- Joined
- Jul 16, 2007
- Messages
- 3,035
- Reaction score
- 1,123
Here's a shot of both of the heads with the chamber machining finished.
Now it was time to start the hand work, filing, stoning and polishing. The first picture shows the starting procedure, I cover everything with marker ink so I can see where the high spots are when I'm removing stock.
The next picture shows the start of the metal removal. I put a layer of duct tape over everything so that when I bump the head face with the grinder collet I won't put any deep gouges in it, at least not deep enough that I can't take a light cut to clean it up.
You can see the high spots showing as I file across them.
Next is a picture showing all the filing finished and the stone work to remove the small bumps in the corners where I can't file.
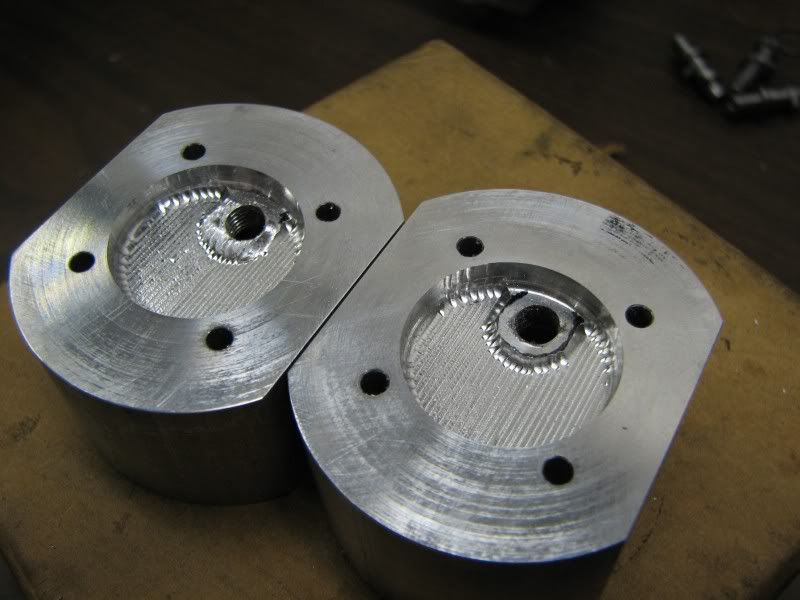
Now it was time to start the hand work, filing, stoning and polishing. The first picture shows the starting procedure, I cover everything with marker ink so I can see where the high spots are when I'm removing stock.
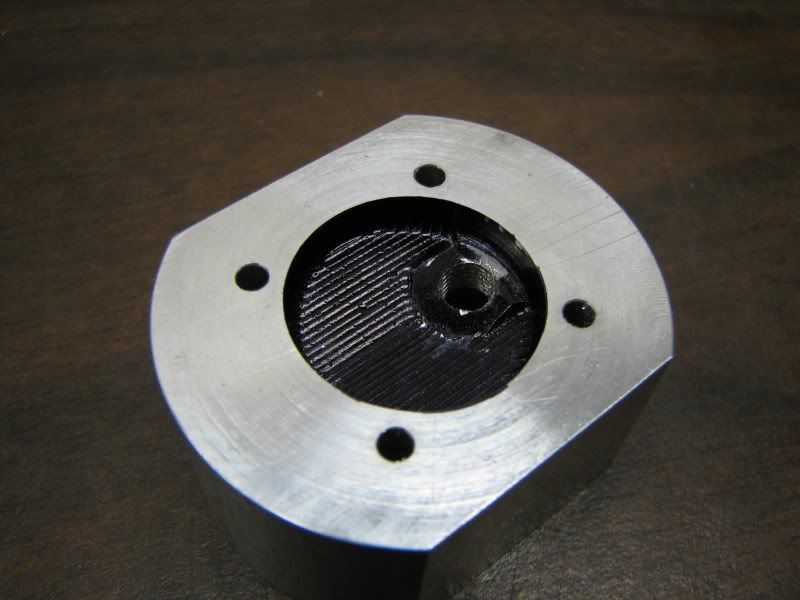
The next picture shows the start of the metal removal. I put a layer of duct tape over everything so that when I bump the head face with the grinder collet I won't put any deep gouges in it, at least not deep enough that I can't take a light cut to clean it up.
You can see the high spots showing as I file across them.
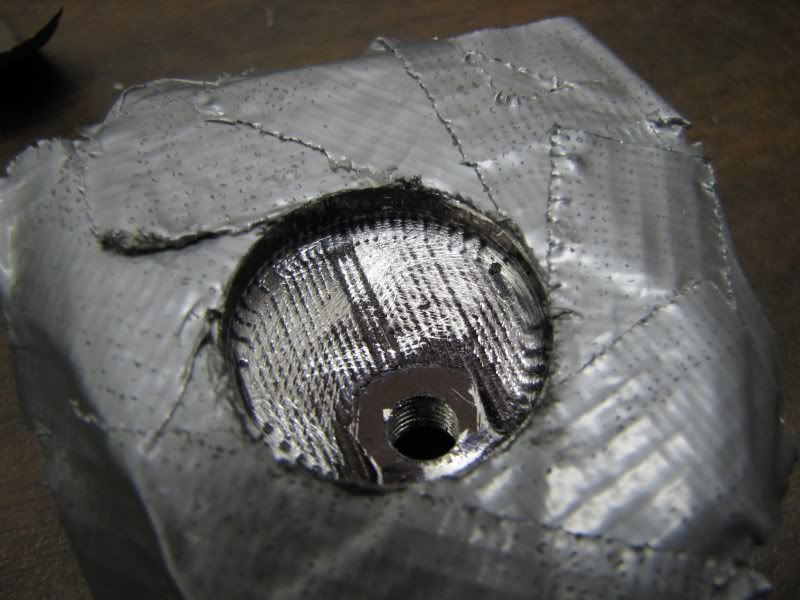
Next is a picture showing all the filing finished and the stone work to remove the small bumps in the corners where I can't file.
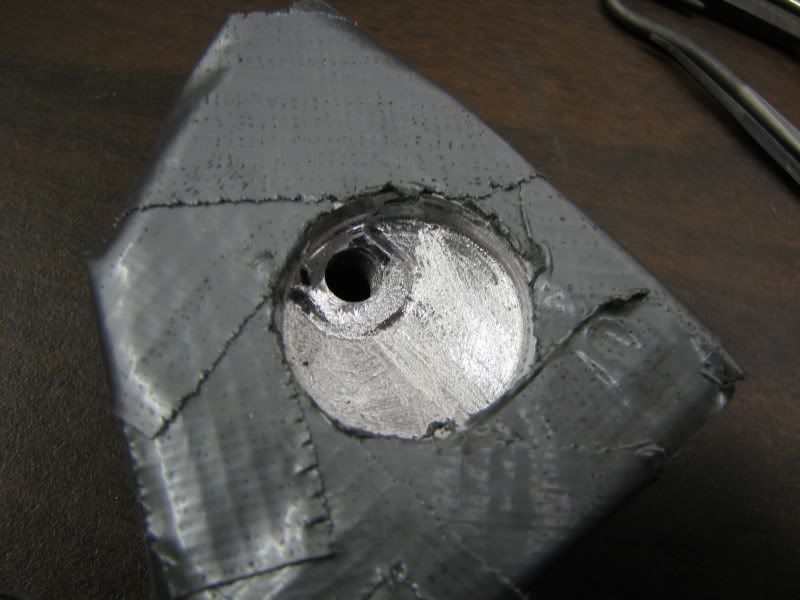