hello again!
I been a little lazy the past days, lets say like a little break..
After finishing the main structure (the columns, base and the piece that I still dont know how is called ???) I decided to machine all the cylinder parts before weld the main frame, the reason is to be able to make some sort of guide to be able to align square and-in position, the cylinder with respect to the base..
before that I will machine all the main pieces, now I start with the cylinder:
the material is the same that before, but I realize that I will need some special turning tool to be able to machine the smaller diameter, with this tool I will no need the use of a rigth and left hand turning tools..
(the pictures will tell better)
and finish! a new tool is welcome to my life! 8) (but because is a newcomer will no earn its own dedicated QCTP holder yet...and until I can sharpen my end-mills, I think it will be a long waiting for this new fellow, meanwhile it will have to borrow some tool-holder of another more veteran turning tool)
the bigger diameter is machined, now I will machine the smaller one!
And now let's see if it work (I would like to grind the tip of the HSS bit a lot more, and reduce to the half of the width, but my bench grinder wheel is way off-center, and with one hand I have to grab the machine and with the other grind the bit, so it was a little dificult :
(almost all my HSS grinder operations are made in a sand belt) but to remove that much, it can be done without a grinder wheel)
if I would be machining steel, I will just turn off the lathe and go to sleep.. but is brass!! so lets give an oportunity :big:
It worked fine!, but the final finish were mmh.. like a cast finish, like pores, but very slightly, some sand paper and the surface get shinny and regular, so no problem at all! 8)
Remember the boring bar that saved my day? 8)
the inner diameter should be 17.00mm, and again with a lot of patience I measure with my telescopic gauge, a micrometer + pin and a caliper, the final cut was made at 2000 RPM and with several pases, the final diameter was arround 17.02 and 17.04 mm as far I can measure, and a very smooth finish, I still can see the tool marks, but I cant feel it with my fingers, so Im satisfied ;D
Now I get back to the emmm that piece ??? I made before, again I trust my screwless vise, and with a little trigonometry I drill the four holes, with no rotary table!, first I center the piece with the spindle using a test dial indicator, arround +/-0.01mm of tolerance, then lock the Y axis, with a edge-finder I get the X axis zeroed at the left extreme of the piece, and then I drill the first two holes (the one of the left, because they have the same X coordinate), and the other two in the same way..
And probably you guessed right, I got a DRO in the Y axis, without him this would be a painfull operation...
and now returning to the cylinder, I use a fly cutter to clean the band saw face, the turned face will be the bottom one thats assembly with the main frame, the milled face will be the top one
and finally I could resist to make a little preview of the engine, the "flywheel" is a old pulley rescued from the scrapyard, when I look at this pulley in the yard I said "mm this one will made a very nice flywheel", then I bought it..
It look good, but the flywheel is the last think I will make, so for this time its only a provisionary wheel ;D
thanks for all the good comments!
I will keep the build process comming!
Saludos!
I been a little lazy the past days, lets say like a little break..
After finishing the main structure (the columns, base and the piece that I still dont know how is called ???) I decided to machine all the cylinder parts before weld the main frame, the reason is to be able to make some sort of guide to be able to align square and-in position, the cylinder with respect to the base..
before that I will machine all the main pieces, now I start with the cylinder:
the material is the same that before, but I realize that I will need some special turning tool to be able to machine the smaller diameter, with this tool I will no need the use of a rigth and left hand turning tools..
(the pictures will tell better)
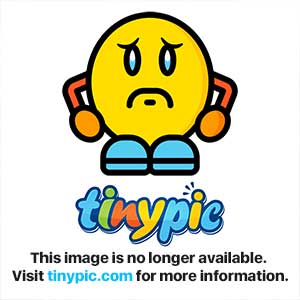
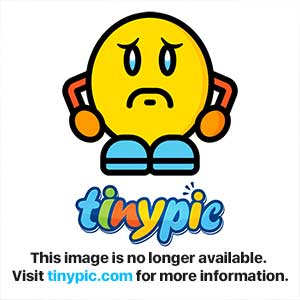
and finish! a new tool is welcome to my life! 8) (but because is a newcomer will no earn its own dedicated QCTP holder yet...and until I can sharpen my end-mills, I think it will be a long waiting for this new fellow, meanwhile it will have to borrow some tool-holder of another more veteran turning tool)
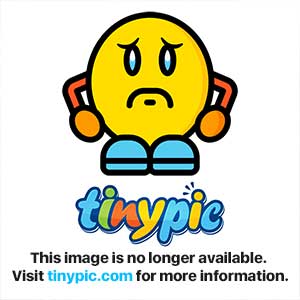
the bigger diameter is machined, now I will machine the smaller one!
And now let's see if it work (I would like to grind the tip of the HSS bit a lot more, and reduce to the half of the width, but my bench grinder wheel is way off-center, and with one hand I have to grab the machine and with the other grind the bit, so it was a little dificult :
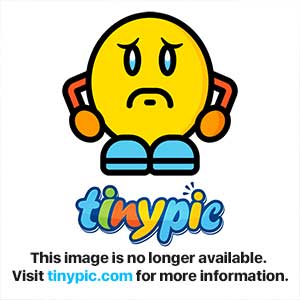
if I would be machining steel, I will just turn off the lathe and go to sleep.. but is brass!! so lets give an oportunity :big:
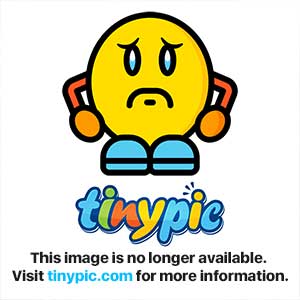
It worked fine!, but the final finish were mmh.. like a cast finish, like pores, but very slightly, some sand paper and the surface get shinny and regular, so no problem at all! 8)
Remember the boring bar that saved my day? 8)
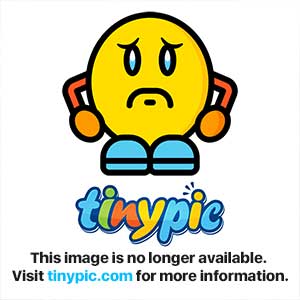
the inner diameter should be 17.00mm, and again with a lot of patience I measure with my telescopic gauge, a micrometer + pin and a caliper, the final cut was made at 2000 RPM and with several pases, the final diameter was arround 17.02 and 17.04 mm as far I can measure, and a very smooth finish, I still can see the tool marks, but I cant feel it with my fingers, so Im satisfied ;D
Now I get back to the emmm that piece ??? I made before, again I trust my screwless vise, and with a little trigonometry I drill the four holes, with no rotary table!, first I center the piece with the spindle using a test dial indicator, arround +/-0.01mm of tolerance, then lock the Y axis, with a edge-finder I get the X axis zeroed at the left extreme of the piece, and then I drill the first two holes (the one of the left, because they have the same X coordinate), and the other two in the same way..
And probably you guessed right, I got a DRO in the Y axis, without him this would be a painfull operation...
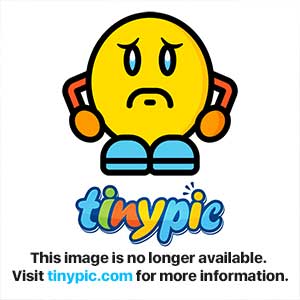
and now returning to the cylinder, I use a fly cutter to clean the band saw face, the turned face will be the bottom one thats assembly with the main frame, the milled face will be the top one
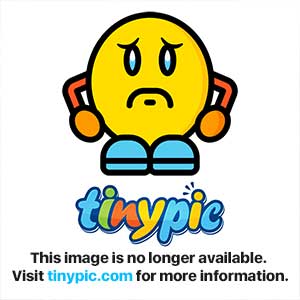
and finally I could resist to make a little preview of the engine, the "flywheel" is a old pulley rescued from the scrapyard, when I look at this pulley in the yard I said "mm this one will made a very nice flywheel", then I bought it..
It look good, but the flywheel is the last think I will make, so for this time its only a provisionary wheel ;D
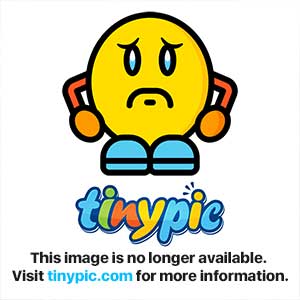
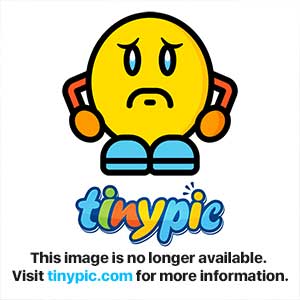
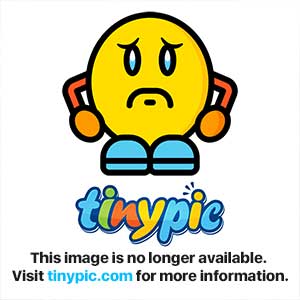
thanks for all the good comments!
I will keep the build process comming!
Saludos!