We're half-way thru February and I need to build something. The Corliss steam engine is a very interesting design, and it seems that there are two designs available on the net. One is as per the original full size Corliss engine, with two auxiliary "dashpot" cylinders to aid in closing (or maybe opening) the intake valves. The intake valve mechanisms have a complex design, incorporating a two piece rotationally slotted mechanism which works with these "dashpot" cylinders.---Then there is the simplified version, which does not have the dashpot cylinders nor the complex mechanism on the intake valve apparatus. Instead, it has two adjustable links driving the intake valving and two adjustable links driving the exhaust valve mechanism. I will be building the second simplified version. A gentleman was kind enough to send me a 3D assembly of the second type of Corliss engine and I will be revising the design to suit my own fancy. This is the engine as it was sent to me. The first obvious change I see is that all 4 of the bearings for the valve shafts are using 1/16" diameter hex head bolts. These will be upgraded to #4 socket head capscrews. I like the look of socket head capscrews better, and I seriously doubt that I could drill and tap sixteen 1/16" diameter threaded holes without breaking off the tap. Stay tuned---it should be an interesting journey.---Brian
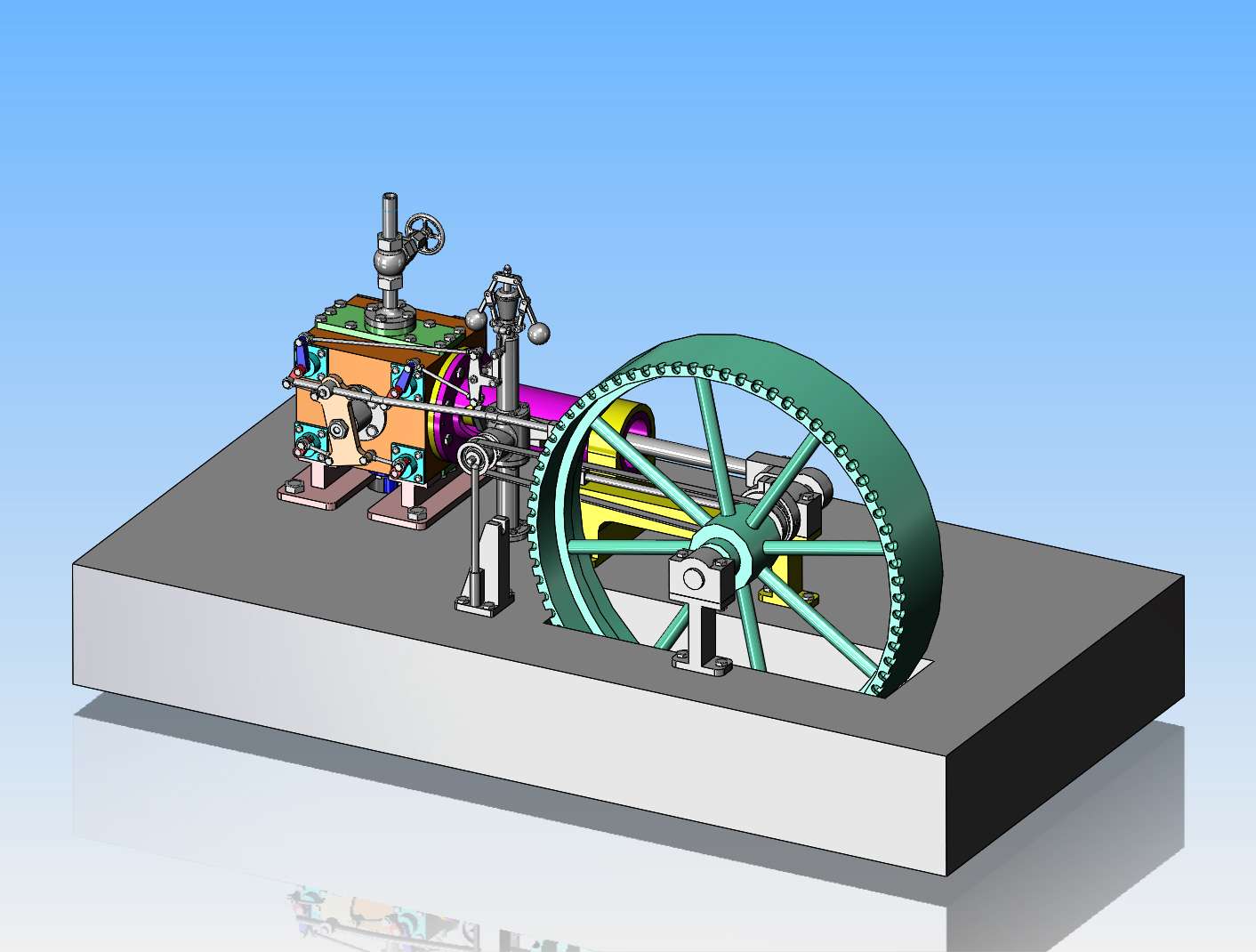
Last edited: