I am just in the initial stages of marking out cut lines on the piece of 2 1/2" square piece of aluminum which will become my cooling tower. Since the bore will be somewhat complicated by being larger internally than at the outside ends, it can't be done with a conventional boring head. So--I dragged the model over onto my lathe faceplate. this immediately shows me two things. #1--the part will fit okay for turning, as it doesn't stick out beyond the edges of the faceplate. #2---I don't want to trim it to length until after I have bored it. By leaving it full length, I can put a bolt thru the top (above what is shown as the open end of the water reservoir) to bolt it to the faceplate, then trim it to length after it has been bored.
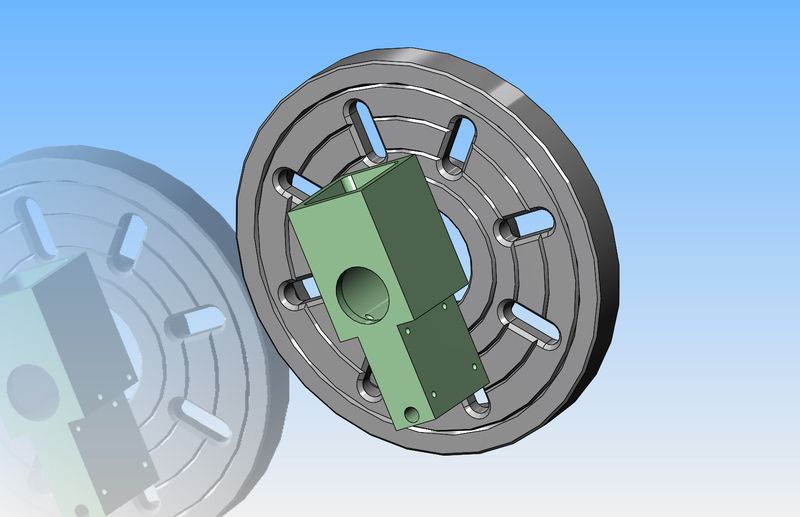