Generatorgus
Senior Member
- Joined
- Feb 25, 2010
- Messages
- 362
- Reaction score
- 167
Well, I thought I had the valve body seal decision made, but thanks to Mike Ive got a better way.
I never thought to check metric O-ring sizes.
I try to avoid the metric thing, although I wish they had gone thru with it way back in the 70s? when it was a big debate in this country.
Its a much easier system but we steadfastly refused to accept it and chose to maintain our archaic system of measurement.
There is no reason that I should need two sets of wrenches to work on my vehicle or have to have a decimal equivalent chart hanging in my shop.
A lot more important things in this country should be maintained, but our measuring system should have been allowed to fade into history.
Sorry, I had to get that off my chest.
I did find a 1mm size that will work for the bottom seal without any changes and I can dump the Teflon thing.
Having settled on how to seal the valve bodies it is/was time to build them.
Still sticking with a separate flange I decided to make it a clamping type with a step in the flange to engage a ring left on the OD of the body.
With a ½ SS bar in the lathe starting on the bottom end (or top, depending on which valve body your looking at) I cut the 7/16 OD and the 3/8 in OD step for the inner seal at the end.
At that point I decided to test the fit in the head and while at it I traced the location of the port.
A 1/8 dia hole was drilled and reamed thru for the valve stem and then the bottom hollowed out to the top of the port location. The body was parted off and in the mill the port holes where bored with an end mill.
Sorry, no pics, my camera battery needed charging.
Now semi complete another test fit.
Then back in the lathe the top ends were hollowed out with a drill and finished flat at the bottom to accommodate the valve springs.
Also the taper was cut by trial and error. I measured a 3 degree angle on my sketch, but I snuck up on it anyway. Just being careful, not wanting to ruin them at this point.
This time I just plain forgot to take pictures of those steps.
First part almost complete, just noticed I didn't cut the grooves for the top O-ring.
I never thought to check metric O-ring sizes.
I try to avoid the metric thing, although I wish they had gone thru with it way back in the 70s? when it was a big debate in this country.
Its a much easier system but we steadfastly refused to accept it and chose to maintain our archaic system of measurement.
There is no reason that I should need two sets of wrenches to work on my vehicle or have to have a decimal equivalent chart hanging in my shop.
A lot more important things in this country should be maintained, but our measuring system should have been allowed to fade into history.
Sorry, I had to get that off my chest.
I did find a 1mm size that will work for the bottom seal without any changes and I can dump the Teflon thing.
Having settled on how to seal the valve bodies it is/was time to build them.
Still sticking with a separate flange I decided to make it a clamping type with a step in the flange to engage a ring left on the OD of the body.
With a ½ SS bar in the lathe starting on the bottom end (or top, depending on which valve body your looking at) I cut the 7/16 OD and the 3/8 in OD step for the inner seal at the end.
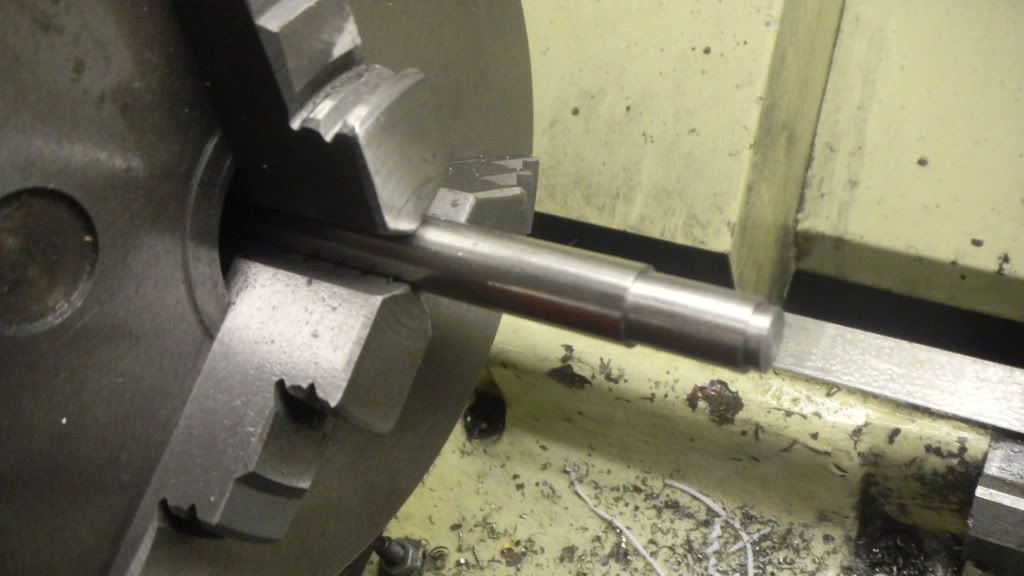
At that point I decided to test the fit in the head and while at it I traced the location of the port.
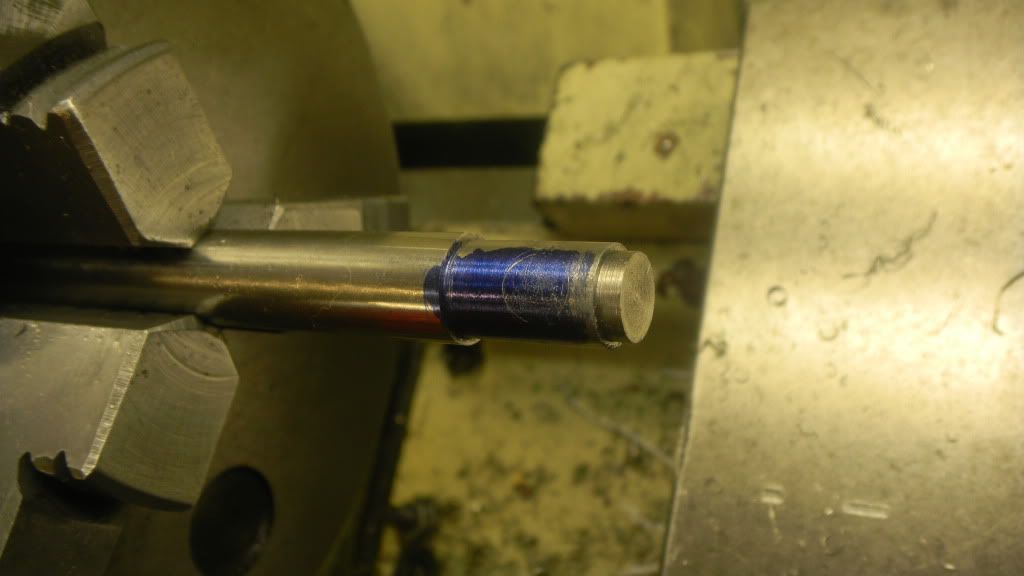
A 1/8 dia hole was drilled and reamed thru for the valve stem and then the bottom hollowed out to the top of the port location. The body was parted off and in the mill the port holes where bored with an end mill.
Sorry, no pics, my camera battery needed charging.
Now semi complete another test fit.
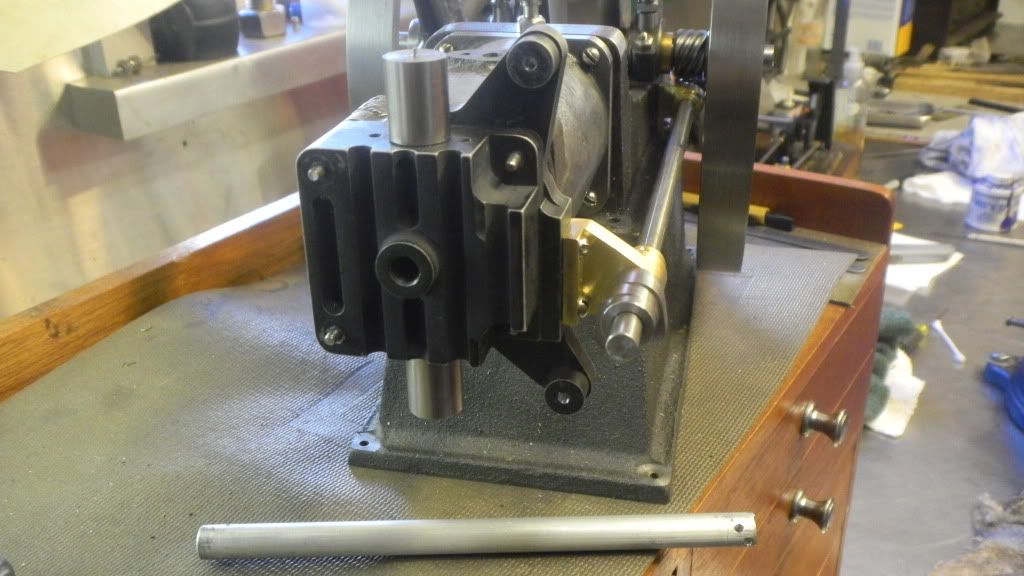
Then back in the lathe the top ends were hollowed out with a drill and finished flat at the bottom to accommodate the valve springs.
Also the taper was cut by trial and error. I measured a 3 degree angle on my sketch, but I snuck up on it anyway. Just being careful, not wanting to ruin them at this point.
This time I just plain forgot to take pictures of those steps.
First part almost complete, just noticed I didn't cut the grooves for the top O-ring.
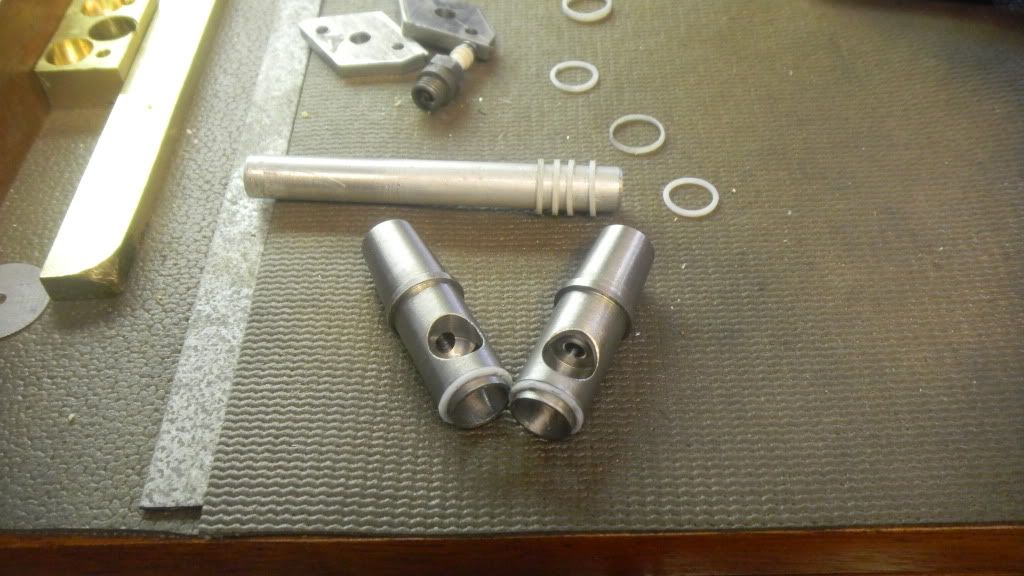
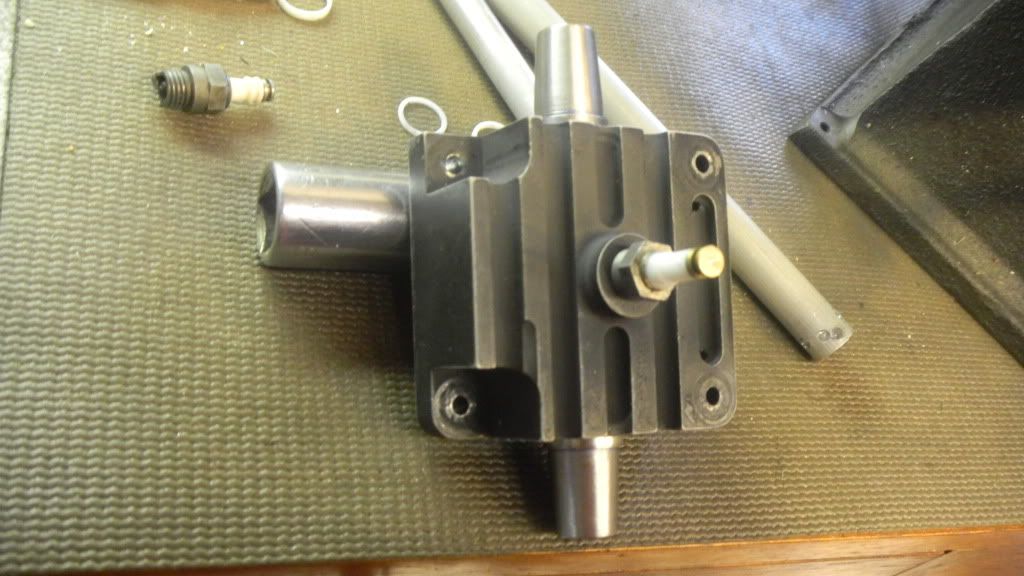