arnoldb
Well-Known Member
- Joined
- Apr 8, 2009
- Messages
- 1,792
- Reaction score
- 12
CC, Rob: many thanks - I really appreciate your input.
CC:
Rob:
On my other build (my "first" engine - that is now rapidly moving down the line :-[ ), I made a "wrong" connecting rod from silver steel (the flats on the head were not parallel to the shaft).
Cheap miser that I am, instead of throwing it away, I cut off the head through the hole, then ground the profile as needed from what was left, and then hardened it. I didn't bother to temper it again, just slipped it over the oilstone a couple of times to get some nice cutting surfaces. For brass and aluminium, that should be OK, but if I need to do steel or interrupted cuts with it, I'll have to temper it a bit...
Crap-O-Cad attached of turning a con rod into a boring bar - might be useful for someone , but you will have to turn your head a bit (sorry)
Regards, Arnold
[Edit: turned the picture right way around]
CC:
- Thank you; I feel honoured, but there are a LOT of other members of HMEM who gives a better target to aim at; I'm still trying to aim theregives us something to aim at
Rob:
Uhm, no... :hDe: Uhm... I cheated :-[did you forge over the end of the silver steel first , then grind it to shape ?
On my other build (my "first" engine - that is now rapidly moving down the line :-[ ), I made a "wrong" connecting rod from silver steel (the flats on the head were not parallel to the shaft).
Cheap miser that I am, instead of throwing it away, I cut off the head through the hole, then ground the profile as needed from what was left, and then hardened it. I didn't bother to temper it again, just slipped it over the oilstone a couple of times to get some nice cutting surfaces. For brass and aluminium, that should be OK, but if I need to do steel or interrupted cuts with it, I'll have to temper it a bit...
Crap-O-Cad attached of turning a con rod into a boring bar - might be useful for someone , but you will have to turn your head a bit (sorry)
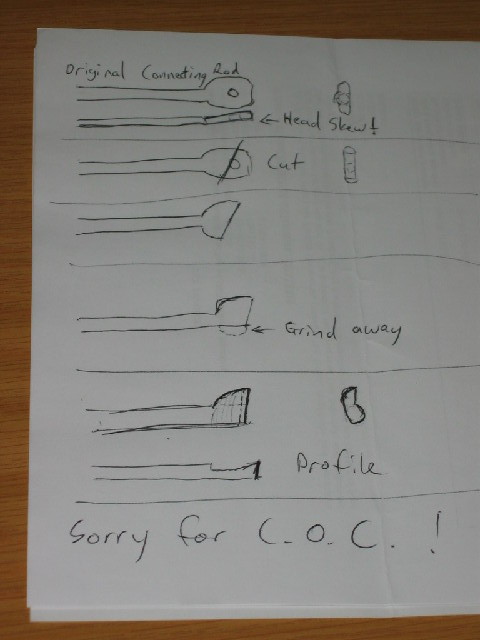
Regards, Arnold
[Edit: turned the picture right way around]