- Joined
- Jun 4, 2008
- Messages
- 3,294
- Reaction score
- 636
Machined the large wheel using a piece of aluminum as the fixture plate. For support I used a set of 12" vise jaws I got from Monster Jaws, in which I milled steps.
Then made the magnet pockets in brass strips that form the rim. I had to make these in 3 separate pieces in order to fit 4" wide brass sheet. The flat head 2-56 socket screws are stainless and thus non-magnetic. Since the wheel is now effectively 1/4" thick I made the brass hub thicker by 1/8".
Then some test fits. I discovered that I'd messed up the small wheel that is connected to the large wheel's shaft by countersinking the wrong side, and also not milling a relief groove to clear the bearing. So that wheel will need to be remade. I also did remake the bearing carrier as I noticed it was drilled off-center.
The shaft lengths seem to be critical in getting the wheels to be close but not touching. The two intermediate shafts are easy to adjust, but the shafts that go through the bearing carriers are harder. I won't really know until I get everything assembled.
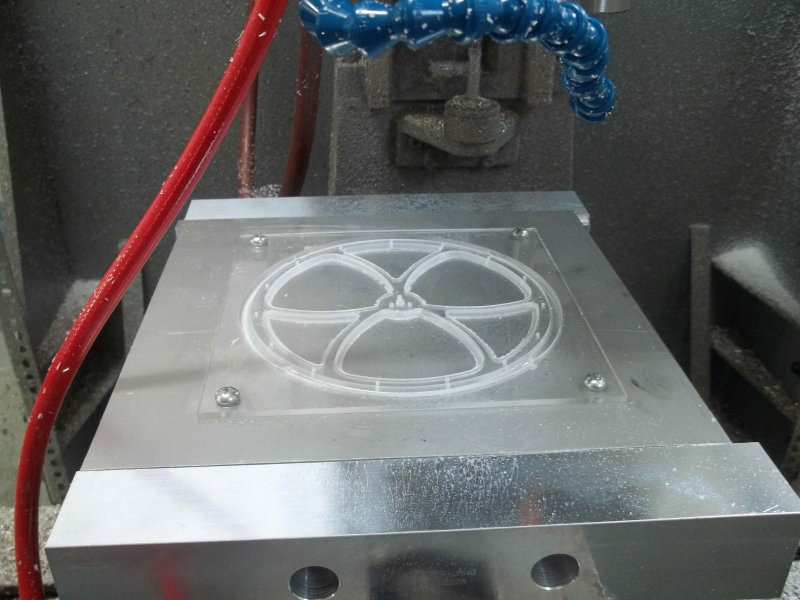
Then made the magnet pockets in brass strips that form the rim. I had to make these in 3 separate pieces in order to fit 4" wide brass sheet. The flat head 2-56 socket screws are stainless and thus non-magnetic. Since the wheel is now effectively 1/4" thick I made the brass hub thicker by 1/8".
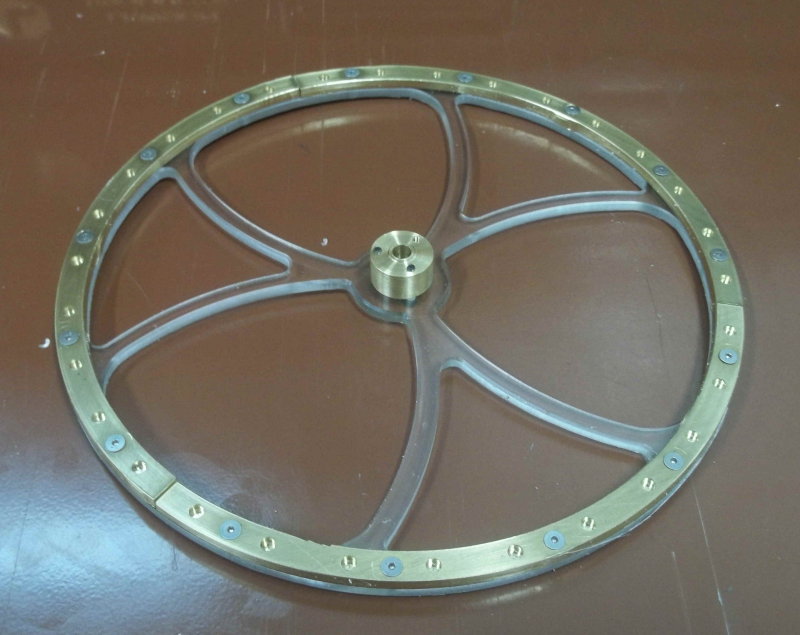
Then some test fits. I discovered that I'd messed up the small wheel that is connected to the large wheel's shaft by countersinking the wrong side, and also not milling a relief groove to clear the bearing. So that wheel will need to be remade. I also did remake the bearing carrier as I noticed it was drilled off-center.
The shaft lengths seem to be critical in getting the wheels to be close but not touching. The two intermediate shafts are easy to adjust, but the shafts that go through the bearing carriers are harder. I won't really know until I get everything assembled.
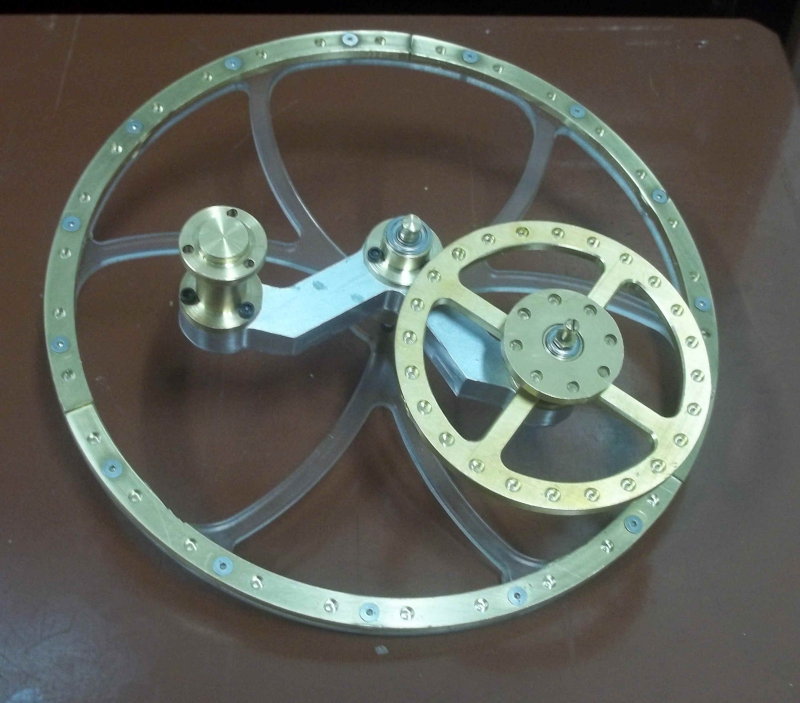