Well, I have finally found some time to start another engine. This will be my first attempt at posting a build here so please keep this in mind as we go. Any helpful suggestions on my posting will be gratefully accepted.
I like to build my own designs and I have been thinking about this one for a while now. It will be a twin cylinder IC engine of four stroke design. I have wanted to build an engine with all roller bearing construction for a while now and this is what I have come up with. I don't normally do much drawing before I start and this one will be no different. I hope you will be able to follow along and as it takes shape it should become much clearer to understand.
I picked up a couple of 2:1 bevel gear sets at an engine show a while back and tried to figure how I could incorporate them into an engine. What I came up with is the smaller gears which are the pinions are on integral shafts which will have crankdisks attached to the outboard ends. The pinions will act on the larger ring gear which the flywheel will be attached to.
So the flywheel will rotate at half engine speed with the exhaust valve cam attached to the other end of this shaft. One cam lobe will operate both cylinders. This will be a slow speed throttle governed engine so I will use atmospheric intake valves. The first pic I have is of the work I have finished so far( not much ).
Here I have one pinion assembly put together and the other in pieces. These are constructed like the pinion supports in Ford 9" differentials.
I like to build my own designs and I have been thinking about this one for a while now. It will be a twin cylinder IC engine of four stroke design. I have wanted to build an engine with all roller bearing construction for a while now and this is what I have come up with. I don't normally do much drawing before I start and this one will be no different. I hope you will be able to follow along and as it takes shape it should become much clearer to understand.
I picked up a couple of 2:1 bevel gear sets at an engine show a while back and tried to figure how I could incorporate them into an engine. What I came up with is the smaller gears which are the pinions are on integral shafts which will have crankdisks attached to the outboard ends. The pinions will act on the larger ring gear which the flywheel will be attached to.
So the flywheel will rotate at half engine speed with the exhaust valve cam attached to the other end of this shaft. One cam lobe will operate both cylinders. This will be a slow speed throttle governed engine so I will use atmospheric intake valves. The first pic I have is of the work I have finished so far( not much ).
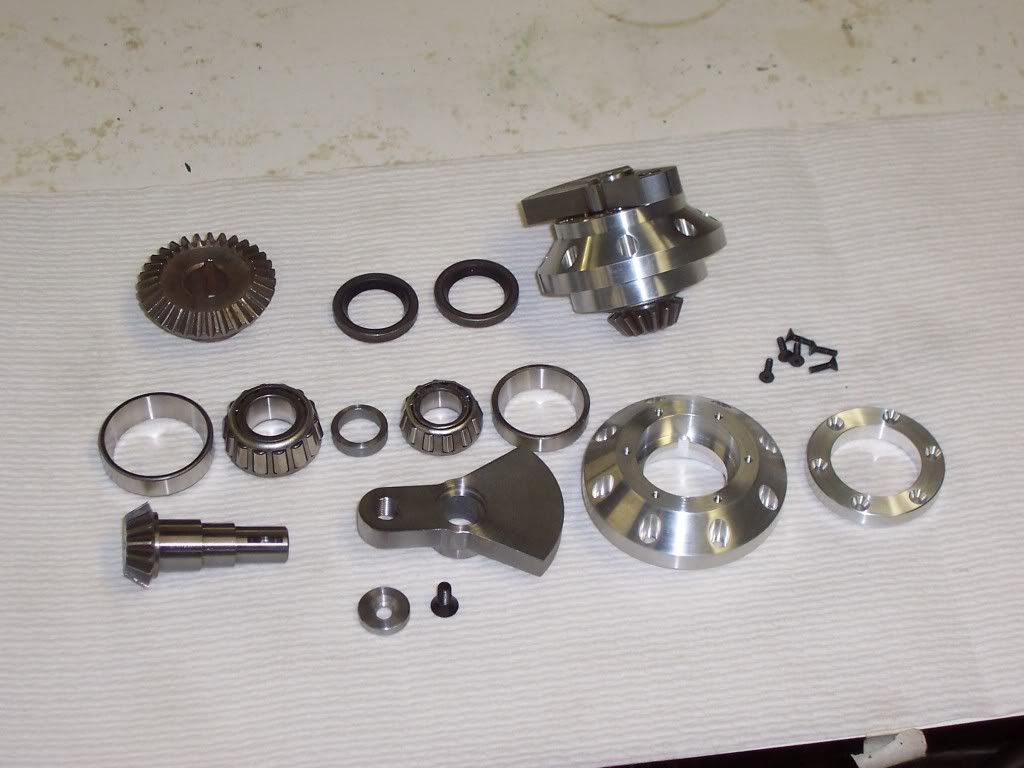
Here I have one pinion assembly put together and the other in pieces. These are constructed like the pinion supports in Ford 9" differentials.