Some of you may have seen in the past me mention myintension to build this engine in a bigger size, well Ive started.
It will be based on the 1/12th scale model byAnthony Mount that was serialised in EIM and also reproduced in his secondbook. Plans are also available from BruceEngineering as well as castings.
I intend to double the size to 1/6th scale and havingrecently obtained some photos of the original engine will try to make minetruer to that. This will result in an engine with the following spec.
Length 15 ½
Width 10 ¼
Height 14
Flywheel dia 10 ¾
Bore & stroke 1 7/8x 2
The prototype was quite a small beam engine, most peoplethink of the large waterworks pumping engines when a beam engine is mentionedbut this one was smaller and would likely have been used in a mill or factoryto drive overhead line shafting. Thats why it can be built at a relativelylarge 1/6th scale and still fit the flywheel on my lathe (just).
I probably wont do a bit by bit build but just show some ofthe more interesting parts which will mostly be the fabrication of the itemsthat are supplied as castings in the Bruce model and anything else that I thinkothers may be interested in.
J
It will be based on the 1/12th scale model byAnthony Mount that was serialised in EIM and also reproduced in his secondbook. Plans are also available from BruceEngineering as well as castings.
I intend to double the size to 1/6th scale and havingrecently obtained some photos of the original engine will try to make minetruer to that. This will result in an engine with the following spec.
Length 15 ½
Width 10 ¼
Height 14
Flywheel dia 10 ¾
Bore & stroke 1 7/8x 2
The prototype was quite a small beam engine, most peoplethink of the large waterworks pumping engines when a beam engine is mentionedbut this one was smaller and would likely have been used in a mill or factoryto drive overhead line shafting. Thats why it can be built at a relativelylarge 1/6th scale and still fit the flywheel on my lathe (just).
I probably wont do a bit by bit build but just show some ofthe more interesting parts which will mostly be the fabrication of the itemsthat are supplied as castings in the Bruce model and anything else that I thinkothers may be interested in.
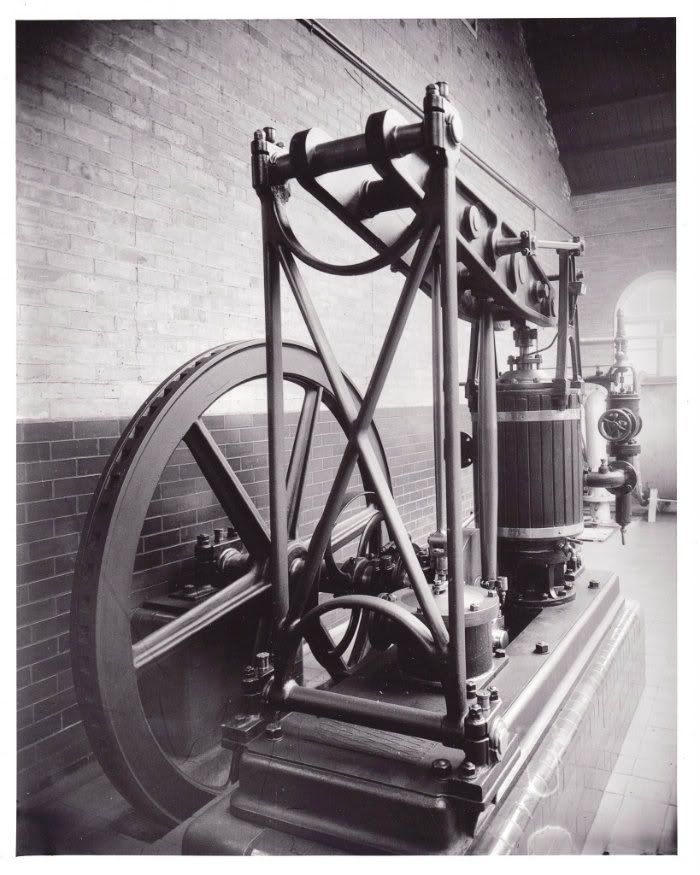
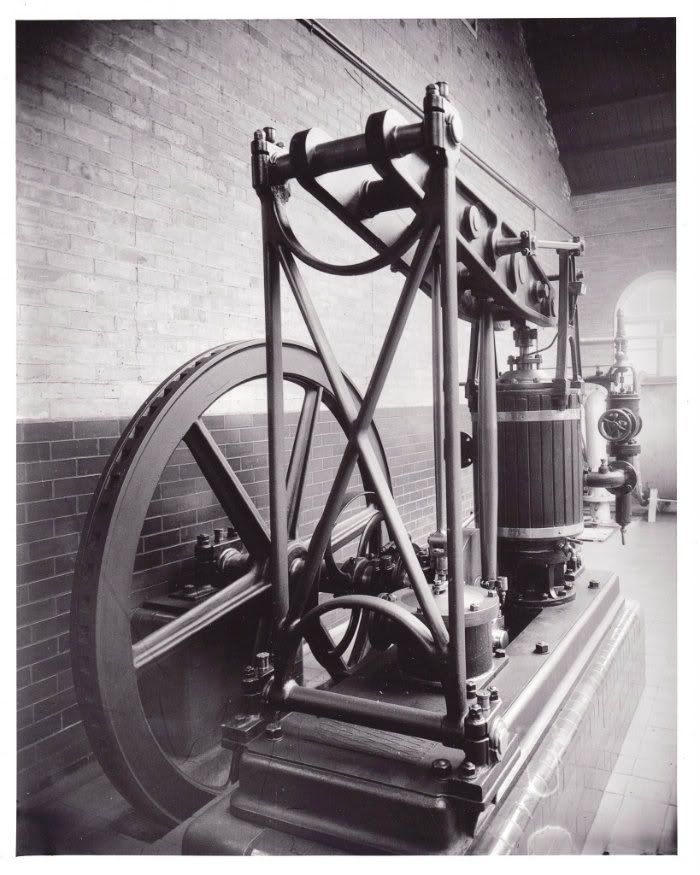
J