Bit of background first.
Making a raft of HTD 5M series pulleys, mill a stick out on the 4th axis CNC in two sizes 40 teeth and 20 teeth for 2:1 reductions for the CNC conversions.
These are dead easy to do, get the OD from tables or off the HPC web site and for the 5M series you need a 1/8" ball nose cutter plunged in to a depth of 2.16mm - job done.
Now the tricky bit, ball nose cutters are a ***** to traverse with because as the radius gets to centre there isn't much clearance and right on centre that part of the cutter isn't rotating, so feeds have to be very conservative.
The only cutters I had on stock were long reach two flute Chinese cutters and the chances of breaking one of these with 20mm of flute length will either be high or very boring if done in 17,457 passes [ approx ]
So brilliant brainwave, not seen this posted before but it's that simple it must have been done before.
Took a piece of 10mm steel and cut and faced it both ends equal to 5mm less than the length of the cutter, centre driled it and drilled one end 1/4" to a depth just over the shank length and the other end was drilled 1/8" to match the cutter. Slot cut in the side with a hacksaw and the cutter inserted so that it stuck proud by 5mm.
This way only 5mm of the cutter is unsupported.
Started off doing it in two passes but them swapped to full depth with no problems.
End results.
John S.
Making a raft of HTD 5M series pulleys, mill a stick out on the 4th axis CNC in two sizes 40 teeth and 20 teeth for 2:1 reductions for the CNC conversions.
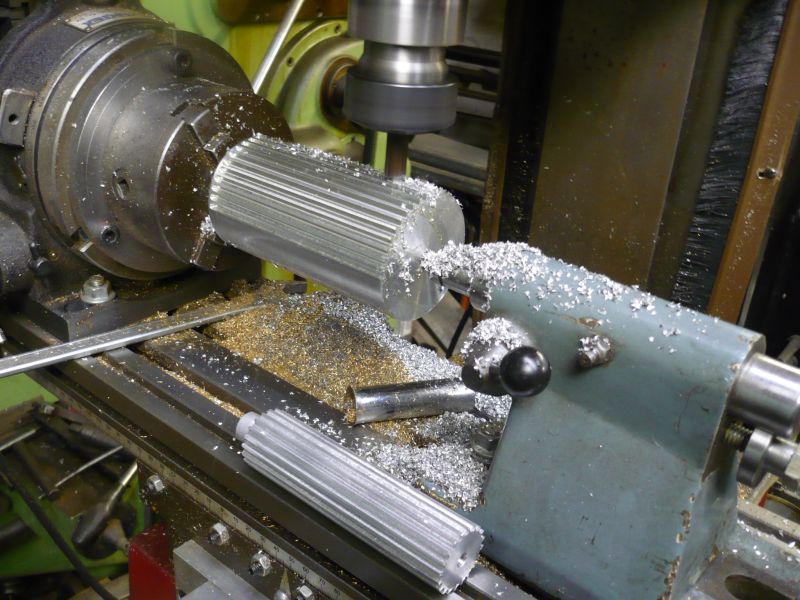
These are dead easy to do, get the OD from tables or off the HPC web site and for the 5M series you need a 1/8" ball nose cutter plunged in to a depth of 2.16mm - job done.
Now the tricky bit, ball nose cutters are a ***** to traverse with because as the radius gets to centre there isn't much clearance and right on centre that part of the cutter isn't rotating, so feeds have to be very conservative.
The only cutters I had on stock were long reach two flute Chinese cutters and the chances of breaking one of these with 20mm of flute length will either be high or very boring if done in 17,457 passes [ approx ]
So brilliant brainwave, not seen this posted before but it's that simple it must have been done before.
Took a piece of 10mm steel and cut and faced it both ends equal to 5mm less than the length of the cutter, centre driled it and drilled one end 1/4" to a depth just over the shank length and the other end was drilled 1/8" to match the cutter. Slot cut in the side with a hacksaw and the cutter inserted so that it stuck proud by 5mm.
This way only 5mm of the cutter is unsupported.
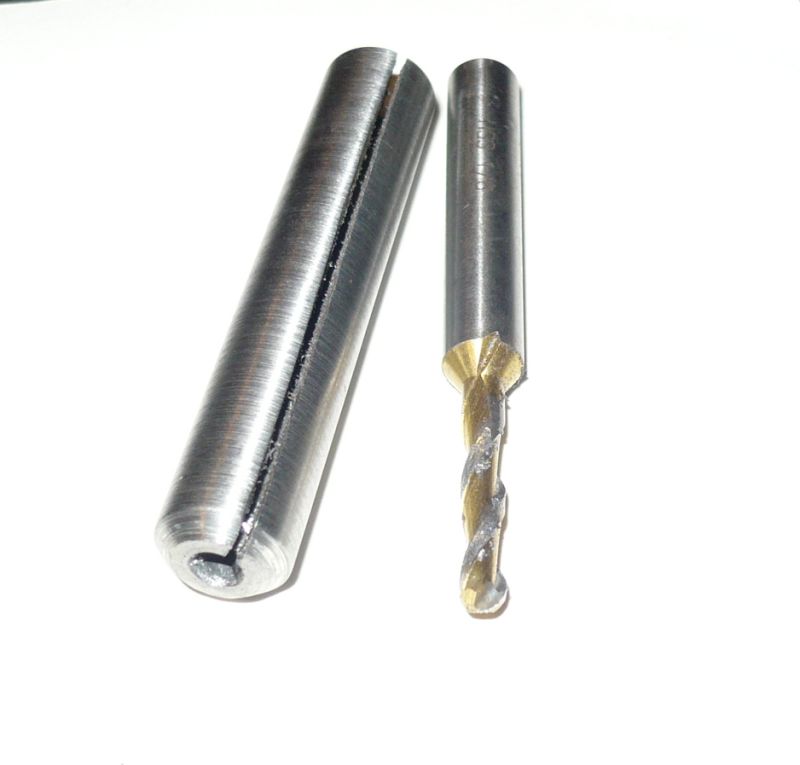
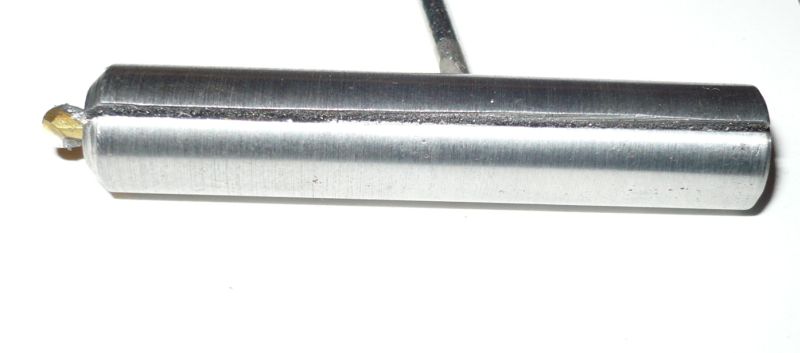
Started off doing it in two passes but them swapped to full depth with no problems.
End results.
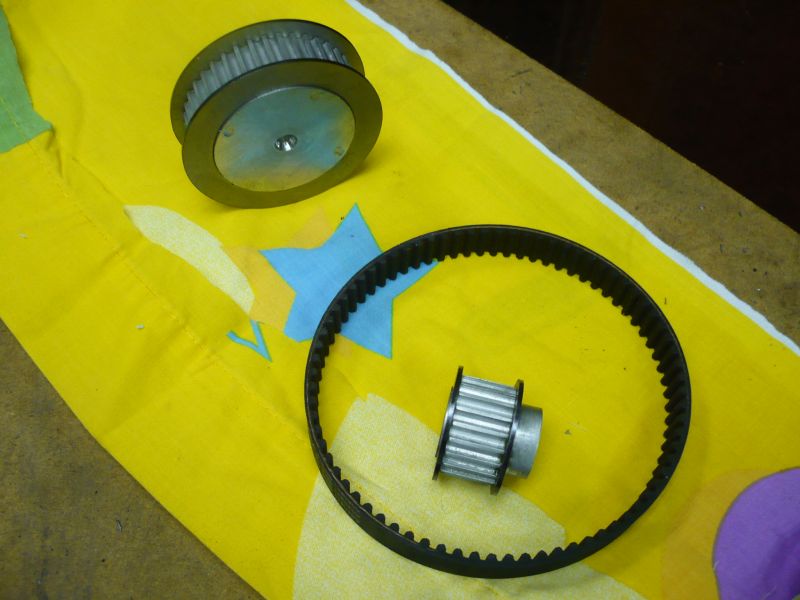
John S.