- Joined
- Jan 30, 2011
- Messages
- 365
- Reaction score
- 72
Hi Chris - I missed your post and just had a late reminder on email
.
Good to see them coming together, they are looking good so far.
Re the use of small taps - I agree it is always a bit heart in mouth with small taps but something you might like to see - it's a bit late now of course but in case you need it in the future....
Grind a small flat on the side of the tap just above the thread - just long enough to take a grubscrew point. Then turn and knurl a small disc about 25mm dia and 6/7mm thick and drill for the tap. Cross drill for a small grubscrew and you have a very controllable tap wrench for small taps. 25mm dia is just right for 10,8 BA and 2/2.5mm or so. The motion is very 'circular' as opposed to the wringing action of a tee bar. Originally I supported the tap by very lightly closing the chuck jaws - literally just touching but have recently found it much better to drill a small piece of brass to take the tap shank (loose fit) and hold that in the chuck as a guide.
Here are a couple of pics from the Waller build - its being used on the lathe but the principle's the same. It's 12BA and a smaller diameter wrench- about 19mm.
Having been down the route you show - there's even a couple of sprung loaded points to support the tap chuck now lying fairly redundant in the tray I can say this is much the better way, particularly for 'feel' as to whats happening with the tap.
Hope that's of use to you.
Not that much further to go now eh? Whats next to do?
regards - Ramon
Good to see them coming together, they are looking good so far.
Re the use of small taps - I agree it is always a bit heart in mouth with small taps but something you might like to see - it's a bit late now of course but in case you need it in the future....
Grind a small flat on the side of the tap just above the thread - just long enough to take a grubscrew point. Then turn and knurl a small disc about 25mm dia and 6/7mm thick and drill for the tap. Cross drill for a small grubscrew and you have a very controllable tap wrench for small taps. 25mm dia is just right for 10,8 BA and 2/2.5mm or so. The motion is very 'circular' as opposed to the wringing action of a tee bar. Originally I supported the tap by very lightly closing the chuck jaws - literally just touching but have recently found it much better to drill a small piece of brass to take the tap shank (loose fit) and hold that in the chuck as a guide.
Here are a couple of pics from the Waller build - its being used on the lathe but the principle's the same. It's 12BA and a smaller diameter wrench- about 19mm.
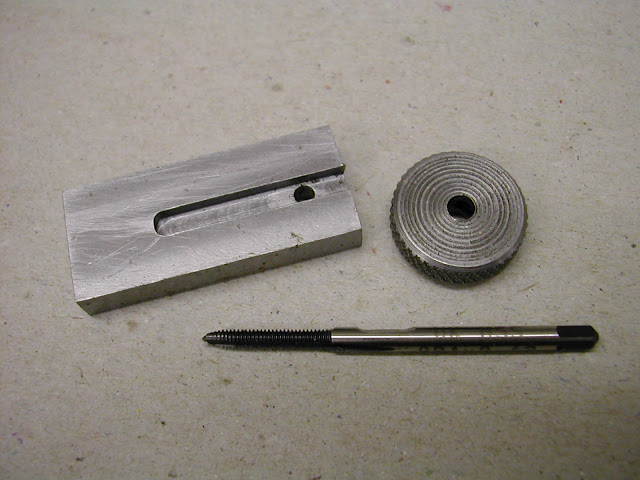
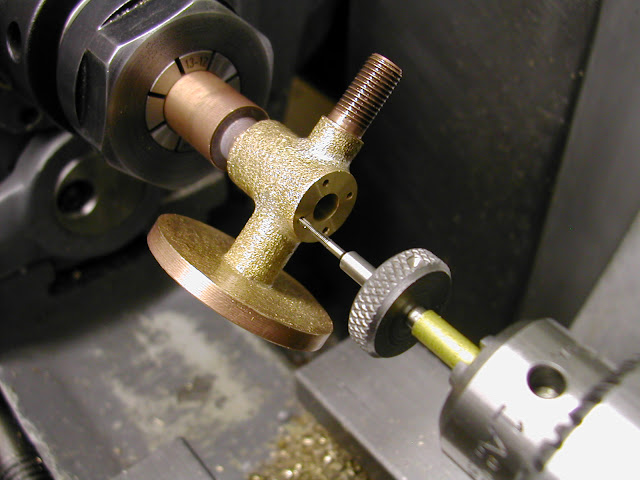
Having been down the route you show - there's even a couple of sprung loaded points to support the tap chuck now lying fairly redundant in the tray I can say this is much the better way, particularly for 'feel' as to whats happening with the tap.
Hope that's of use to you.
Not that much further to go now eh? Whats next to do?
regards - Ramon