Ever since I started using a four jaw chuck, about 12 years ago, I have used a 1/4" diameter rod x 15" long with a point turned on one end. The pointed end is placed into a "center punch mark" on the piece I want to center in the four jaw chuck, and the other end is held in a tailstock mounted chuck. Then a dial indicator is brought in to bear on the 1/4" rod just clear of the part in the chuck, and the chuck is turned by hand and adjusted ---and adjusted---and adjusted---until the dial indicator reads "0" for a full 360 degrees of rotation. This method has served me well, but about 3 months ago I wanted to center a piece which had a 3/8" hole that I wanted to bore out to marginally oversize. I didn't want to use a larger diameter rod, because the larger in diameter the rod is, the less willing it is to flex. I thought about it for a while and then come up with this modification to my 1/4" diameter rod. This works great, the rod can still deflect easily, and I can center accurately on holes up to 9/16" diameter. Note that in order to do this, you can't use the typical pointed end on a dial indicator. It has to be unscrewed and replaced by a larger, flat "anvil" on the end
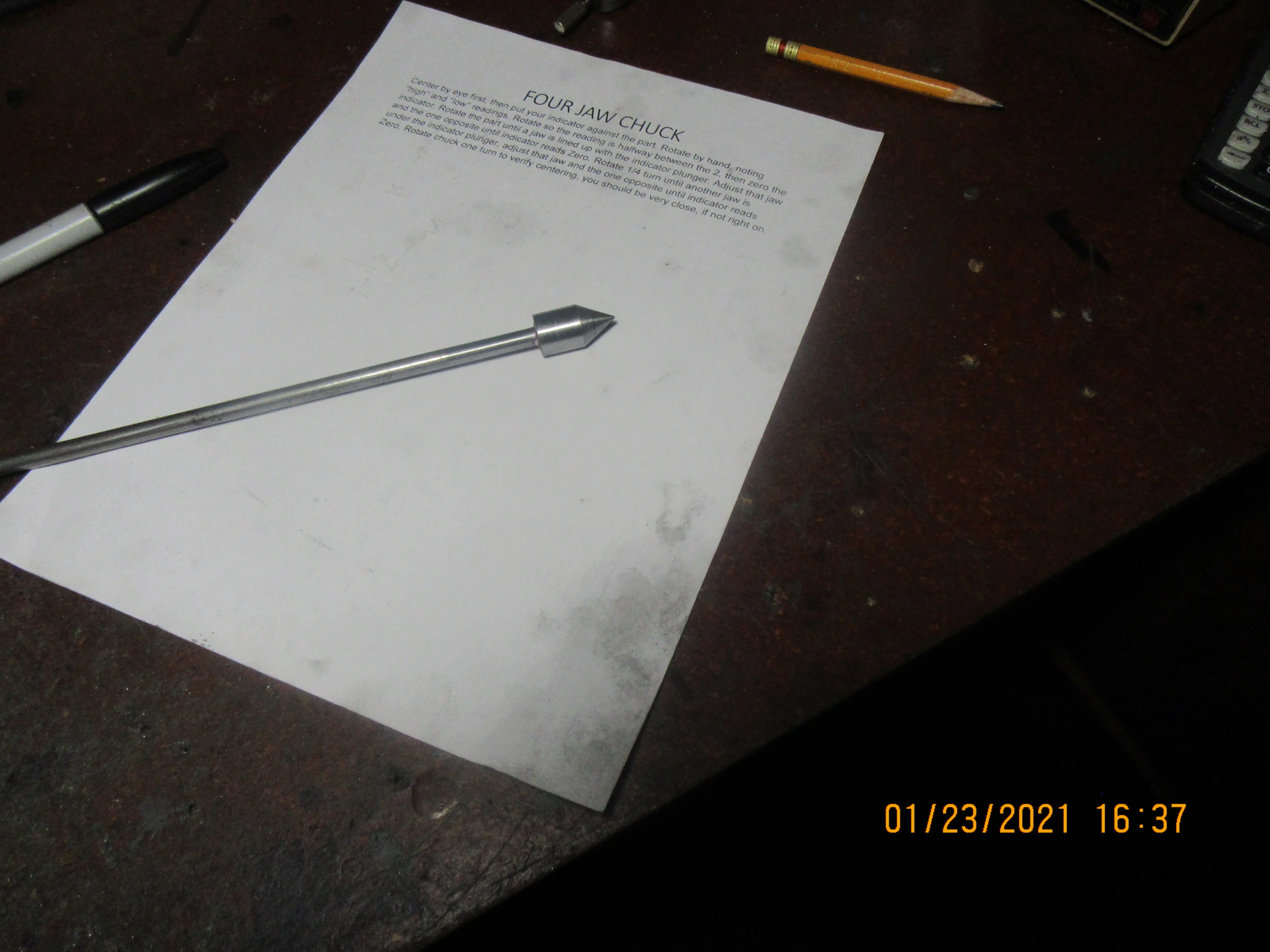
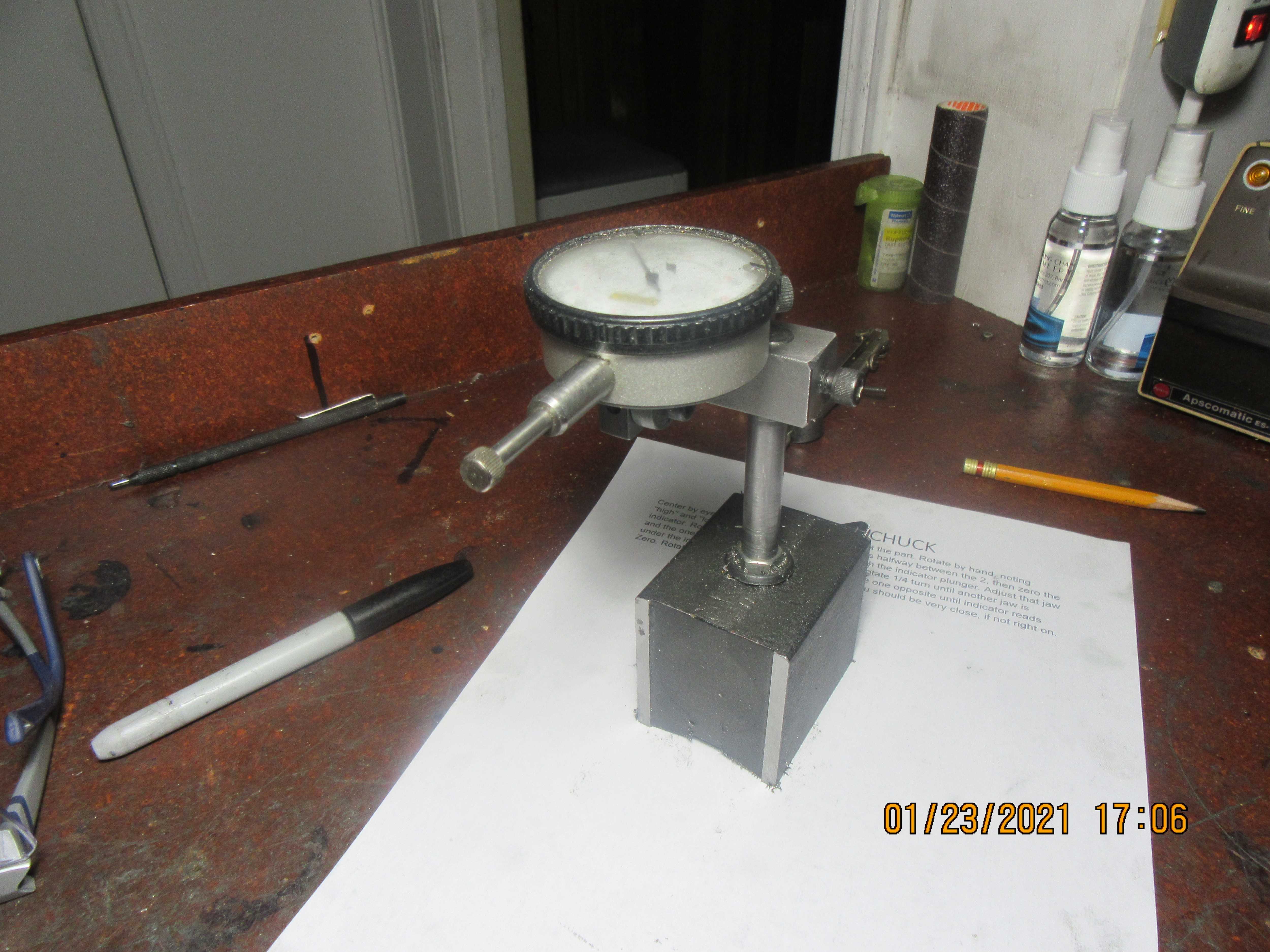
Last edited: