rodw
Well-Known Member
- Joined
- Dec 2, 2012
- Messages
- 1,146
- Reaction score
- 340
There seems to be heaps of threads on ball turners on the forum but not much said about using a boring head to do this. So here is one set up to fit on a BXA tool post.
When I bought my boring head, I bought an additional straight shank mounting flange for it. It had a 20mm diameter shaft. I bought a pair of 42mm x 20mm x 12mm bearings which only cost $5.50 each. The body is made of aluminium (from 50mm x 100mm flat bar) and the handle is 12mm steel. I found some plans online but I had to redo them as they were for a CXA tool post.
I improvised with the height adjustment over the weekend for now and used a washer sandwiched between two nuts and I was able to centre it OK. You only need to do this once and is pretty easy. It is just a matter of adjusting the height until the tool touches the top and bottom of a piece of round stock in the chuck.
So drill and tap the end of some bar stock, part off the piece so it is the same length as the diameter and go for it!
Just wind the tool in gently and take your time with small cuts.
Umm... loosen the ball before you polish it as it was very hard to get a grip to unthread it from the mandrel (just use any old bolt the right thread)
Beautiful!
To polish it, with the lathe running at 500 rpm, I started with 240 grit sandpaper and moved up to 400 wet and dry kept wet with some kerosene. Then moved up to 600, 800 and 1000 grit (with kero) before the final polish with Autosol metal polish which you should be able to get from a car accessory store. Looks like chrome!
Oh and another tip I learnt somewhere, maybe even on this forum. When tapping a thread in a lathe or mill, remove the anvil from a self punching centre punch and use it to hold the tap centred.
this really works treat and the tool can be returned to normal (but as I had 2, I cut a ring around one with the lathe) so I know which one is what.
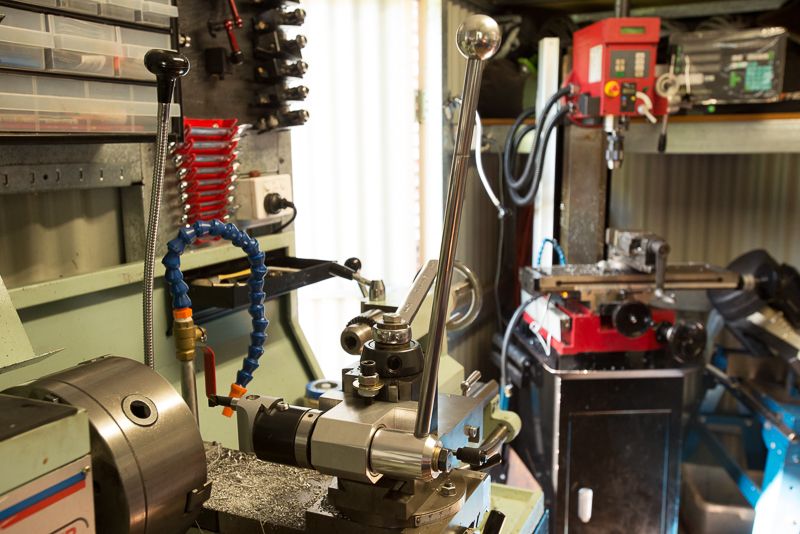
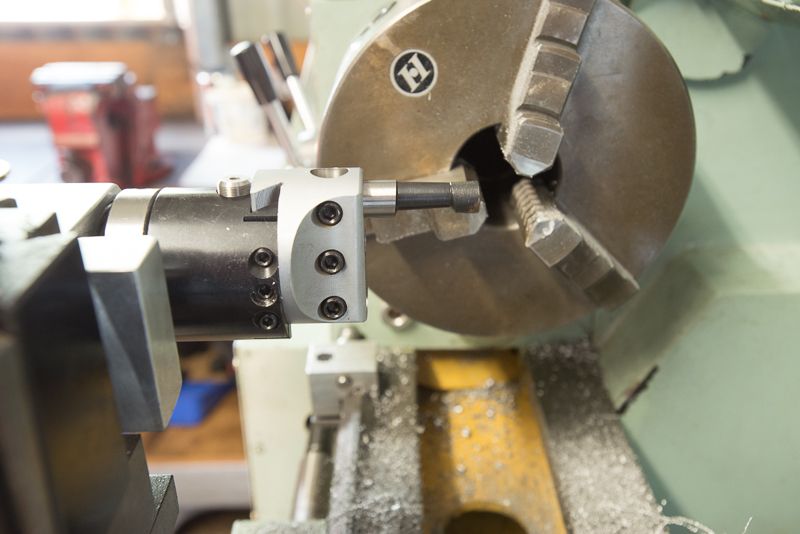
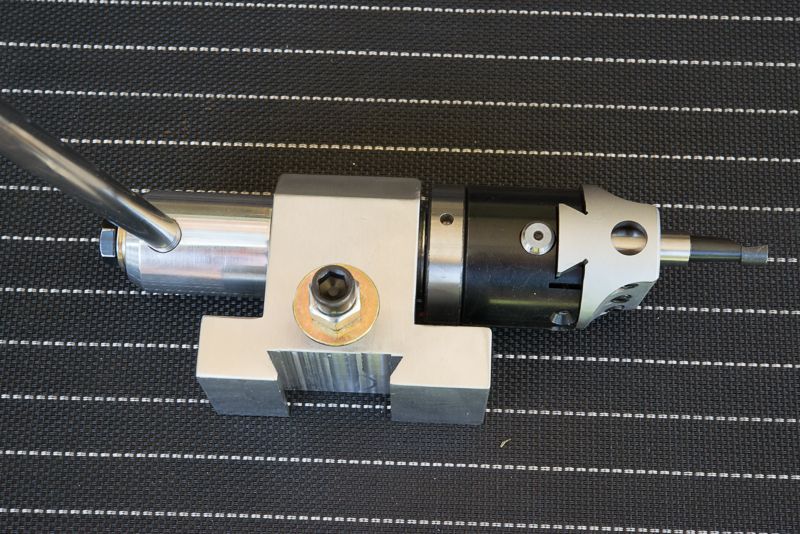
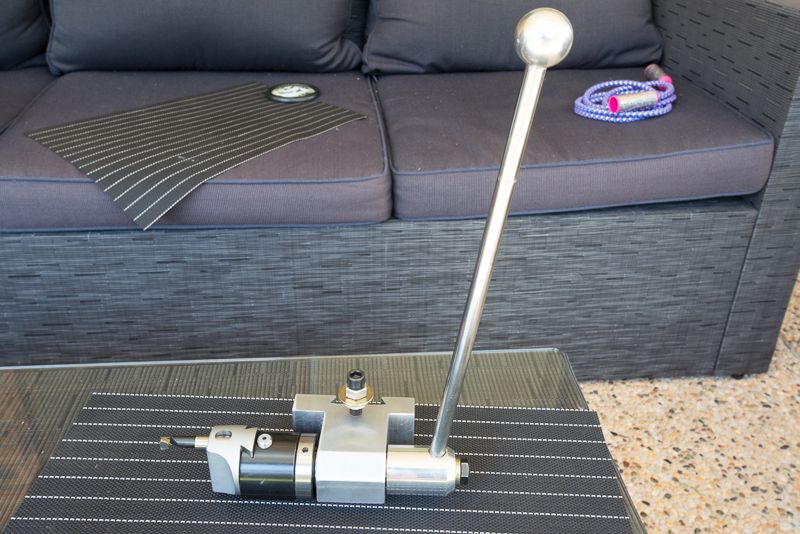
When I bought my boring head, I bought an additional straight shank mounting flange for it. It had a 20mm diameter shaft. I bought a pair of 42mm x 20mm x 12mm bearings which only cost $5.50 each. The body is made of aluminium (from 50mm x 100mm flat bar) and the handle is 12mm steel. I found some plans online but I had to redo them as they were for a CXA tool post.
I improvised with the height adjustment over the weekend for now and used a washer sandwiched between two nuts and I was able to centre it OK. You only need to do this once and is pretty easy. It is just a matter of adjusting the height until the tool touches the top and bottom of a piece of round stock in the chuck.
So drill and tap the end of some bar stock, part off the piece so it is the same length as the diameter and go for it!
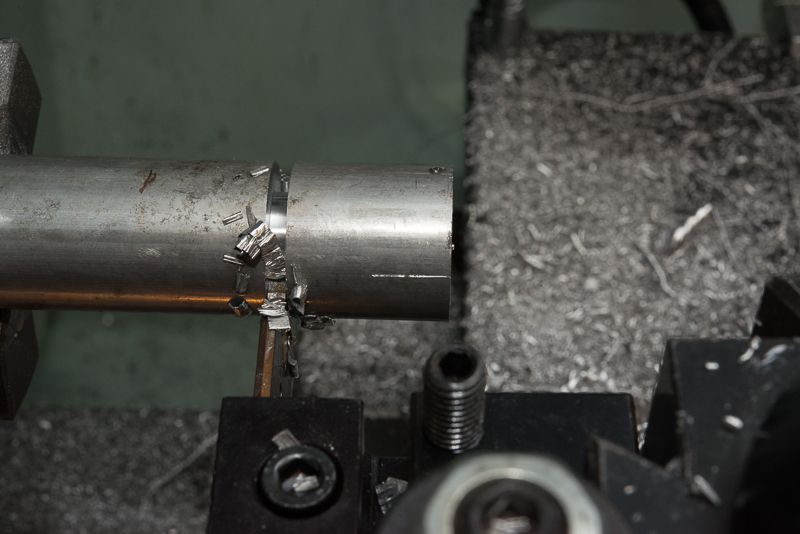
Just wind the tool in gently and take your time with small cuts.
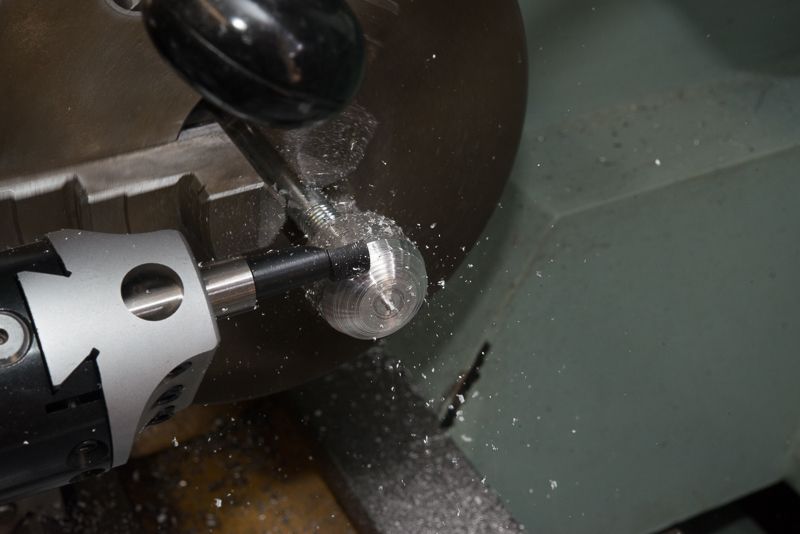
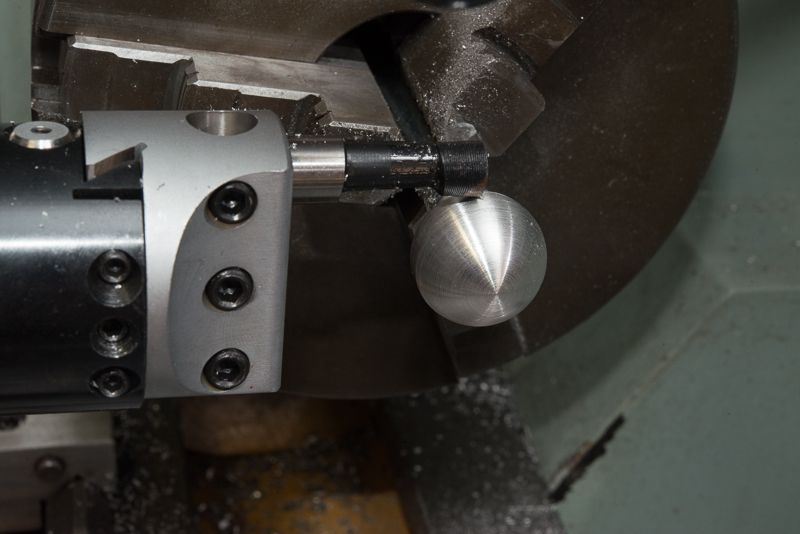
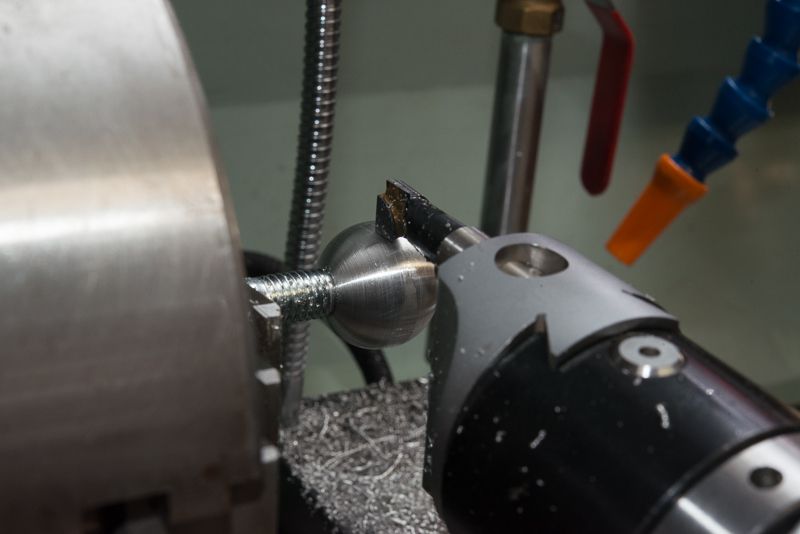
Umm... loosen the ball before you polish it as it was very hard to get a grip to unthread it from the mandrel (just use any old bolt the right thread)
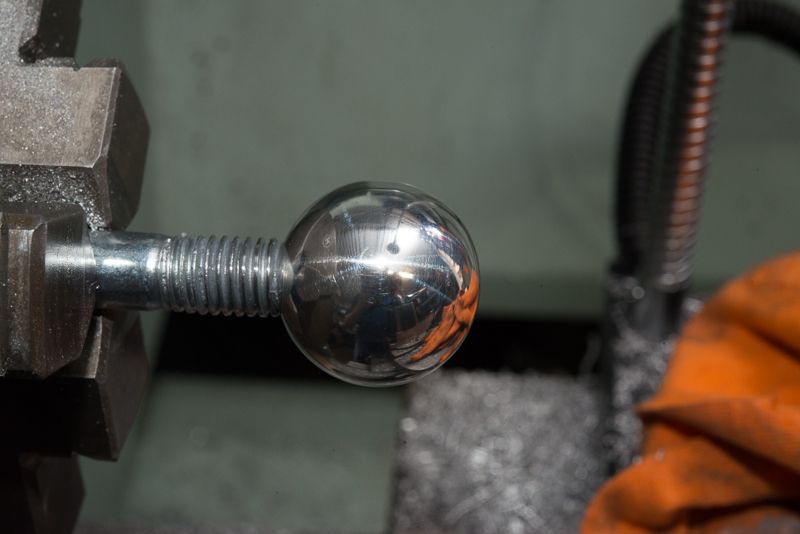
Beautiful!
To polish it, with the lathe running at 500 rpm, I started with 240 grit sandpaper and moved up to 400 wet and dry kept wet with some kerosene. Then moved up to 600, 800 and 1000 grit (with kero) before the final polish with Autosol metal polish which you should be able to get from a car accessory store. Looks like chrome!
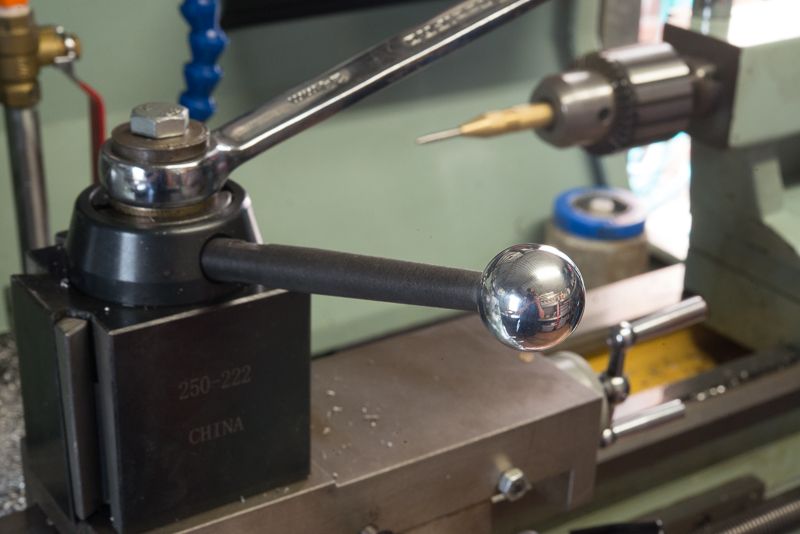
Oh and another tip I learnt somewhere, maybe even on this forum. When tapping a thread in a lathe or mill, remove the anvil from a self punching centre punch and use it to hold the tap centred.
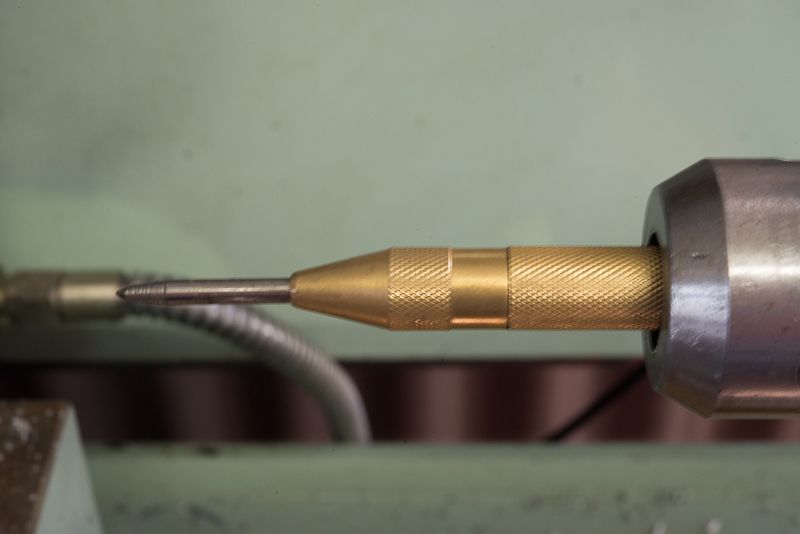
this really works treat and the tool can be returned to normal (but as I had 2, I cut a ring around one with the lathe) so I know which one is what.