Pete,
What Andrew said actually makes sense.
You might find that lots of ballast might be required to get the hull to its waterline (can't say designed waterline because you worked it out yourself), but even so, getting a good waterline is one of the first things you need to do, without it you could end up with a very unstable boat.
I made a 4ft long Clyde puffer, and even with a 100 amp hour battery in it, it was still too top heavy. I eventually put in internally sealed ballast tanks that allowed the boat to sink further, they contained another 5gallons of water weighing 50 pounds.
The chalk marks on the outside of the hull shows the rough position where the tanks were inside.
You might have to resort to having a couple of large pop bottles full of water inside to achieve your waterline.
John
What Andrew said actually makes sense.
You might find that lots of ballast might be required to get the hull to its waterline (can't say designed waterline because you worked it out yourself), but even so, getting a good waterline is one of the first things you need to do, without it you could end up with a very unstable boat.
I made a 4ft long Clyde puffer, and even with a 100 amp hour battery in it, it was still too top heavy. I eventually put in internally sealed ballast tanks that allowed the boat to sink further, they contained another 5gallons of water weighing 50 pounds.
The chalk marks on the outside of the hull shows the rough position where the tanks were inside.
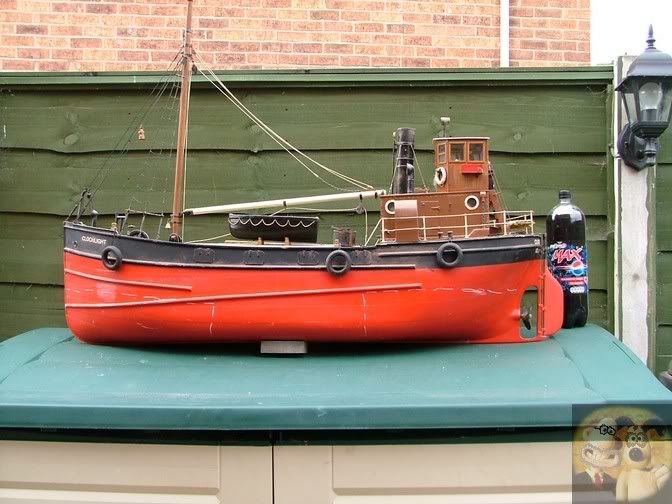
You might have to resort to having a couple of large pop bottles full of water inside to achieve your waterline.
John