- Joined
- Mar 13, 2012
- Messages
- 583
- Reaction score
- 62
This is a build log for a horizontal Stirling engine designed by Jan Ridders. There are a number of these engines that show up when you do a search on this site. I don't think mine will be much different than the rest, but I'll try to capture the process as I go along.
I got a start today by waterjetting out a blank for the cylinder mounting block. This isn't the ideal tool for the job as I'll demonstrate later, but I don't have a rotary table, and my programming ability on the CNC mill is quite limited.
After I had the blank, I clamped it up and fly cut it to the correct thickness. (Sorry for the out of focus pictures. I used a different camera than normal, and couldn't see the photos were out of focus until I put them on the computer)
When I cut the blank, I made and undersized hole for the displacer cylinder and more undersized holes for the cylinder flange screws. The plan was to use the mill to cut these holes to size and to accurately locate the blind hole for the power piston. To do this, I had to make a fixture to clamp the part to.
The fixture is just a well used plate of aluminum with the bolt pattern for the displace cylinder flanges drilled. I reamed two of the holes to accept dowel pins, and tapped the other two for 4-40 screws. With the pre-cut holes in the part reamed to slip over the dowel pins, I had a securely held part with a known location.
Then I milled in the hole and pocket for the two cylinders. I could have used a boring head, but programming in a circular pocket ins one of the few things I know how to do with this machine.
To locate the pocket that surrounds the displacer hole on the other side, I simply flipped the part over and rotated it 90 degrees so that it would slip back down over the dowel pins. I had to use a clamp to hold it down this time because the bolt pattern is actually a rectangle, not a square so the threaded holes don't line up after the rotation.
I needed to find a way to clamp the part back in the vise so that the centerline between the cylinders was horizontal in order to mill the notch in the bottom that will accept the mounting bracket. To do this I put the dowel pins through two of the mounting flange holes and let them rest on top of the vise. I used this trick again with two different holes to drill the air passage between the two cylinders.
Now the problem with a waterjet is that the edges of your part have what is essentially a media blasted finish. We use 120 grit abrasive in our machine, and the edges come out uniform, but with a heavily textured finish. This is a bit of a pain if you want to have a polished finish in the end. (Yeah, I know. You guys all feel sorry for me now
)
An hour and a half with a file and then successive wet sanding got me to this. This is to 400 grit. I'll have to go a bit further to get the level of polish I want.
Well, that's all for now...
I got a start today by waterjetting out a blank for the cylinder mounting block. This isn't the ideal tool for the job as I'll demonstrate later, but I don't have a rotary table, and my programming ability on the CNC mill is quite limited.
After I had the blank, I clamped it up and fly cut it to the correct thickness. (Sorry for the out of focus pictures. I used a different camera than normal, and couldn't see the photos were out of focus until I put them on the computer)
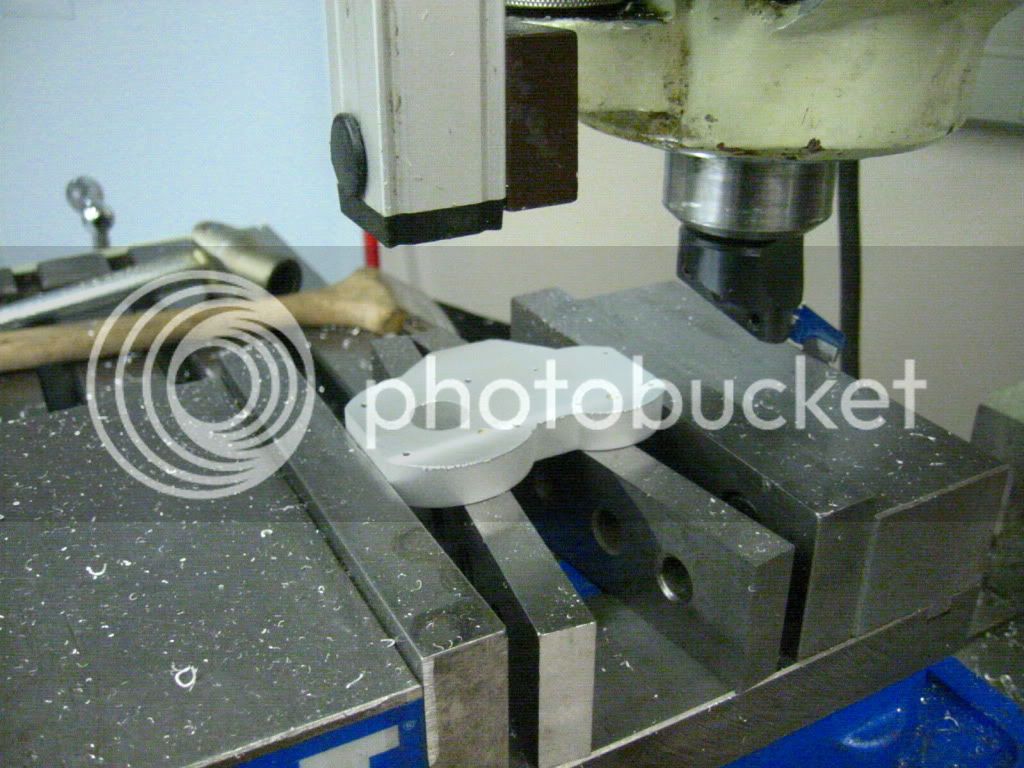
When I cut the blank, I made and undersized hole for the displacer cylinder and more undersized holes for the cylinder flange screws. The plan was to use the mill to cut these holes to size and to accurately locate the blind hole for the power piston. To do this, I had to make a fixture to clamp the part to.
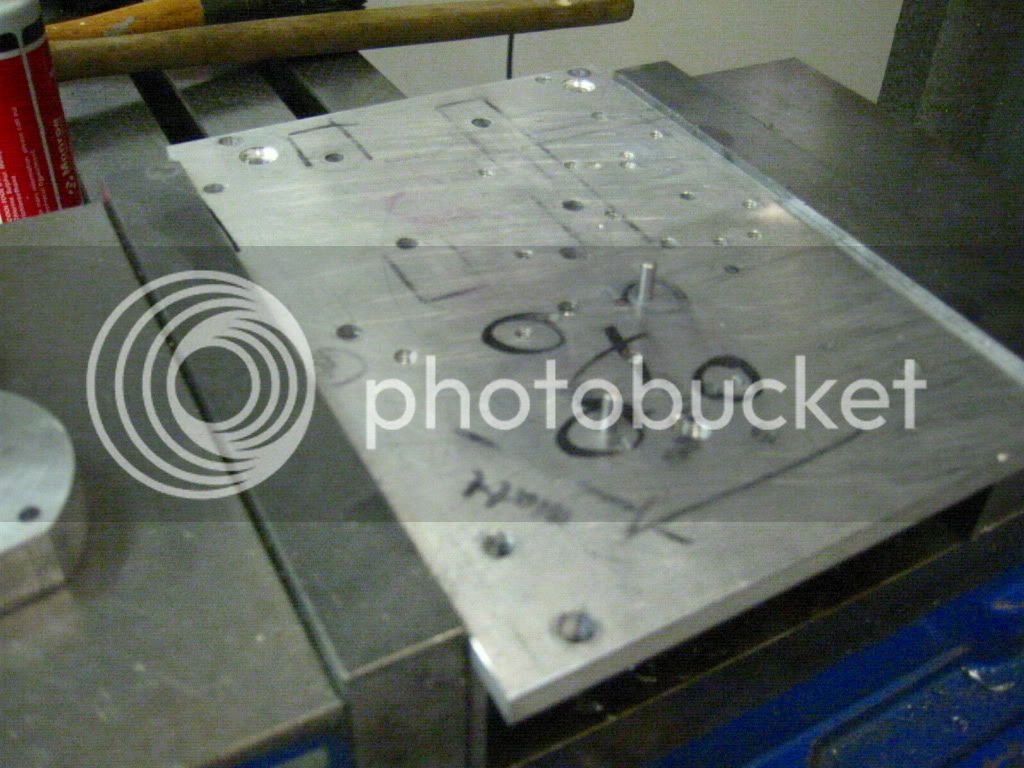
The fixture is just a well used plate of aluminum with the bolt pattern for the displace cylinder flanges drilled. I reamed two of the holes to accept dowel pins, and tapped the other two for 4-40 screws. With the pre-cut holes in the part reamed to slip over the dowel pins, I had a securely held part with a known location.
Then I milled in the hole and pocket for the two cylinders. I could have used a boring head, but programming in a circular pocket ins one of the few things I know how to do with this machine.

To locate the pocket that surrounds the displacer hole on the other side, I simply flipped the part over and rotated it 90 degrees so that it would slip back down over the dowel pins. I had to use a clamp to hold it down this time because the bolt pattern is actually a rectangle, not a square so the threaded holes don't line up after the rotation.
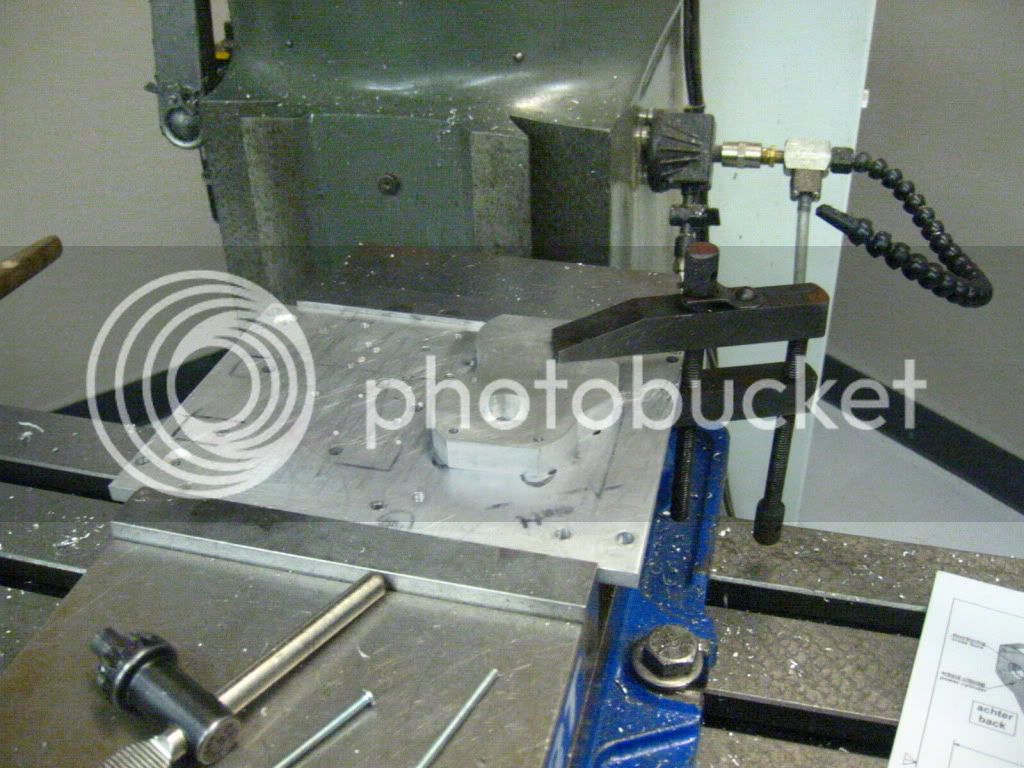
I needed to find a way to clamp the part back in the vise so that the centerline between the cylinders was horizontal in order to mill the notch in the bottom that will accept the mounting bracket. To do this I put the dowel pins through two of the mounting flange holes and let them rest on top of the vise. I used this trick again with two different holes to drill the air passage between the two cylinders.
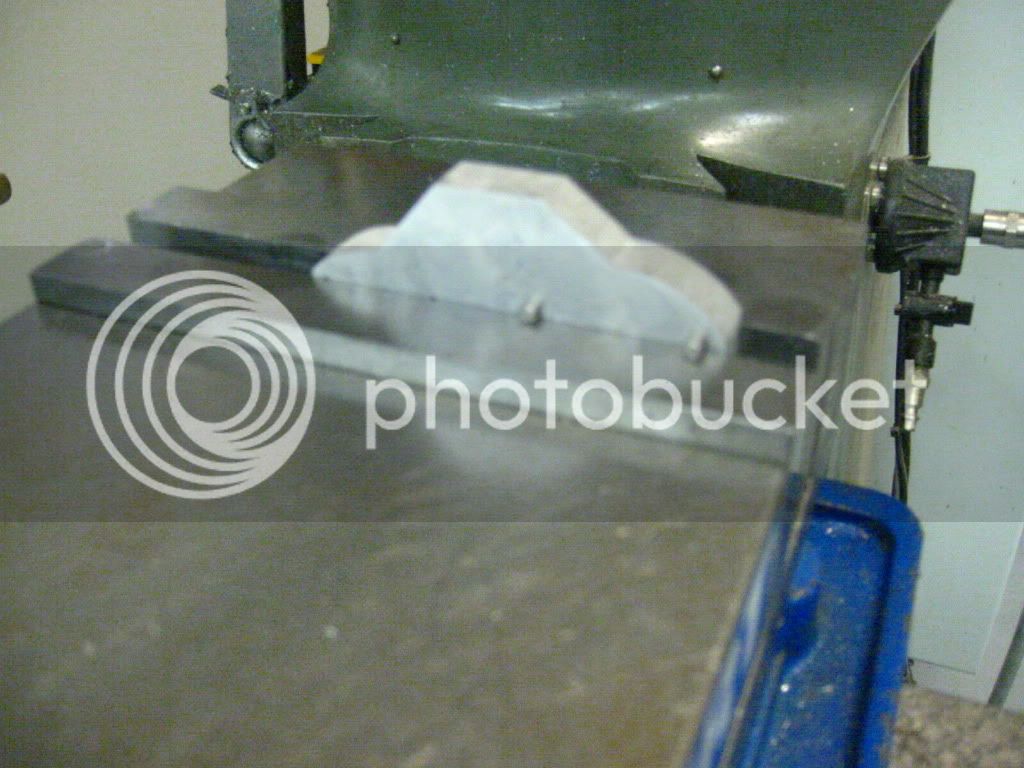
Now the problem with a waterjet is that the edges of your part have what is essentially a media blasted finish. We use 120 grit abrasive in our machine, and the edges come out uniform, but with a heavily textured finish. This is a bit of a pain if you want to have a polished finish in the end. (Yeah, I know. You guys all feel sorry for me now
An hour and a half with a file and then successive wet sanding got me to this. This is to 400 grit. I'll have to go a bit further to get the level of polish I want.
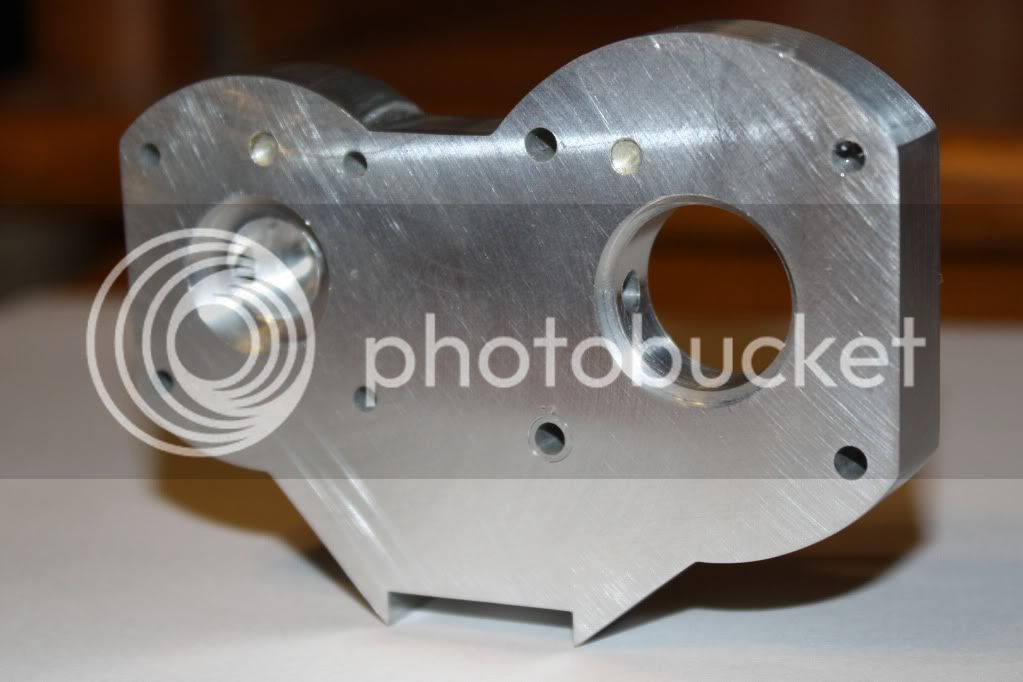
Well, that's all for now...