It seems that in spite of all the care I took when machining and assembling my Atkinson engine, I have a leaky intake valve. Perhaps not leaking badly enough to prevent the engine from starting, but leaking, none the less. As I go through all the possible causes for the engine not starting and try to eliminate them, one thing popped up. Its a miserable chore to pull the head off the Atkinson once its all assembled, so I needed a way to test for leaking valves BEFORE assembling the head to the engine. So---I made a pressure chamber. This is simply a round peice of aluminum the same diameter as the cylinder, with the same bolt pattern as the cylinder, and an internal cavity which I can pump air into from my compressor. It is turned down to a diameter that fits into the recess in the cylinder head, and the internal chamber is big enough in diameter to miss the heads of the valves. I put a ring of gasket material between the test chamber and the cyl head, then carefully snugged down the 4 cylinder head bolts. Now I can pressurize the chamber with my compressor, and it immediately shows up a leaky valve. You can hear it hissing at the carb throat or the exhaust manifold. I am probably going to have to make a new intake valve cage ---maybe even a new valve. Ah well, bad on me. I thought that the pressure chamber idea might help some other poor sod who is attempting to build a 4 cycle engine.---Brian
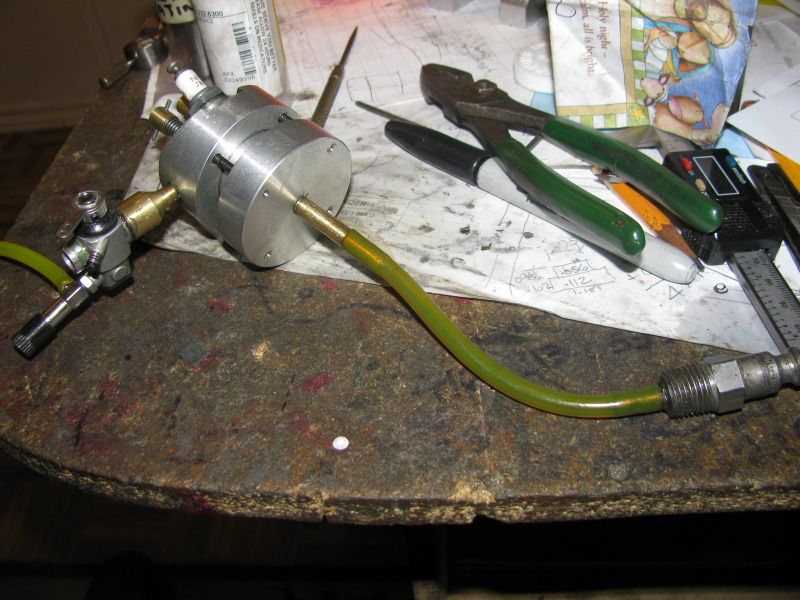
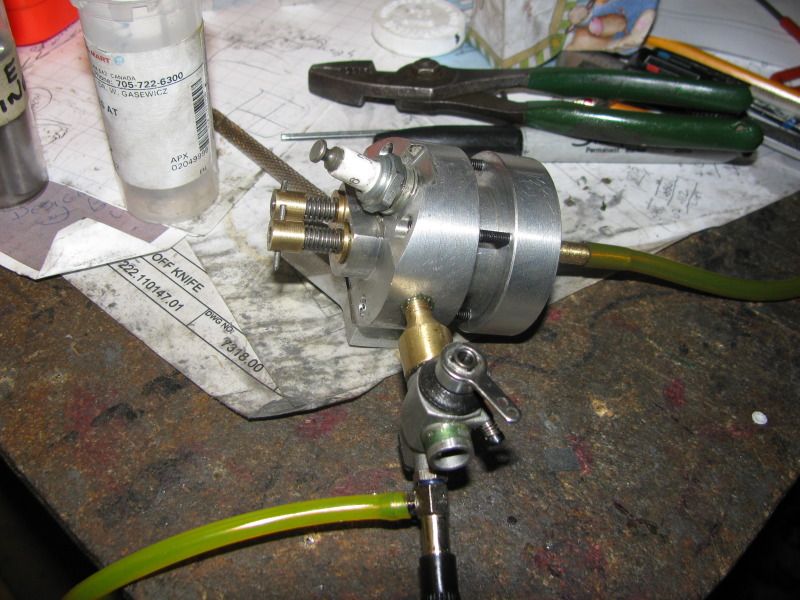