- Joined
- Jan 30, 2011
- Messages
- 365
- Reaction score
- 72
Hi guy's , Once again thank you for your kind and encouraging comments. I'm not so sure I can live up to some expectations (Andy) but I do take on board what you are all saying.
Let me say though - I'm no 'expert' and certainly no academic but I do have a lot of years under the belt making various kinds of models but have no vast 'mine of information' ready to relate, just how I've gone about something. Seems like that can be of use to some so am quite happy, infact more than happy, to share it with anyone interested. I don't belong to any model engineering club (please don't read anything 'political' or sinister in that - just choice) so this and the Model Engineer site is my only form of social contact with those of similar bent outside of a few close ME friends.
On that note then Peter - pinning
Using these rods as an example but it applies just as well on flat surfaces ....
First drill a hole for the pin. Do this with two/three differing sizes the last drill taking out only a few thou. here it was .040 - .055 - .0625 for a 1/16 silver steel pin. To be as invisible as possible turn the pin from similar steel to the part as silver steel will show as a very slightly shinier area on mild steel parts after a while. The important thing is not to deburr the hole - not even slightly. If you do so it will leave a witness.
Make the pin long enough to hold and Loctite both the hole and the pin (603 or 638 high strength retainer)
Tap the pin in until it bottoms out supporting it on softer material
Clip the pin close to the workpiece and gently peen the pin to swell it in the hole. Note 'gently' - don't peen this over like a rivet as there is no need to and you may dent the work piece. (I should point out that I forgot to peen this particular one and it still worked out okay but I would always give it a few taps to ensure the pin fits the top of the hole as tightly as possible.
Next pull a layer of masking tape over the protruding pin
Then using a fine file, file the pin until the file just rubs the masking tape
Remove the tape and apply felt tip pen / marking blue
Gently file the pin keeping a wary eye out for marking the ink as here
Then file to flair in with the surrounding surface
Finally finish with some worn emery. The duller surface on the rest of the rod is the result of using wet and dry and Garryflex abrasive blocks which produes a very smooth finish
This method works just as well on flat surfaces though the final filing has to be done very carefully to avoid scratching the surrounding area - I prefer to use a flat needle file for that with the very tip rounded off with a stone to prevent corner 'dig ins'. By pushing the end of the file flat down on top of the pin with the thumb of one hand while bending the file up slightly - a needle file will flex sufficiently - and apply filing motion with the other in very short strokes it is surprising just how much control you have in taking the pin down to the surface.
As said - can't stress it enough - if you debur the hole - no matter how carefully - you will get a witness. A little black circle or part of a circle that will constantly yell at you that you really shouldn't have deburred the hole
If it's a threaded hole that needs to be reclaimed or disguised it will not work if the thread comes to the top of the hole. No matter how much you peen it there will always be the start of the helix. The only way to totally disguse it is to open it up and plug it as above.
If its done right the only evidence should be a slight discolouration if the materials are different.
Hope that will help improve your pinning Peter
The compressor was plumbed in without half the hassle envisaged so I was able to make a good start on the valve parts - more later
Hope this is useful to others too
Regards - Ramon
Let me say though - I'm no 'expert' and certainly no academic but I do have a lot of years under the belt making various kinds of models but have no vast 'mine of information' ready to relate, just how I've gone about something. Seems like that can be of use to some so am quite happy, infact more than happy, to share it with anyone interested. I don't belong to any model engineering club (please don't read anything 'political' or sinister in that - just choice) so this and the Model Engineer site is my only form of social contact with those of similar bent outside of a few close ME friends.
On that note then Peter - pinning
Using these rods as an example but it applies just as well on flat surfaces ....
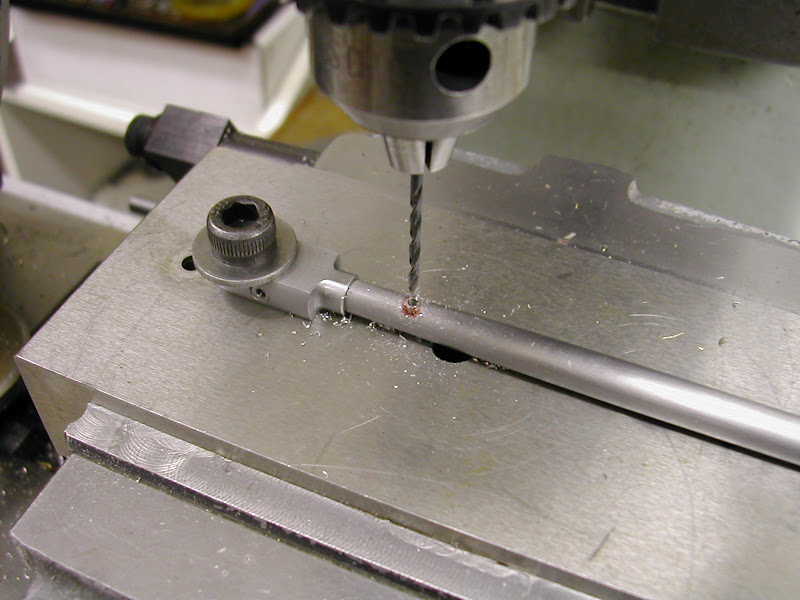
First drill a hole for the pin. Do this with two/three differing sizes the last drill taking out only a few thou. here it was .040 - .055 - .0625 for a 1/16 silver steel pin. To be as invisible as possible turn the pin from similar steel to the part as silver steel will show as a very slightly shinier area on mild steel parts after a while. The important thing is not to deburr the hole - not even slightly. If you do so it will leave a witness.
Make the pin long enough to hold and Loctite both the hole and the pin (603 or 638 high strength retainer)
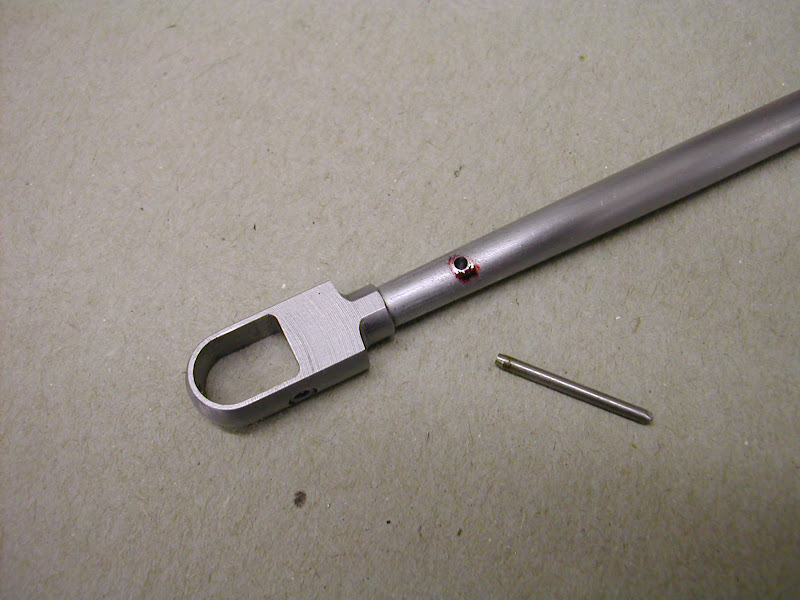
Tap the pin in until it bottoms out supporting it on softer material
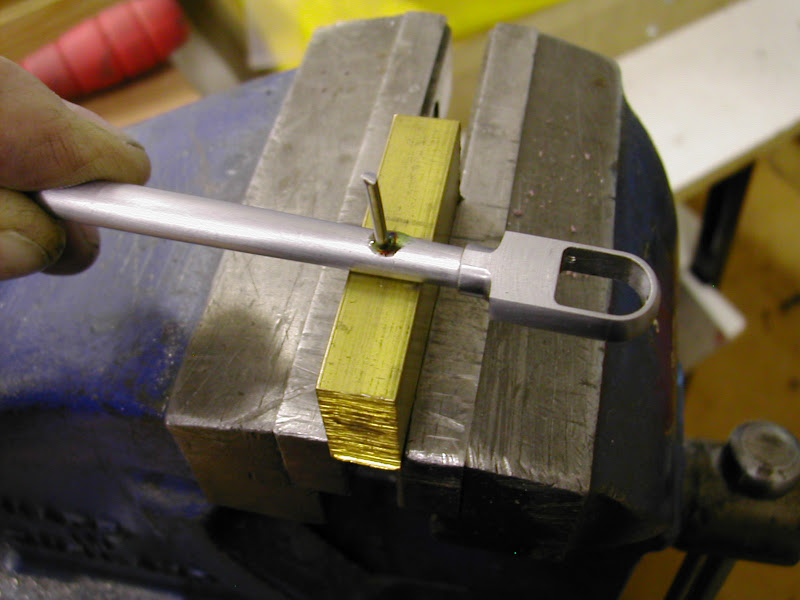
Clip the pin close to the workpiece and gently peen the pin to swell it in the hole. Note 'gently' - don't peen this over like a rivet as there is no need to and you may dent the work piece. (I should point out that I forgot to peen this particular one and it still worked out okay but I would always give it a few taps to ensure the pin fits the top of the hole as tightly as possible.
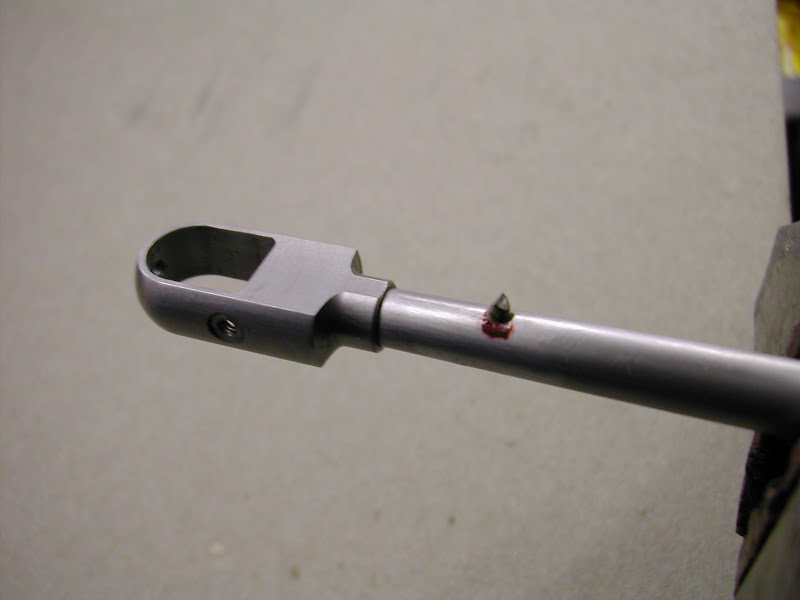
Next pull a layer of masking tape over the protruding pin
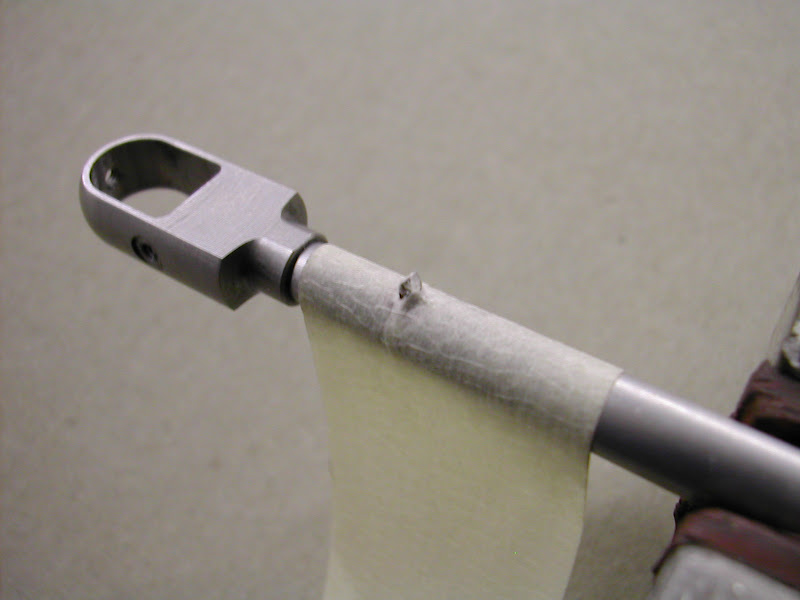
Then using a fine file, file the pin until the file just rubs the masking tape
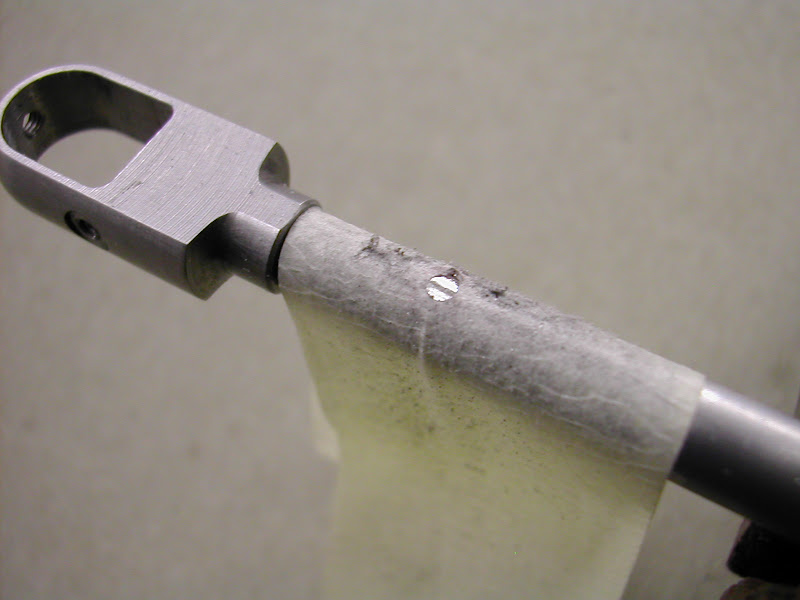
Remove the tape and apply felt tip pen / marking blue
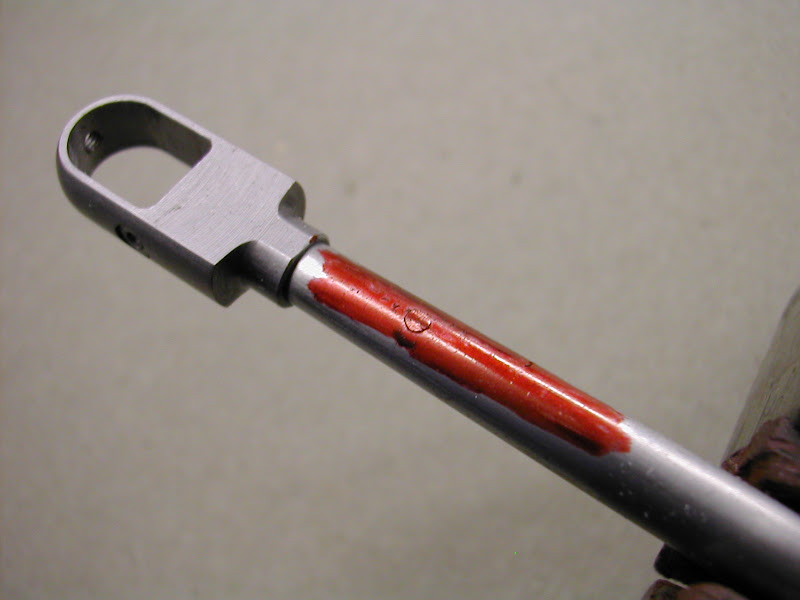
Gently file the pin keeping a wary eye out for marking the ink as here
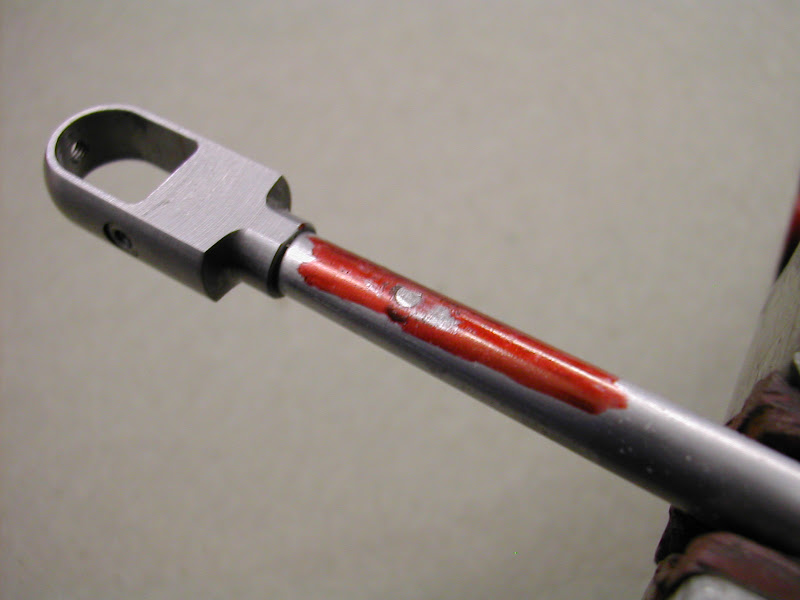
Then file to flair in with the surrounding surface
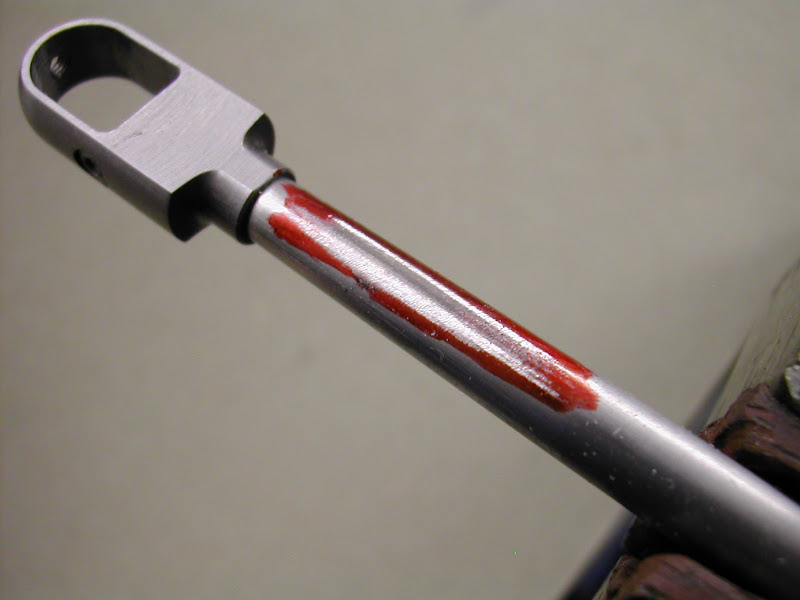
Finally finish with some worn emery. The duller surface on the rest of the rod is the result of using wet and dry and Garryflex abrasive blocks which produes a very smooth finish
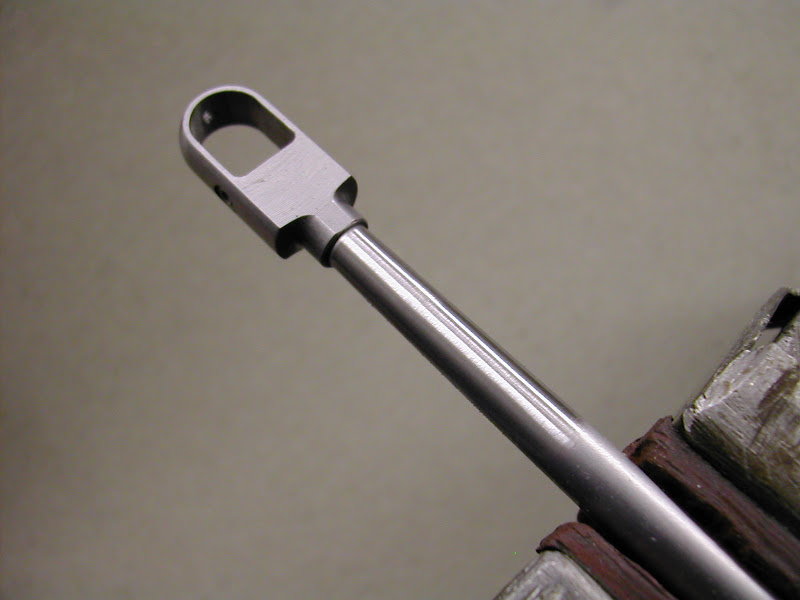
This method works just as well on flat surfaces though the final filing has to be done very carefully to avoid scratching the surrounding area - I prefer to use a flat needle file for that with the very tip rounded off with a stone to prevent corner 'dig ins'. By pushing the end of the file flat down on top of the pin with the thumb of one hand while bending the file up slightly - a needle file will flex sufficiently - and apply filing motion with the other in very short strokes it is surprising just how much control you have in taking the pin down to the surface.
As said - can't stress it enough - if you debur the hole - no matter how carefully - you will get a witness. A little black circle or part of a circle that will constantly yell at you that you really shouldn't have deburred the hole
If it's a threaded hole that needs to be reclaimed or disguised it will not work if the thread comes to the top of the hole. No matter how much you peen it there will always be the start of the helix. The only way to totally disguse it is to open it up and plug it as above.
If its done right the only evidence should be a slight discolouration if the materials are different.
Hope that will help improve your pinning Peter
The compressor was plumbed in without half the hassle envisaged so I was able to make a good start on the valve parts - more later
Hope this is useful to others too
Regards - Ramon