- Joined
- Mar 3, 2008
- Messages
- 243
- Reaction score
- 20
I found some interesting plans and software from Jon Bondy here: http://www.jonbondy.com/software.htm
These are plans and software to measure a small engines RPM and Power. It is a simple system that can calculate the power by measuring the time it takes to recover from a near stall using the MOI ( Moment of Inertia ) of the flywheel. For simple solid flywheels it has a built in calculator. For wheels with spokes and cutouts you need to figure this MOI out yourself. I will model the flywheel in Pro/Engineer and that will give me an accurate MOI.
First was to make the PCB. Since I had a Printed Circuit Board Prototype machine at work this was easy. This machine is essentially a 2.5D CNC machine. I can put in sheets of copper clad material, and it will mill out insulating areas around the conductors.
Here is the $27,000 CNC Machine
And after 10 Min...... A finished PCB. You can see how the cutter insulated the conductors.
Here is the bottom side. The pads with spokes are Negative (GND) connections
After assembly:
For testing I hooked up my PM-2a Steam Engine:
Screen shot showing output of one of the tests:
Overall it was a fun project, but I am not sure how accurate it is. I will do some more tests on some of my other engines. I think there is a newer program out there that uses a computer mouse's scroll wheel for input.
Well its starting to get warm finally and I think this will be my last Milling/Lathing project until the fall. As soon as it gets hot, I am outside most of the time. Summer is too short in Canada!
But I will still be working on/Cruising in this:
Iron Horse
These are plans and software to measure a small engines RPM and Power. It is a simple system that can calculate the power by measuring the time it takes to recover from a near stall using the MOI ( Moment of Inertia ) of the flywheel. For simple solid flywheels it has a built in calculator. For wheels with spokes and cutouts you need to figure this MOI out yourself. I will model the flywheel in Pro/Engineer and that will give me an accurate MOI.
First was to make the PCB. Since I had a Printed Circuit Board Prototype machine at work this was easy. This machine is essentially a 2.5D CNC machine. I can put in sheets of copper clad material, and it will mill out insulating areas around the conductors.
Here is the $27,000 CNC Machine
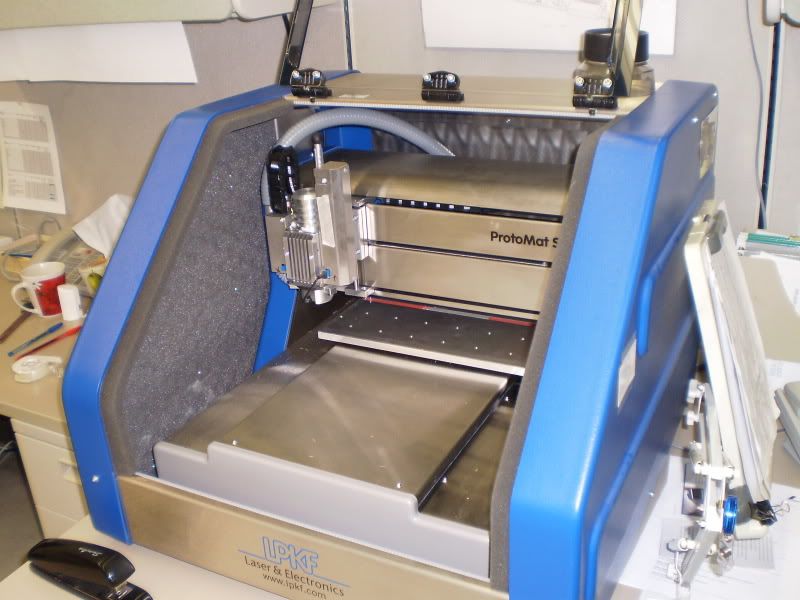
And after 10 Min...... A finished PCB. You can see how the cutter insulated the conductors.
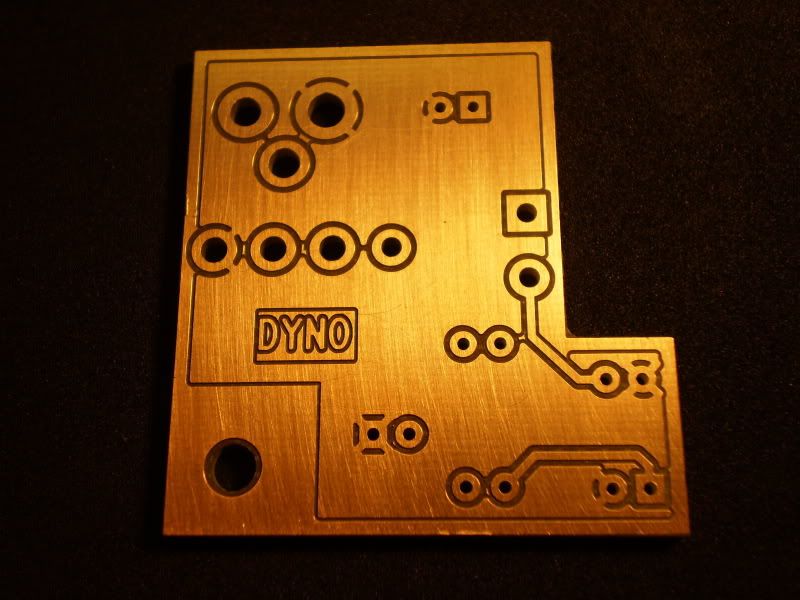
Here is the bottom side. The pads with spokes are Negative (GND) connections
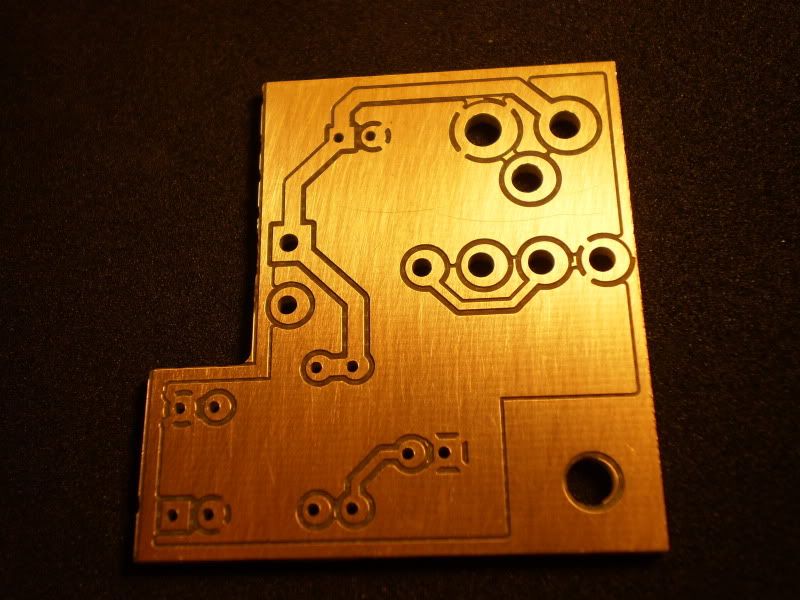
After assembly:
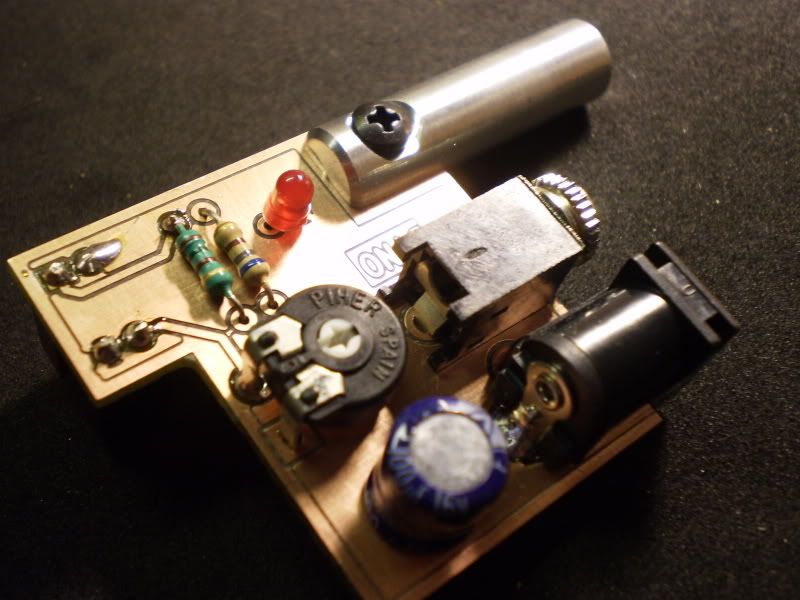
For testing I hooked up my PM-2a Steam Engine:
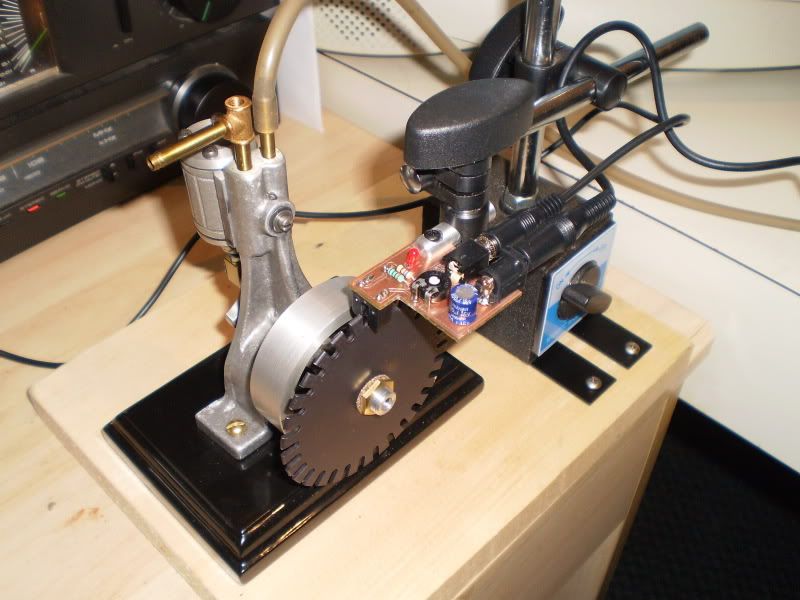
Screen shot showing output of one of the tests:
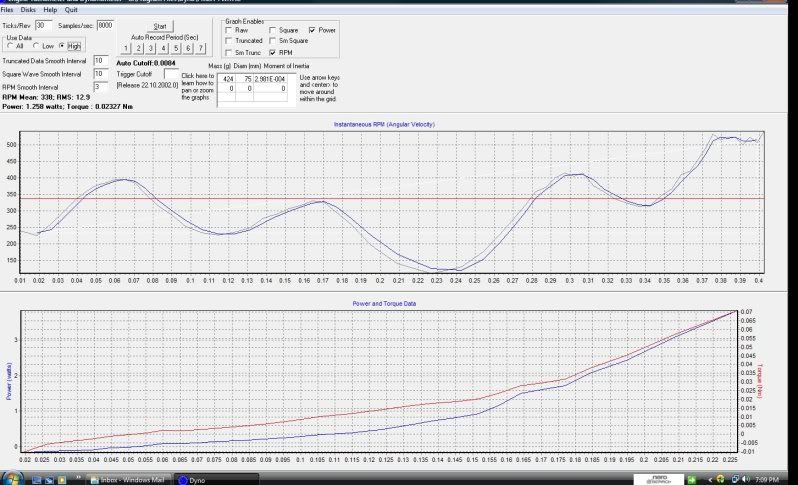
Overall it was a fun project, but I am not sure how accurate it is. I will do some more tests on some of my other engines. I think there is a newer program out there that uses a computer mouse's scroll wheel for input.
Well its starting to get warm finally and I think this will be my last Milling/Lathing project until the fall. As soon as it gets hot, I am outside most of the time. Summer is too short in Canada!
But I will still be working on/Cruising in this:
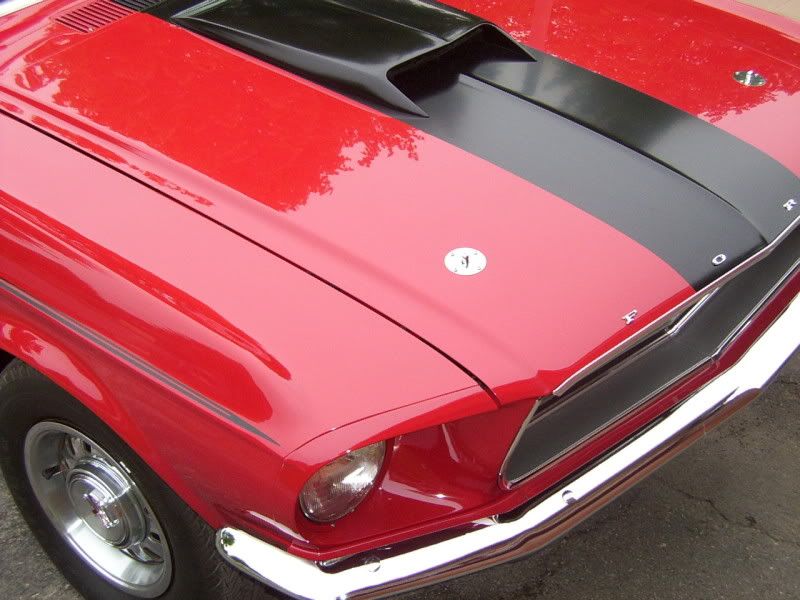
Iron Horse