Here I'm making main bearings. I milled a piece of bearing bronze flat down the center line then placed 2 pieces of such back to back to form a bar again and mounted the combination in the lathe chuck, drilled it, reamed it, turned it and parted to length. I then spent 20 minutes searching the shop floor for the pieces after they flew off. I then owned 2 bearing shells. The next parting job was done in a paper cup. Below is a picture of the shells being parted off. Some solder them together first. I just chucked em. Seemed to work. I overheard Steve mention that's how he did it. In the past I've CNC'd them from plate. This worked better.
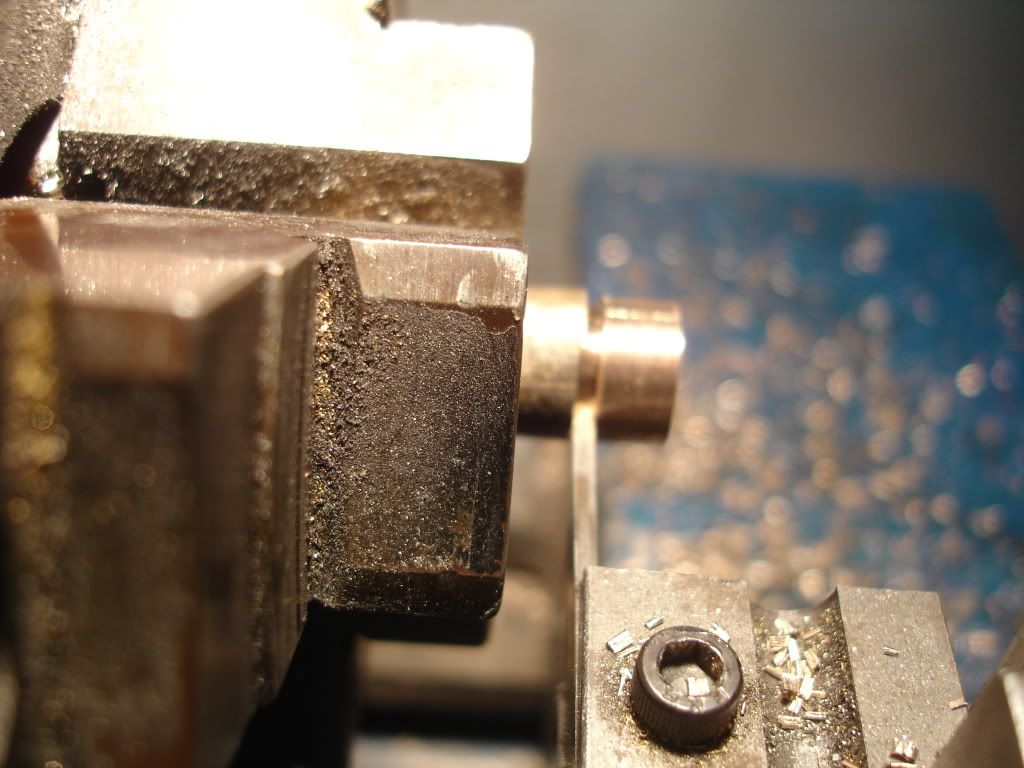