For the base of the engine I had intended to use a length of 125x65x15 PFC (parallel flange channel) that I had conviently over ordered on an order for some other work related structural steel. Having now got pictures of the actual engine I had to rethink my methods therefore I will make the top of the base from 5mm steel plate and the sides from 1 1/2" x 5/8" alloy.
You know when you are building bigger engines because you can't cut right through the part with a hacksaw :
, so the angle grinder with a thin cutting disc was used to complete the cuts and give me a piece approx 5" x17"
After some very basic layout using a pencil and marker the sheet was fixed to the mill table on some MDF packing.
The first job was to add another hold down in the middle of some waste followed by cutting the two holes for the pump and cylinder base using a boring head and their associated fixing holes.
As work progressed I had to reset the plate as its length was just over the 360mm travel of the X3s table. Having studied the old photos again tonight I need to make this rectangular hole larger but its easy enough to reset on the mill.
The final bit of profiling was done on the rotary table as the crank hole needs to have a rounded end where it meets the cylinder base.
And here it is just about done except for a few odd holes and the above mentioned cutout.
J
You know when you are building bigger engines because you can't cut right through the part with a hacksaw :
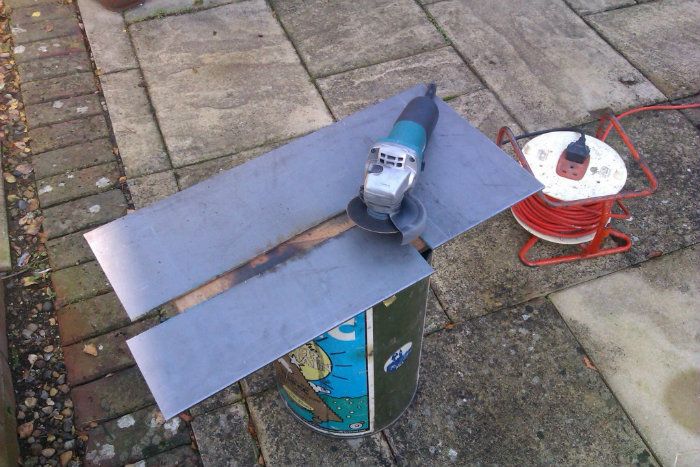
After some very basic layout using a pencil and marker the sheet was fixed to the mill table on some MDF packing.
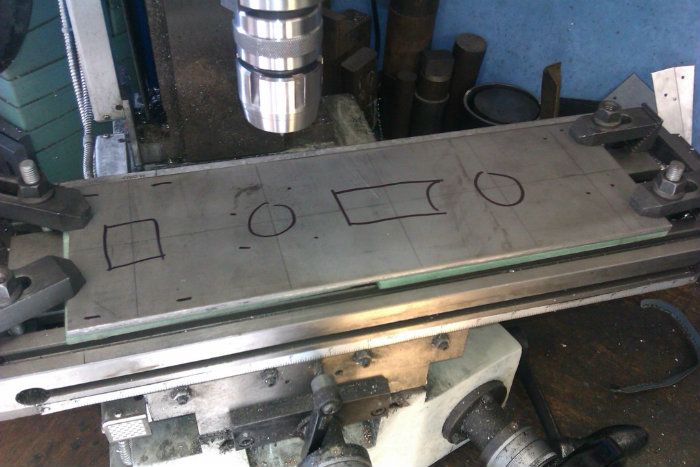
The first job was to add another hold down in the middle of some waste followed by cutting the two holes for the pump and cylinder base using a boring head and their associated fixing holes.
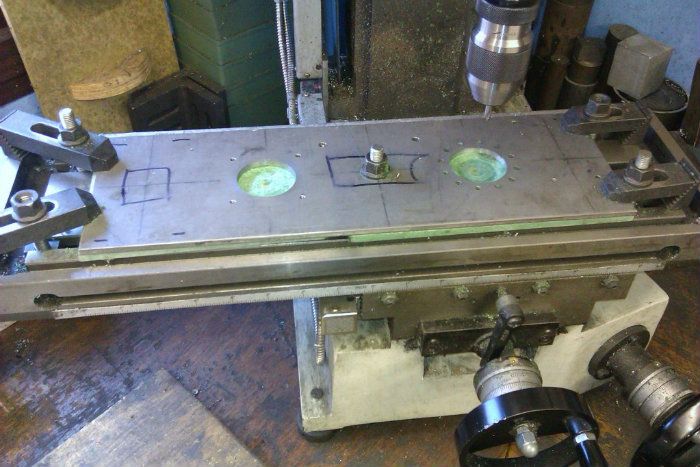
As work progressed I had to reset the plate as its length was just over the 360mm travel of the X3s table. Having studied the old photos again tonight I need to make this rectangular hole larger but its easy enough to reset on the mill.

The final bit of profiling was done on the rotary table as the crank hole needs to have a rounded end where it meets the cylinder base.

And here it is just about done except for a few odd holes and the above mentioned cutout.
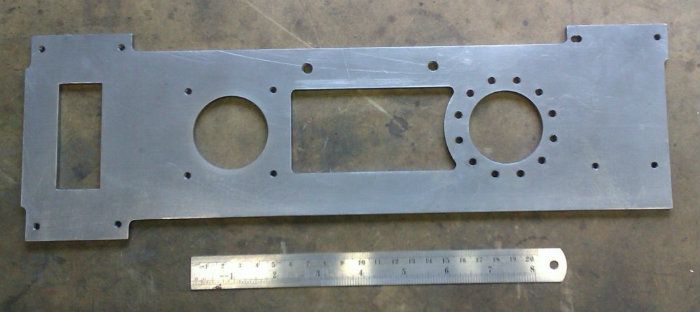
J