I am considering buying a toolpost grinder for my lathe from Little Machine Shop.
http://littlemachineshop.com/products/product_view.php?ProductID=2001&category=
I simply don't have the ability to turn small precision parts like needle valves for miniature carburetors on my 10" x 18" lathe. Once I get below about 3/32" diameter stock, the material just flexes away from even my sharpest HSS tooling. I am assuming that with a toolpost grinder like the one shown in the picture and link, that I could grind these small items to the required taper. I would be using this for unhardened mild cold rolled steel. I would also use it to grind the sealing faces on miniature valves like the ones on the small i.c. engines I build. I don't know the first thing about toolpost grinders, but for $150 I am willing to learn, especially if I can use one to make these small parts that I have no other good way of making. The one in the picture is 2" from the center of the grinding wheel to the base, and they suggest removing the compound rest and bolting it directly to the cross slide table. My lathe measures about 3" from the center of the chuck to the top of the cross slide table, so I realize I would have to machine an adapter plate. Of course, this would leave me with no way to set up angles to grind tapers, so I would probably have to have an adapter plate with drilled and tapped holes at whatever angles I would most commonly wish to grind on tapered needle valves. Any insight that you can give me in respect to what i want to do would be much appreciated.-----Brian
http://littlemachineshop.com/products/product_view.php?ProductID=2001&category=
I simply don't have the ability to turn small precision parts like needle valves for miniature carburetors on my 10" x 18" lathe. Once I get below about 3/32" diameter stock, the material just flexes away from even my sharpest HSS tooling. I am assuming that with a toolpost grinder like the one shown in the picture and link, that I could grind these small items to the required taper. I would be using this for unhardened mild cold rolled steel. I would also use it to grind the sealing faces on miniature valves like the ones on the small i.c. engines I build. I don't know the first thing about toolpost grinders, but for $150 I am willing to learn, especially if I can use one to make these small parts that I have no other good way of making. The one in the picture is 2" from the center of the grinding wheel to the base, and they suggest removing the compound rest and bolting it directly to the cross slide table. My lathe measures about 3" from the center of the chuck to the top of the cross slide table, so I realize I would have to machine an adapter plate. Of course, this would leave me with no way to set up angles to grind tapers, so I would probably have to have an adapter plate with drilled and tapped holes at whatever angles I would most commonly wish to grind on tapered needle valves. Any insight that you can give me in respect to what i want to do would be much appreciated.-----Brian
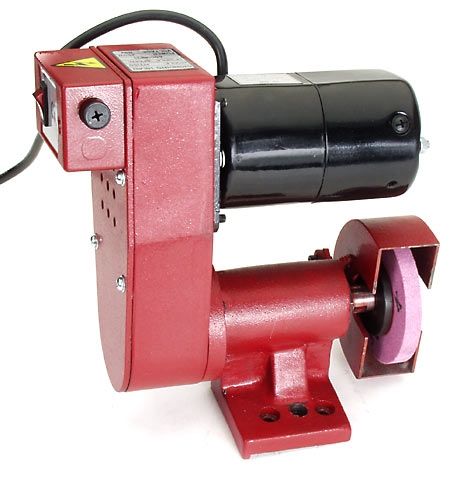