A week ago, my lathe quit. This was very upsetting, because it had just quit about 2 or 3 months ago, and had to be taken to Toronto for repairs. Fortunately, the safety switch inside the change gear cover had slipped out of adjustment, so my cost was negligible, but the hardest part was getting the lathe out of my tiny workshop and out into the garage and into my truck. I must declare right here, that I really like this lathe. I bought it new about 6 years ago, and it has performed faithfully for me. When it was brand new, I brought it home in my truck, unloaded it with my engine hoist, and hired a local machinery mover to move it into my machine shop. Two great big men stopped by, put a machine skate under the heavy end, and moved it into my machine shop. This took about 15 minutes, and they charged me $500. Never again, said I!!! That was out and out robbery. Three months ago, I moved the lathe out to my truck by myself and drove it to Toronto for repairs. When it was repaired, I unloaded it from my truck and moved it back into my machine shop by myself. That went well, but I was 74 years old in July, and it was just about more than I could handle. Last week I moved the lathe out to my truck by myself again for a trip to Toronto, but thought "there has to be an easier way to do this". I had designed and built a "transfer table" three months ago which I could load the lathe on and transport it from my truck to my machine shop. The really ugly part was moving the lathe from the wheeled "transfer table" back onto the cabinets which the lathe normally sets on.--But wait!!!! I'm a machine designer. Damn, I'll build a machine to assist me!!! (The lathe issue was a wire coming loose on the reverse terminal inside the lathes electrical cabinet.) This first picture shows me in the process of unloading the lathe from my truck, using my cherry picker hoist to place the lathe on the "transfer table".
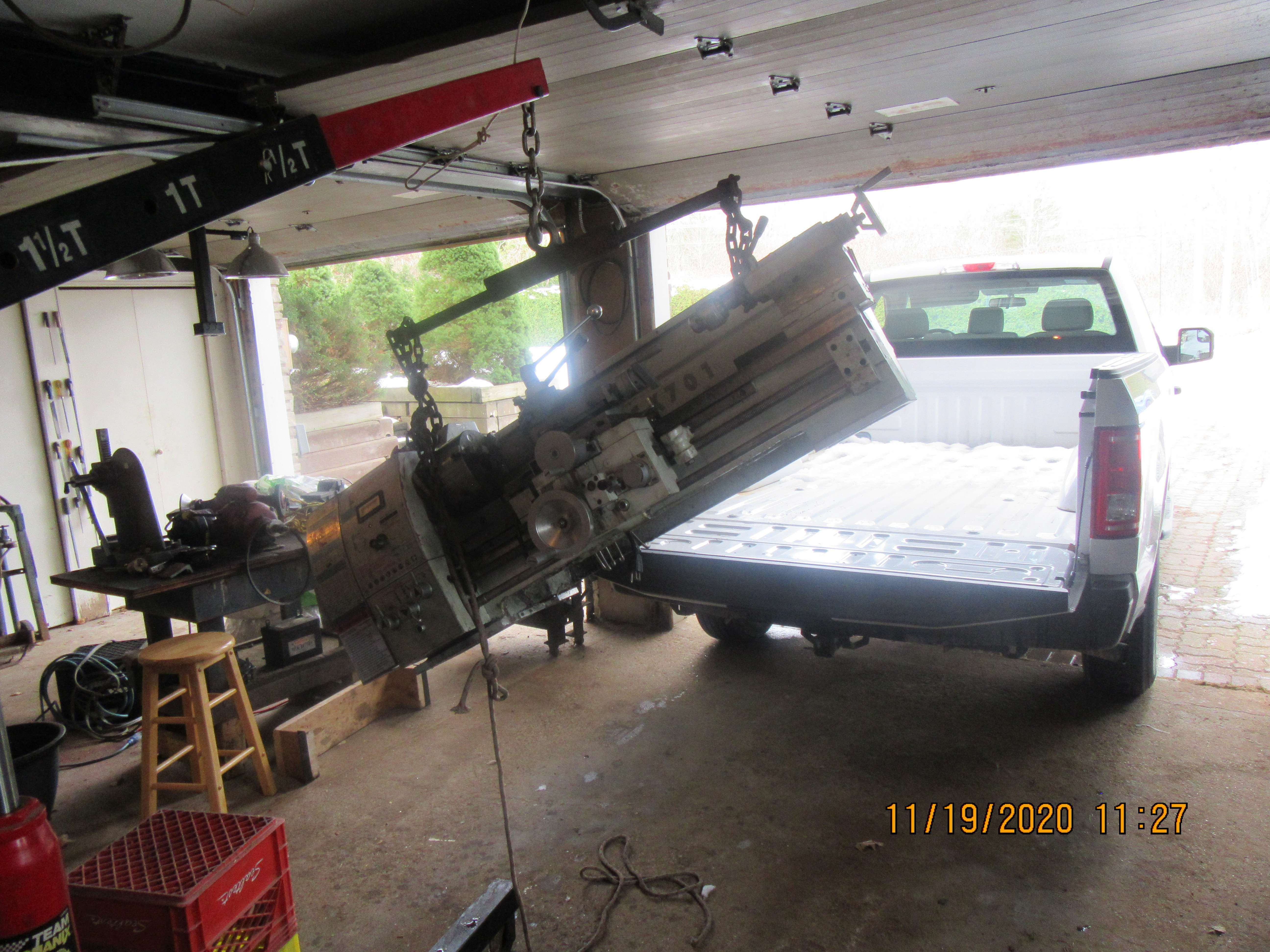
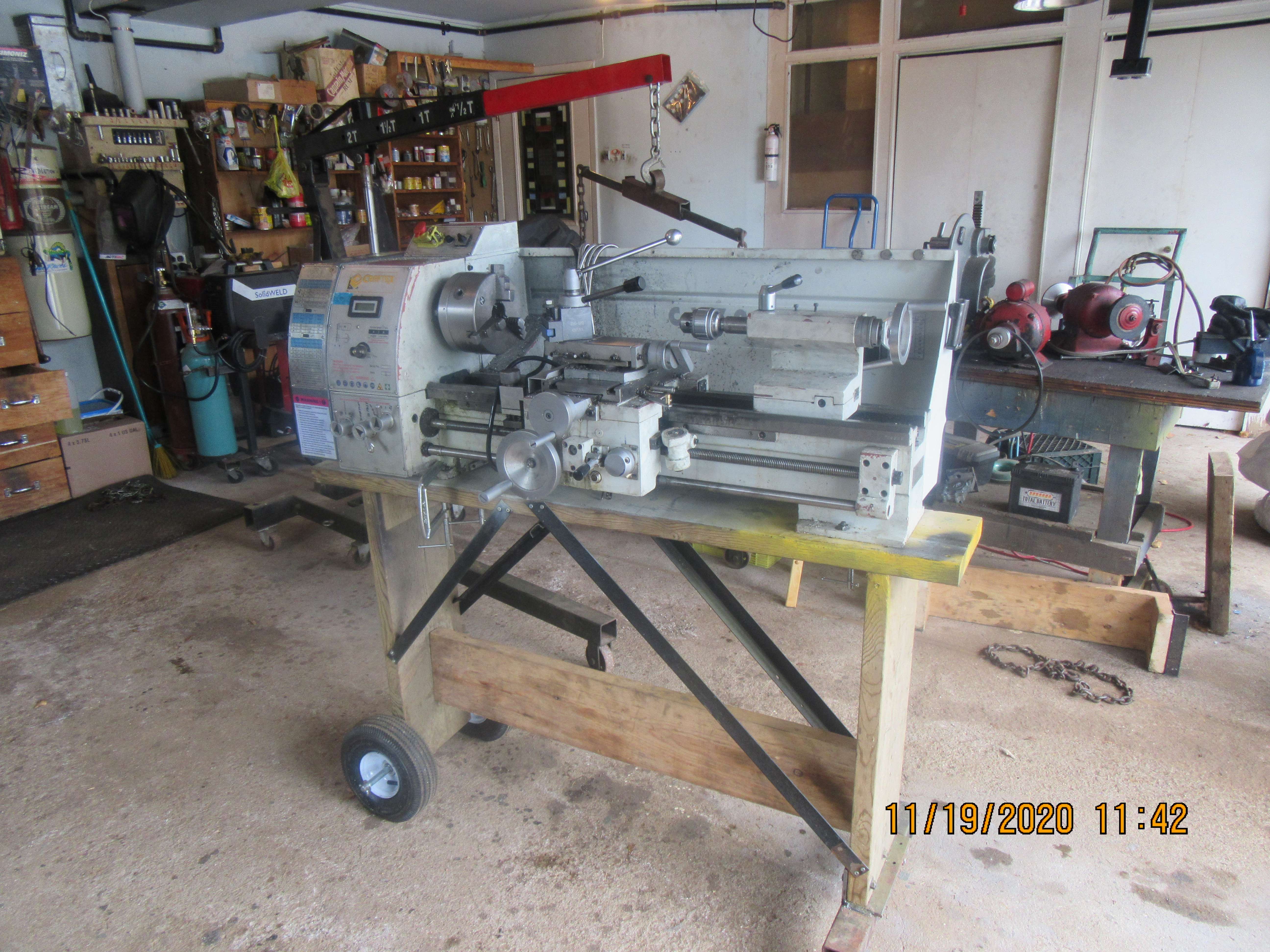