Maryak
Well-Known Member
- Joined
- Sep 12, 2008
- Messages
- 4,990
- Reaction score
- 77
Brian,
Almost without exception these engines were controlled by a throttle and a Differential Valve to reverse the direction of rotation. The engines were also full admission with no lap or lead.
I hope this is what you are looking for.
Best Regards
Bob
Almost without exception these engines were controlled by a throttle and a Differential Valve to reverse the direction of rotation. The engines were also full admission with no lap or lead.
I hope this is what you are looking for.
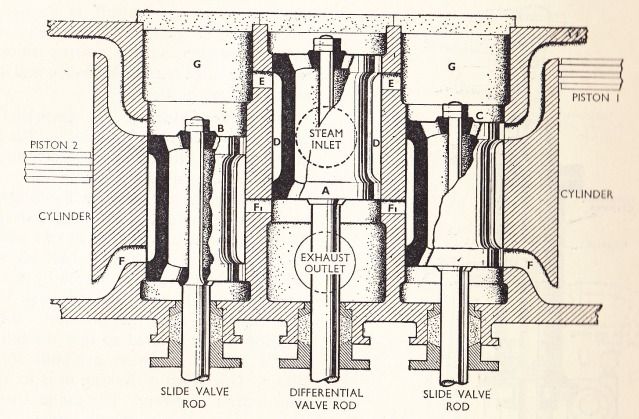
Best Regards
Bob