rake60
Well-Known Member
- Joined
- Jul 8, 2007
- Messages
- 4,756
- Reaction score
- 126
The maintenance man at work brought me a hollow shaft out of one of the presses.
The shaft was about 5" in diameter and 12" long. It had a few scared up critical fits
on it that needed to be polished clean.
I had to come up with a way of chucking it up safely quick.
This isn't a new idea, I've used it many times in the past.
I cut a short length of 3/4" square stock and center drilled in in the mill.
With the shaft chucked up in the lathe, the square stock was used to stabilize the
outboard end.
This quick mock up in my hobby shop shows the general idea.
That is fine for polishing, but it is NOT stable enough for turning.
I have another time tested method for doing that.
I turn a fit on a small disk for a stuff to stuff fit to the ID of the shaft or tubing.
A press fit will be impossible to remove after the internal stresses relieve during machining.
A fit with too much clearance has other obvious drawbacks.
Then I flip the disk around, chuck on the fit that was just turned and center drill the disk.
Another quick mock up:
That set up isn't going anywhere but around and around.
It isn't always a perfect center, but it's close enough for 99% of the things I do.
A better answer would be to buy a decent bull nose center, but how much fun could
that be?
Rick
The shaft was about 5" in diameter and 12" long. It had a few scared up critical fits
on it that needed to be polished clean.
I had to come up with a way of chucking it up safely quick.
This isn't a new idea, I've used it many times in the past.
I cut a short length of 3/4" square stock and center drilled in in the mill.
With the shaft chucked up in the lathe, the square stock was used to stabilize the
outboard end.
This quick mock up in my hobby shop shows the general idea.
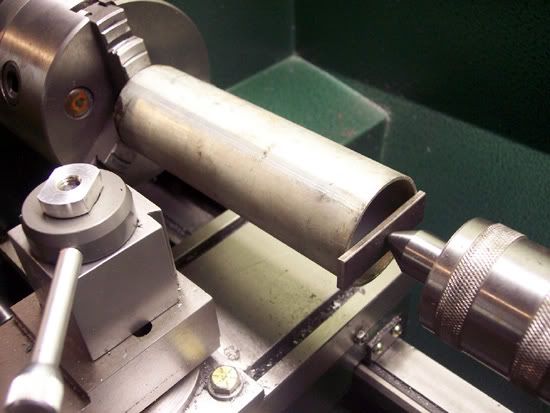
That is fine for polishing, but it is NOT stable enough for turning.
I have another time tested method for doing that.
I turn a fit on a small disk for a stuff to stuff fit to the ID of the shaft or tubing.
A press fit will be impossible to remove after the internal stresses relieve during machining.
A fit with too much clearance has other obvious drawbacks.
Then I flip the disk around, chuck on the fit that was just turned and center drill the disk.
Another quick mock up:
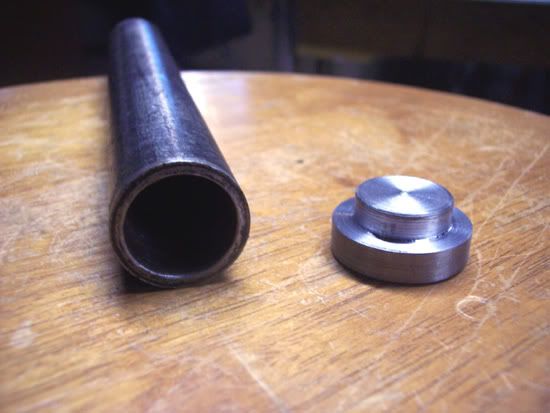
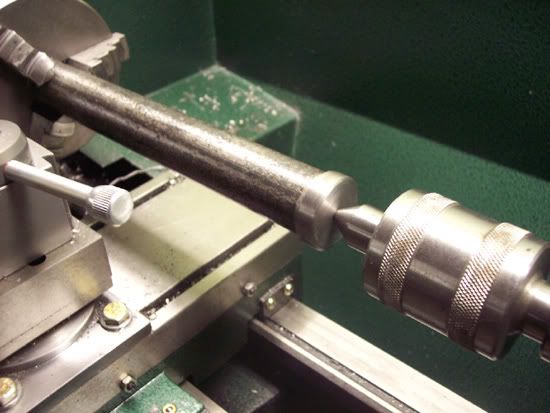
That set up isn't going anywhere but around and around.
It isn't always a perfect center, but it's close enough for 99% of the things I do.
A better answer would be to buy a decent bull nose center, but how much fun could
that be?
Rick