- Joined
- Jan 30, 2011
- Messages
- 365
- Reaction score
- 72
Hi Guys, Thanks as always for the comments, it is good to receive this feedback and hear that it is proving beneficial.
I confess I hadn't considered the possibility of how Pete (Doubletop) first saw it (or indeed others) with reference to the JB Weld. I know some of us can be very unprepared to accept the use of modern materials - Loctite, epoxies etc - in what are after all replicas of a bygone age but I look at it from the perspective in that were those materials available in those days they probably would have been used. I wouldn't personally advocate JBW from a structural point of view (though I'm sure it would surprise us if it were) but to use it for cosmetic reasons to simulate a cast effect seems - to me - to be a fair use. After all, once that coat of paint goes on the surface beneath could be made of anything. It's a good point though Pete and I'm pleased you raised it (but even more pleased that you appear won over
)
Peter (Peatoluser) the expanding mandrel was home made and featured back when doing the rocker shaft bearings. I now have quite a collection of these from 4mm upwards. All are expanded by a 60 degree tapered caphead bolt - this one uses 8BA - and exert considerable pressure on the workpiece with very little torque on the screw. These smaller ones are used in collets which makes them in most part re-useable but the larger ones, normally held in the three jaw are turned each time to suit in order to ensure concentricity. I find this easier than using a four jaw as even then they can be difficult to get exactly right, radially and axially. They are so quick to make it's easier to reduce them slightly each time, occasionally making a new one when nothing is suitable.
This is the one used above.
This one was used on the eccentric, the screw in this case 2BA
Just to recap - the hole is tapped and deeply centred with a centre drill and the OD roughed to within .5mm or so before slots are put in. Insert the screw and just nip up before turning the OD to a good fit in the workpiece.
I have had a day of distractions today so very little progress on those last few parts :
- "Maybe tomorrow Jack" 
Regards for now - Ramon
I confess I hadn't considered the possibility of how Pete (Doubletop) first saw it (or indeed others) with reference to the JB Weld. I know some of us can be very unprepared to accept the use of modern materials - Loctite, epoxies etc - in what are after all replicas of a bygone age but I look at it from the perspective in that were those materials available in those days they probably would have been used. I wouldn't personally advocate JBW from a structural point of view (though I'm sure it would surprise us if it were) but to use it for cosmetic reasons to simulate a cast effect seems - to me - to be a fair use. After all, once that coat of paint goes on the surface beneath could be made of anything. It's a good point though Pete and I'm pleased you raised it (but even more pleased that you appear won over
Peter (Peatoluser) the expanding mandrel was home made and featured back when doing the rocker shaft bearings. I now have quite a collection of these from 4mm upwards. All are expanded by a 60 degree tapered caphead bolt - this one uses 8BA - and exert considerable pressure on the workpiece with very little torque on the screw. These smaller ones are used in collets which makes them in most part re-useable but the larger ones, normally held in the three jaw are turned each time to suit in order to ensure concentricity. I find this easier than using a four jaw as even then they can be difficult to get exactly right, radially and axially. They are so quick to make it's easier to reduce them slightly each time, occasionally making a new one when nothing is suitable.
This is the one used above.
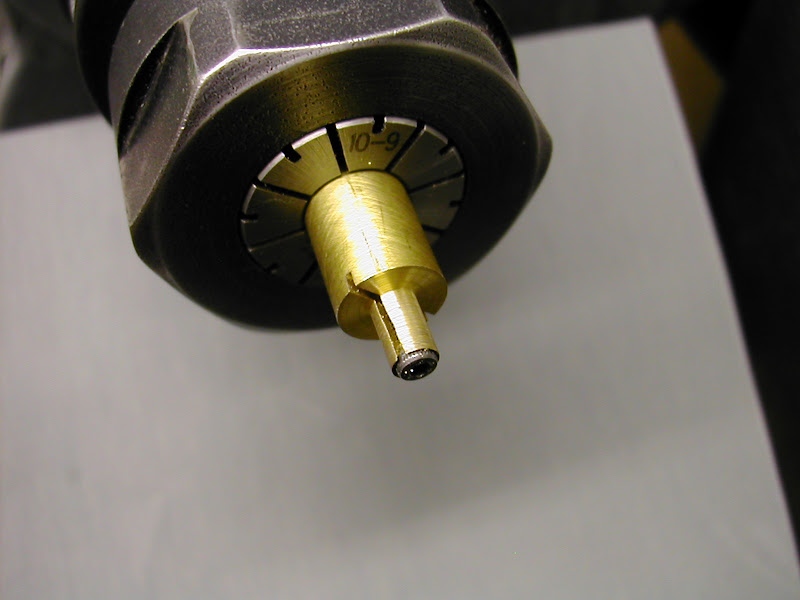
This one was used on the eccentric, the screw in this case 2BA
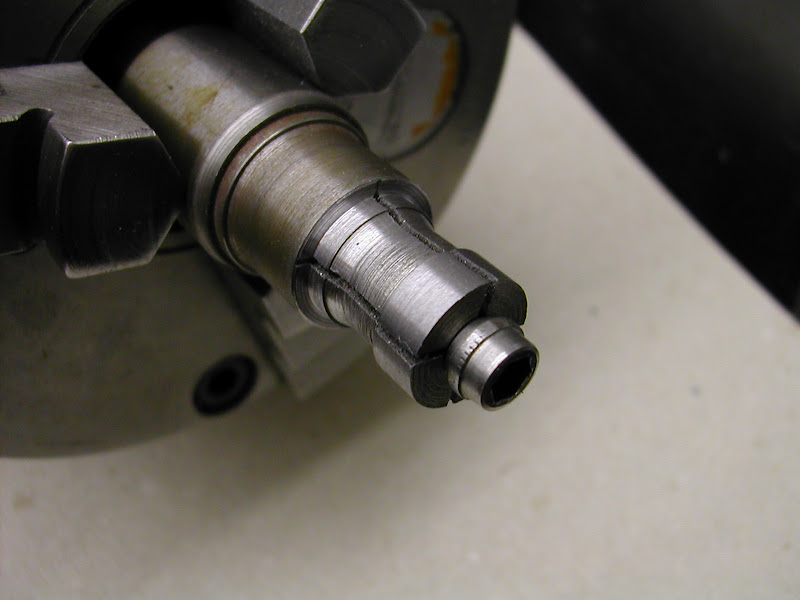
Just to recap - the hole is tapped and deeply centred with a centre drill and the OD roughed to within .5mm or so before slots are put in. Insert the screw and just nip up before turning the OD to a good fit in the workpiece.
I have had a day of distractions today so very little progress on those last few parts :
Regards for now - Ramon