- Joined
- Feb 17, 2008
- Messages
- 2,330
- Reaction score
- 445
Over the years my lathes have gotten heavier and more rigid. From a Unimat in the 50's and 60's, through South Bend 9's and 10's in the 70's and 80's, a Nardini Heavy 10 in the 80's and 90's and now a Hardinge clone. With each move up it has been more difficult to position the tailstock accurately. No problem in the early days, but now with the Hardinge clone the stiction of the dovetail ways it was getting more difficult. It has not helped that age of the operator has caused various shoulder ailments either.
I have been pushing the tailstock away from the headstock using the carriage for a long time. To move toward the headstock I would position the carriage next to tailstock and then push the tail stock against the carriage while positioning everything with the carriage hand wheel. Big problem was I could not see where the tool in the tailstock was being positioned as I was too far to the right. All in all it was awkward.
The photos show the solution I came up with. I did not want to drill and tap holes in either the tailstock or the headstock so I used the bolts that retain the way wipers on each. I inserted spacers under these bolts to allow them to be tightened down. In the factory configuration they are only snugged up enough to hold the wipers in position and expand it slightly. A part with two slots in it and holes that match the wiper retaining bolts was made with an oversize 1/8 hole running the length of it. An E-clip is fitted to the rod in left hand slot and that provides a stop for the rod that goes in the 1/8 hole such that when the rod is pushed in it passes through the second slot and when retracted it just clears the second slot.
On the tailstock a block is mounted the same way with a protrusion that engages the second slot on the carriage part. When engaged the rod can be pushed in and lock the tailstock to the carriage. A knob was added to the 1/8 rod and a spring to keep the rod retracted.
Operation is to position the carriage against the tail stock and then push the knob to lock them to each other. Then hand wheel the carriage/tailstock into position. While moving the tension will keep the rod in position, but as soon as the tension is relaxed the sprling disengages them.
Gail in NM
I have been pushing the tailstock away from the headstock using the carriage for a long time. To move toward the headstock I would position the carriage next to tailstock and then push the tail stock against the carriage while positioning everything with the carriage hand wheel. Big problem was I could not see where the tool in the tailstock was being positioned as I was too far to the right. All in all it was awkward.
The photos show the solution I came up with. I did not want to drill and tap holes in either the tailstock or the headstock so I used the bolts that retain the way wipers on each. I inserted spacers under these bolts to allow them to be tightened down. In the factory configuration they are only snugged up enough to hold the wipers in position and expand it slightly. A part with two slots in it and holes that match the wiper retaining bolts was made with an oversize 1/8 hole running the length of it. An E-clip is fitted to the rod in left hand slot and that provides a stop for the rod that goes in the 1/8 hole such that when the rod is pushed in it passes through the second slot and when retracted it just clears the second slot.
On the tailstock a block is mounted the same way with a protrusion that engages the second slot on the carriage part. When engaged the rod can be pushed in and lock the tailstock to the carriage. A knob was added to the 1/8 rod and a spring to keep the rod retracted.
Operation is to position the carriage against the tail stock and then push the knob to lock them to each other. Then hand wheel the carriage/tailstock into position. While moving the tension will keep the rod in position, but as soon as the tension is relaxed the sprling disengages them.
Gail in NM
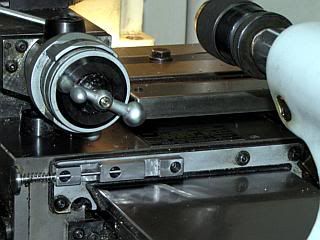
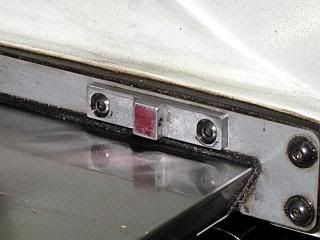
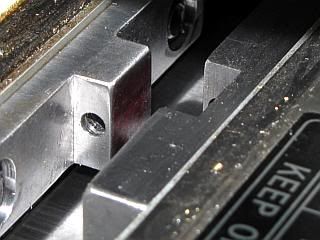
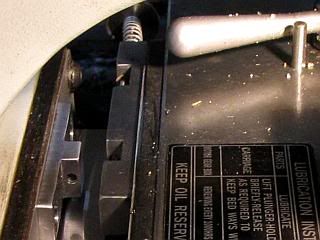