As most of you will know, I am a semi retired design engineer who builds model steam and gasoline engines. I have to publicly admit that while I am a fair hand at most things technical, I am a miserable failure at making needle valves for miniature carburetors. My lathe it too big to start with. Its a 10" x 18" lathe, and the chuck won't even close up small enough to hold a #2-56 screw (which most model carb needle valves seem to have as their main diameter.) I have to hold a smaller chuck (reclaimed off a dead electric drill) in my lathe chuck to even hold the screw. My 3 jaw chuck has about .003 runout in it, which I can live with, but it doesn't help. I sharpen my own HSS lathe bits, but still, trying to cut a 30 degree included taper on something that was only .085" diameter to start with has always eluded me. I have filed them. I have used fine emery paper on my flat file to dress them after filing. I have tried various Dremel type tools to grind them. I have held the screw in my electric drill and spun it against a revolving grindstone. All of this "Sort of" works. Then there are the people who advise that I should drill a .040" hole full length of a #2-56 screw and solder a darning needle into the hole. HAH!!! That trick is somewhat akin to trying to shove a dew worm up a wildcats---Oh never mind. It was only recently brought to my attention that THERE IS A BETTER WAY!!! Instead of trying to put a fine point on an a threaded screw which then screws INTO something else, what if the something else had an external thread and the needle valve actually did incorporate a darning needle soldered into a LARGER DIAMETER part which has an internal thread.--I know, kinda hard to visualize, but a picture is worth a thousand words. This is not my original idea. It is someone elses. I have created the attached 3D model, and what you see is a "section view" thru the carburetor, which clearly shows what I am blathering on about. I'm going to build this---Right Now. It seems like such a wonderful solution. I will post pictures and describe what I am doing as I progress. This one single "How to" could advance the art/craft of building succesful small i.c. engines at least a thousand years!! If it works the way it is supposed to, I will brag about it to you. If its a miserable flop (Like some things I have posted about) I will tell you.---Stay tuned!!!
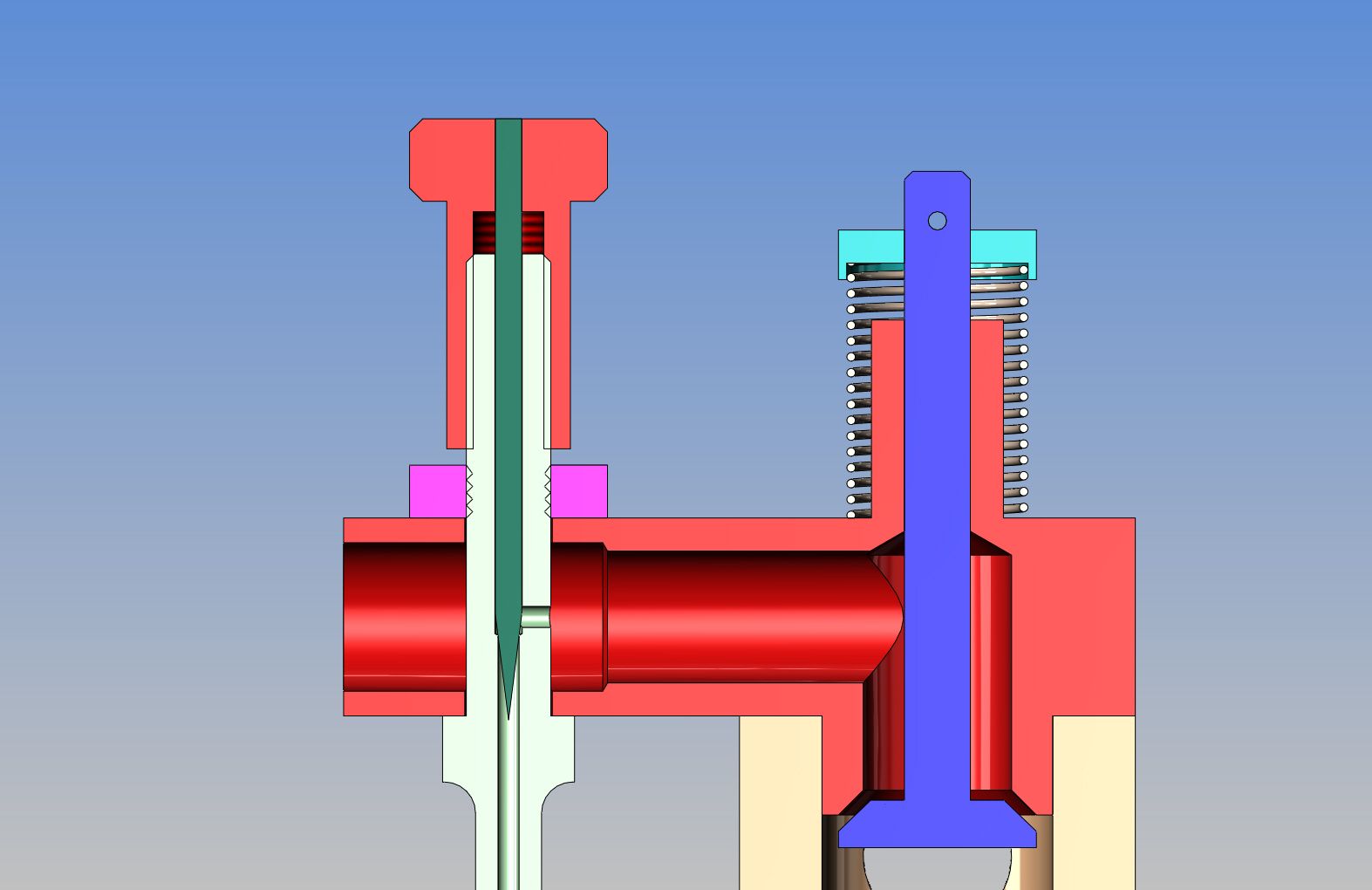