- Joined
- Jun 12, 2012
- Messages
- 88
- Reaction score
- 68
Hi Brian --
Great to hear from you, and especially your reassurance on the cam issue. Been giving me nightmares, that...visions of finishing this project but with all the valves just sitting there, fast asleep...
You're way ahead of me it seems, I've just been at this project for a couple of months...here's the story so far:
The oil pump assembly is also done, and I hope to be nibbling away at the cam cover this weekend, as long as some proper-sized slitting saws arrive in time. I've also been taking pics fairly frequently, and I'll try to organize a little w-i-p series over the next few days. Would love to see yours too.
Also can't wait to hear of your experience with the cam issue. A lot of potential discussion points come to mind, actually.
All best...
Michael T
Great to hear from you, and especially your reassurance on the cam issue. Been giving me nightmares, that...visions of finishing this project but with all the valves just sitting there, fast asleep...
You're way ahead of me it seems, I've just been at this project for a couple of months...here's the story so far:
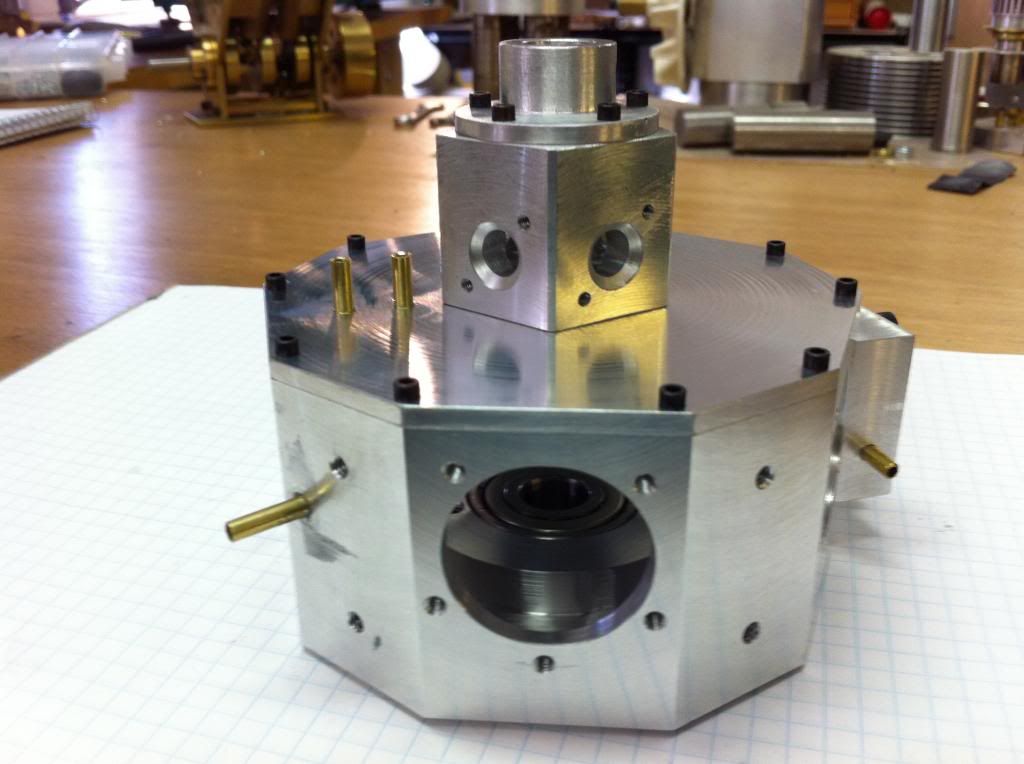
The oil pump assembly is also done, and I hope to be nibbling away at the cam cover this weekend, as long as some proper-sized slitting saws arrive in time. I've also been taking pics fairly frequently, and I'll try to organize a little w-i-p series over the next few days. Would love to see yours too.
Also can't wait to hear of your experience with the cam issue. A lot of potential discussion points come to mind, actually.
All best...
Michael T
Last edited: