rake60
Well-Known Member
- Joined
- Jul 8, 2007
- Messages
- 4,756
- Reaction score
- 126
I was handed a 3/4" stub shaft at work today.
It needed a 3/16" X 1" long keyway cut in it.
I've cut a lot of keyways but never really gave them much thought.
For this one I actually looked up the standard SPECS.
It's on center, the width is good and the .644" length ended up .640", within tolerance.
It even looked good.
The key fits too. That's a plus!
Rick
It needed a 3/16" X 1" long keyway cut in it.
I've cut a lot of keyways but never really gave them much thought.
For this one I actually looked up the standard SPECS.
It's on center, the width is good and the .644" length ended up .640", within tolerance.
It even looked good.
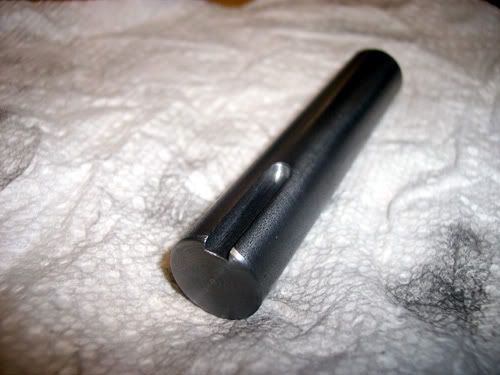
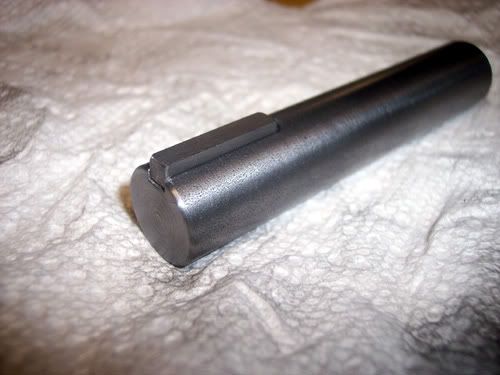
The key fits too. That's a plus!
Rick