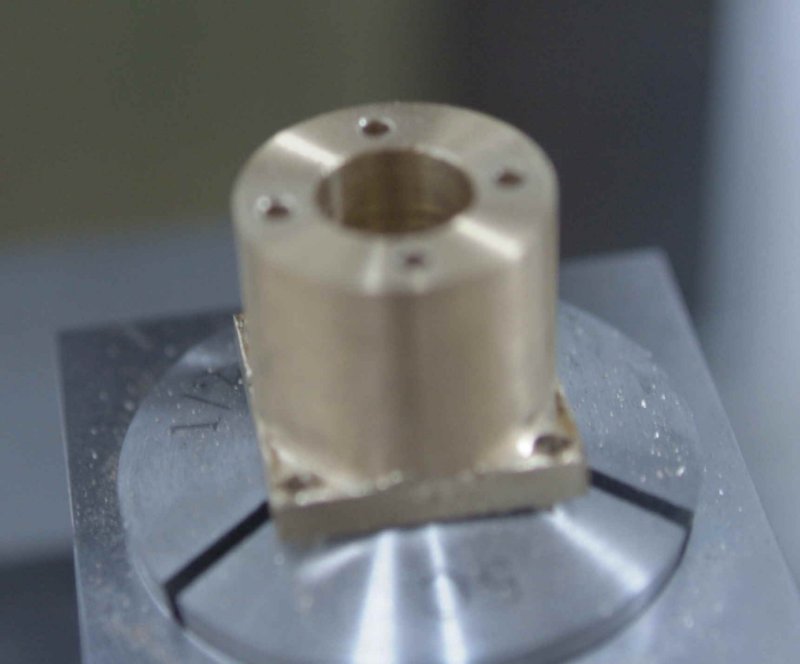
Given that I have too many balls in the air project-wise, I probably won't make the other 4 anytime soon. In any case, I still need to tap the holes on the top, and cut the fins. I will definitely be following John's process for setting up the parting tool in the lathe for that. Once the fins are cut, the only remaining worj will be to shorten the 1/2" spigot to .100"; it's made ~2.5" initially to give more surface for chucking in the collet and lathe.