I ordered up the newest Jan Ridder flame-eater design, and have modeled it all this morning. I have changed metric plate and shaft sizes to the nearest imperial (inch") size that is available and commonly used. This involved juggling a few parts around to compensate for minor differences in dimensions. This is the new design using a stainless cylinder and graphite piston and internal valve. These flame eater engines are notoriously dirty due to soot in the flame being sucked into the cylinder and resulting condensation. I am not in any great hurry to make this engine, but I know how that has worked out in the past. The amount of time I spend in my machine shop is in direct proportion to how much "real" work I have in any given week. ---Brian
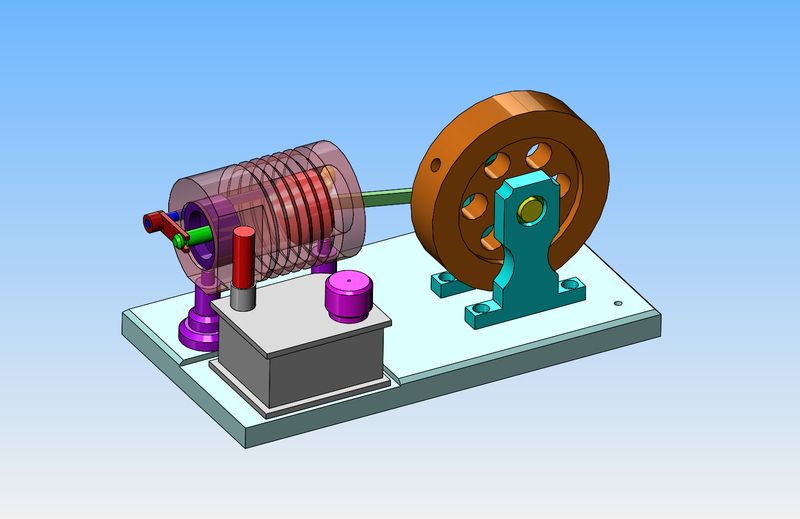
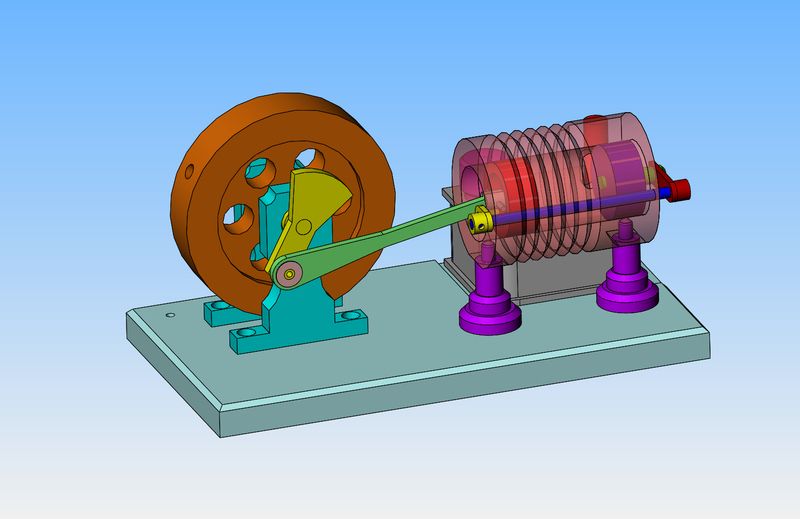