- Joined
- Feb 17, 2008
- Messages
- 2,330
- Reaction score
- 445
On to the crankshaft. Before starting, I drilled and reamed a 1/8 inch hole in a scrap of the same material I will be using for the connecting rod. This is just to give a check gage for the crankpin when it is turned. I could have made the connecting rods first as they are an indepentent part, but I was anxious to make the crankshaft.
I started by chucking a length of 5/8 inch diameter 12L14 in the lathe with enough protruding to cut the from the crankdisk to the front end of the shaft. After facing the end, the 0.188 (3/16) diameter for the propeller mounting shaft was roughed to about 0.02 oversize and the bearing area was roughed to about 3/8 diameter. The reason for roughing these first is to get rid of the stressed skin that most cold rolled material has. If the bearing area was not roughed before finish turning the prop shaft, there is a good chance that the shaft will warp a little bit when the bearing area is turned. I used a VBMT 35 degree carbide insert with a 0.015 tip radius for all turning operations. After roughing, I put a 60 degree center hole in the end of the shaft and finish turned the prop bearing area. I did not find it necessary to use a center during any turning operations, but the center is still necessary to be able to use a gear puller to remove the prop driver if/when the finished engineis disassembled.
After the propshaft was turned, an additional section 0.156 long was turned to 0.203 diameter for the for the propdriver. The end of the shaft was chamfered at 45 degrees so the die would start true and the propshaft was threaded 10-32 using a die. The die was started true by applying pressure with the tailstock drill chuck. The chuck was opened so the jaws were inside the chuck body and pressure applied with the tailstock hand wheel while the first 4 or 5 turns of the thread were formed.
Not photographed, the area of the prop driver was lightly knurled with a single wheel straight knurl to raise the diameter to about 0.206. This probably should have been done before the finish turning of the propshaft because of the pressure of the knurling tool, but as it was a light knurl there was no bending of the shaft. This is a deviation from the drawings as the original used a taper on the shaft and a mating taper on the prop driver. Both work, so it is just a matter of preference and my being lazy.
The 0.250 diameter for the bearing was finish turned and at the junction of the of the bearing and the crankdisk the tool was fed in about 0.012 to form a radiused recess. This is to make sure the crankdisk can seat on the thrust bearing. The thrust bearing could have been recessed to accomplish the same results. In either method it is important that a radius be formed at the junction of the crankdisk and the shaft to help prevent stress cracks from forming at the junction. On a larger engine I would relieve the bearing rather than the shaft.
After forming the radius, I faced off the front of the crankdisk and polished it so it would run smoothly on the thrust bearing.
While turning the bearing surface of the shaft, I checked for a slightly tight fit of the crankshaft in the front bearing and then polished the crankshaft with abrasive paper starting with 600 grit and graduating up to 1200 grit using light oil.
The crankshaft was fed out of the chuck to allow the crankdisk section to be polished a little bit and then cutoff with sufficient allowance for the crankpin to be turned.
Gail in NM,USA
I started by chucking a length of 5/8 inch diameter 12L14 in the lathe with enough protruding to cut the from the crankdisk to the front end of the shaft. After facing the end, the 0.188 (3/16) diameter for the propeller mounting shaft was roughed to about 0.02 oversize and the bearing area was roughed to about 3/8 diameter. The reason for roughing these first is to get rid of the stressed skin that most cold rolled material has. If the bearing area was not roughed before finish turning the prop shaft, there is a good chance that the shaft will warp a little bit when the bearing area is turned. I used a VBMT 35 degree carbide insert with a 0.015 tip radius for all turning operations. After roughing, I put a 60 degree center hole in the end of the shaft and finish turned the prop bearing area. I did not find it necessary to use a center during any turning operations, but the center is still necessary to be able to use a gear puller to remove the prop driver if/when the finished engineis disassembled.
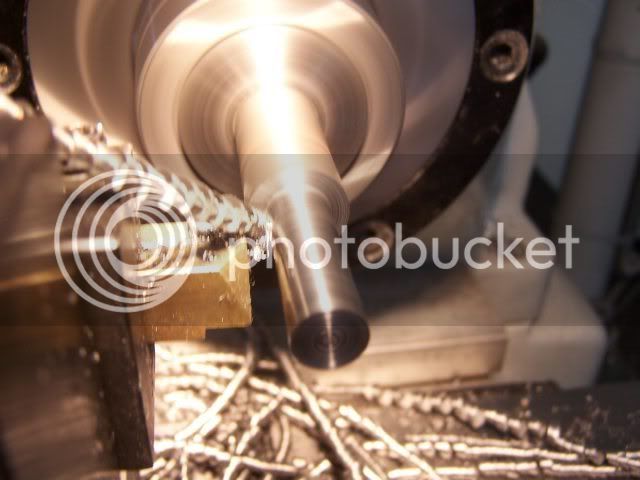
After the propshaft was turned, an additional section 0.156 long was turned to 0.203 diameter for the for the propdriver. The end of the shaft was chamfered at 45 degrees so the die would start true and the propshaft was threaded 10-32 using a die. The die was started true by applying pressure with the tailstock drill chuck. The chuck was opened so the jaws were inside the chuck body and pressure applied with the tailstock hand wheel while the first 4 or 5 turns of the thread were formed.
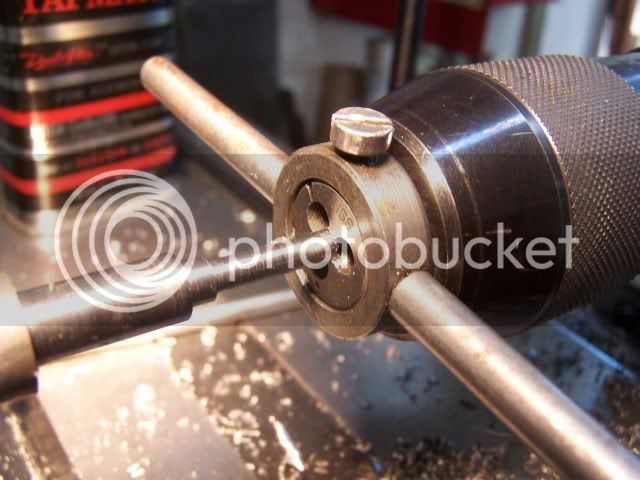
Not photographed, the area of the prop driver was lightly knurled with a single wheel straight knurl to raise the diameter to about 0.206. This probably should have been done before the finish turning of the propshaft because of the pressure of the knurling tool, but as it was a light knurl there was no bending of the shaft. This is a deviation from the drawings as the original used a taper on the shaft and a mating taper on the prop driver. Both work, so it is just a matter of preference and my being lazy.
The 0.250 diameter for the bearing was finish turned and at the junction of the of the bearing and the crankdisk the tool was fed in about 0.012 to form a radiused recess. This is to make sure the crankdisk can seat on the thrust bearing. The thrust bearing could have been recessed to accomplish the same results. In either method it is important that a radius be formed at the junction of the crankdisk and the shaft to help prevent stress cracks from forming at the junction. On a larger engine I would relieve the bearing rather than the shaft.
After forming the radius, I faced off the front of the crankdisk and polished it so it would run smoothly on the thrust bearing.
While turning the bearing surface of the shaft, I checked for a slightly tight fit of the crankshaft in the front bearing and then polished the crankshaft with abrasive paper starting with 600 grit and graduating up to 1200 grit using light oil.
The crankshaft was fed out of the chuck to allow the crankdisk section to be polished a little bit and then cutoff with sufficient allowance for the crankpin to be turned.
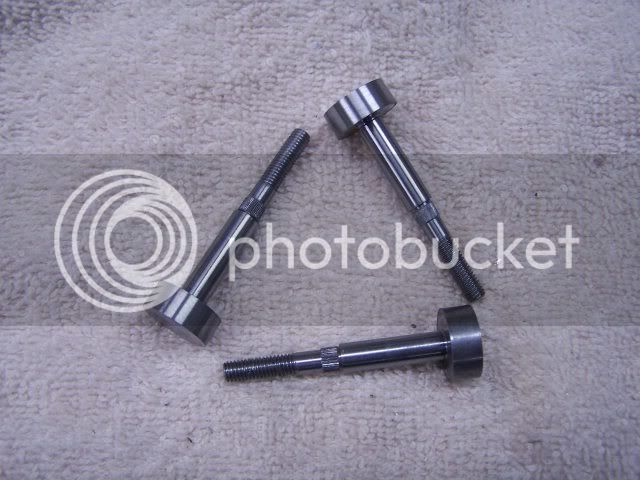
Gail in NM,USA