- Joined
- Jan 17, 2009
- Messages
- 887
- Reaction score
- 82
I have an old works friend who's just getting started in Model Engineering along with his 11 year old son who's his showing a great interest in engines with a developing tallent for 3D CAD. Chatting to them got me thinking about an engine that could be built in a relative short time with limited equipment and I came up with the simple mill engine design that I showed the drawings her http://madmodder.net/index.php/topic,8128.0.html (be warned it has mistakes) that a Dad or Grandad could make together
Hence Lads and Dads.
The design is based on this engine that I saw at the Northern Mill Engine Association at Bolton at their Christmas steam up.
http://www.nmes.org/
I've used standard bar stock size to eliminate milling along with a piston valve, the fly wheel can be a standard 4" Stuart wheel or a fabricated one, I will also use lower cost material avoiding as must has posible copper based alloys.
Any way thats enough of that lets get on with the job,
You will need a small lathe an 1/2 decent drill with a good drill vice and some way of accuratly marking out like this
Just a cheep dig caliper with the legs cut back to form a set of odd legs
First Up the steam chest from 5/8 square ally. Cut a chunk off the bar face off to length in a four jaw and mark out the position for the piston valve.
The back into the four jaw and using a wobble bar set the centre pop running true
Deep centre drill then to avoid the use of expensive reamers drill through with a 5.9mm or a 7/32 drill this will cut over size and make the hole near to dam it 6mm, if the bar you're going to make the piston velve out of is a bit tight just lap it down for a nice slide fit.
Then accuratly mark out the position for the inlet ports don't centre pop them, into the drill vice and line up with a sticky pin this is just a pin held onto the chuck with platercene and nudged until it runs true. Clamp the vice to the drill table
The start with a small centre drill then follow up with a 3mm drill, don't unclamp the vice from the table just losen the jaws and slide the job along to line up the second hole again with the sticky pin a drill that one, do the same with the exhaust holes.
Mark out for the position of central inlet fead, and the 2mm dia clamp down holes, you don't need the sticky pins to line these holes up as their positions are not as critical just use the centre drill.
Thats it job done, just a few more holes to drill in it off the inlet and rod gland fixtures when they are made.
The deburing tool is what my late Dad made I can tell he made it as it's got his personality writen all over it.
Stew
Hence Lads and Dads.
The design is based on this engine that I saw at the Northern Mill Engine Association at Bolton at their Christmas steam up.
http://www.nmes.org/
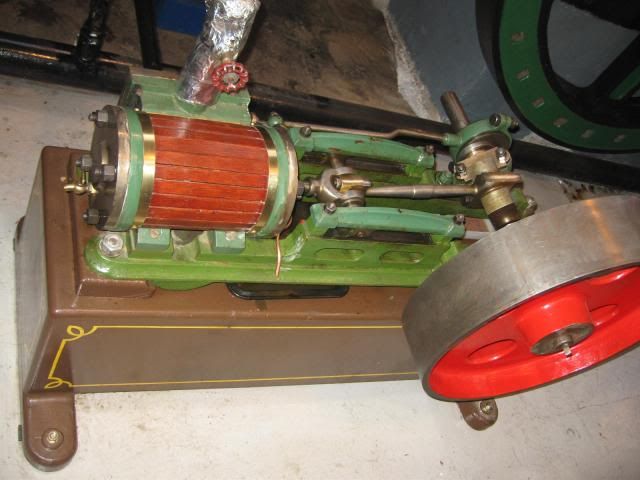
I've used standard bar stock size to eliminate milling along with a piston valve, the fly wheel can be a standard 4" Stuart wheel or a fabricated one, I will also use lower cost material avoiding as must has posible copper based alloys.
Any way thats enough of that lets get on with the job,
You will need a small lathe an 1/2 decent drill with a good drill vice and some way of accuratly marking out like this
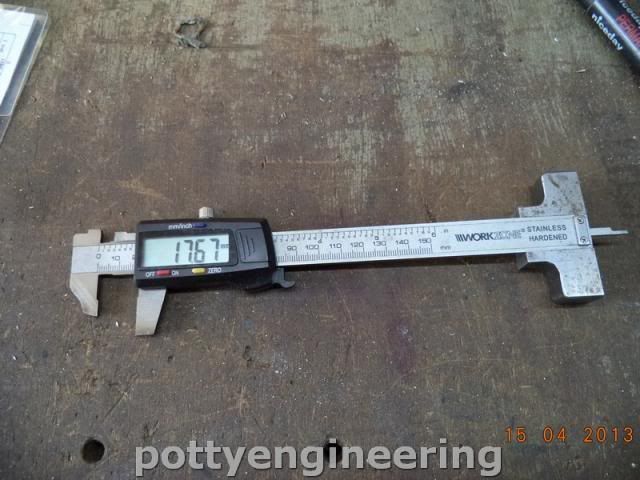
Just a cheep dig caliper with the legs cut back to form a set of odd legs
First Up the steam chest from 5/8 square ally. Cut a chunk off the bar face off to length in a four jaw and mark out the position for the piston valve.
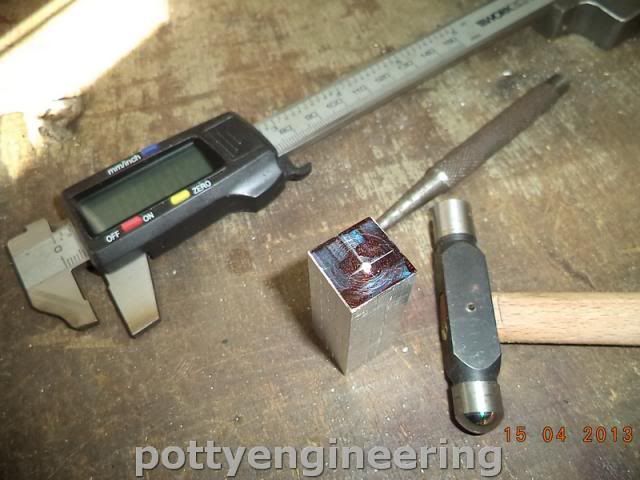
The back into the four jaw and using a wobble bar set the centre pop running true
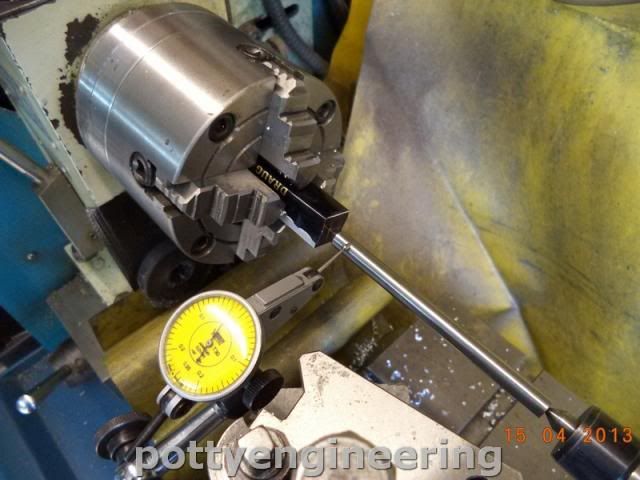
Deep centre drill then to avoid the use of expensive reamers drill through with a 5.9mm or a 7/32 drill this will cut over size and make the hole near to dam it 6mm, if the bar you're going to make the piston velve out of is a bit tight just lap it down for a nice slide fit.
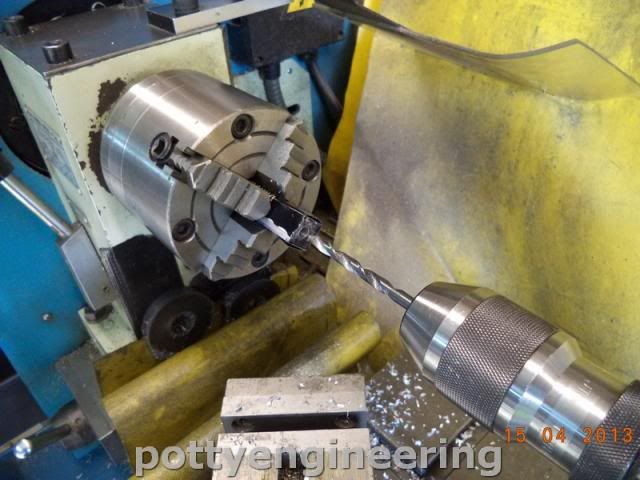
Then accuratly mark out the position for the inlet ports don't centre pop them, into the drill vice and line up with a sticky pin this is just a pin held onto the chuck with platercene and nudged until it runs true. Clamp the vice to the drill table
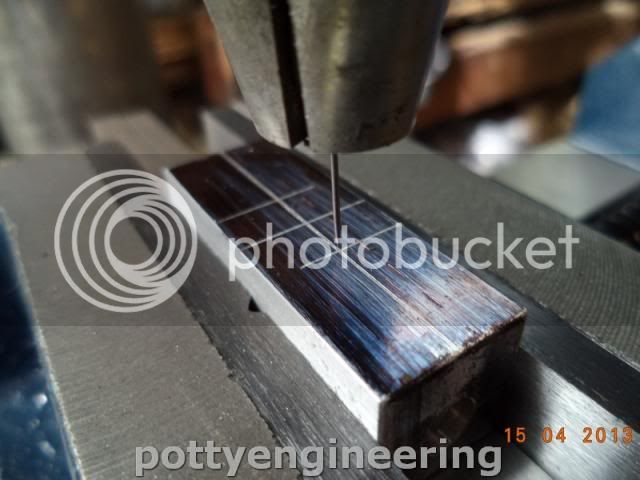
The start with a small centre drill then follow up with a 3mm drill, don't unclamp the vice from the table just losen the jaws and slide the job along to line up the second hole again with the sticky pin a drill that one, do the same with the exhaust holes.
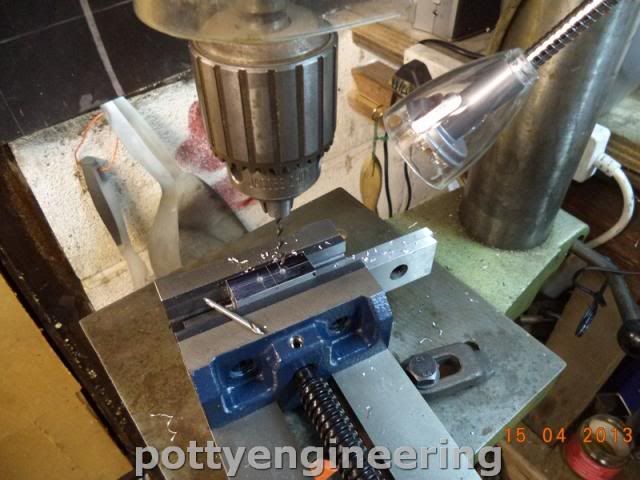
Mark out for the position of central inlet fead, and the 2mm dia clamp down holes, you don't need the sticky pins to line these holes up as their positions are not as critical just use the centre drill.
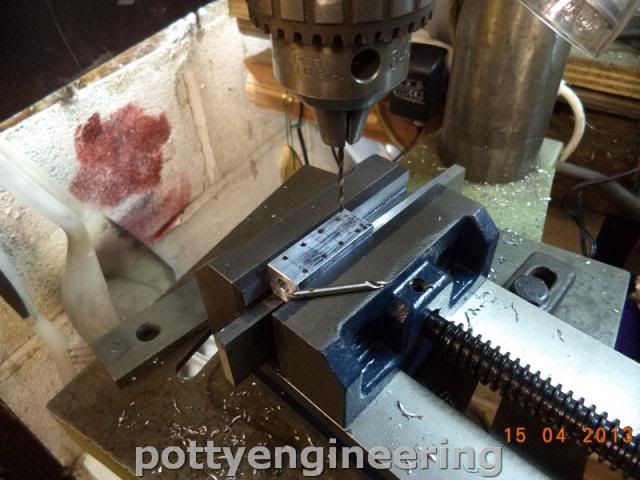
Thats it job done, just a few more holes to drill in it off the inlet and rod gland fixtures when they are made.
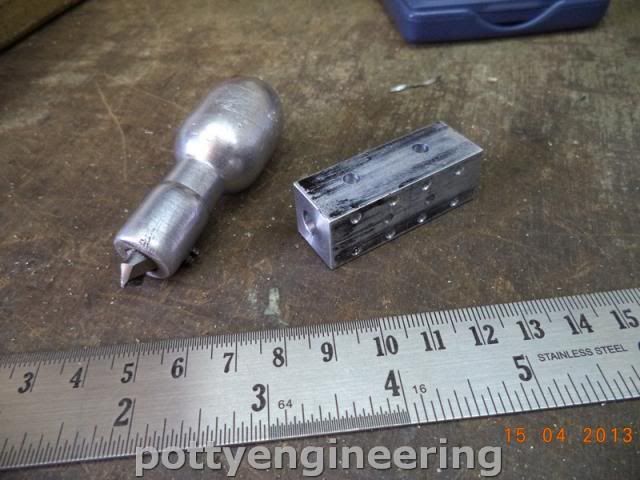
The deburing tool is what my late Dad made I can tell he made it as it's got his personality writen all over it.
Stew