- Joined
- Aug 25, 2007
- Messages
- 3,890
- Reaction score
- 715
I have an Enco Mill Drill that I bought 16 years ago. Long ago I fitted a DC gear motor to the X-Axis with an additional gear set that can be connected or disconnected by loosening a setscrew and sliding the big gear back, disengaging from the dogs on the screw.
I've been slowly collecting parts to convert it to CNC and while I have most of the mechanicals, I've yet to get stepper drivers and controller box. So, in the meantime, I'm thinking it might be interesting to go ahead and swap out the DC gear motor for one of my steppers. An arduino powered stepper motor on the X-axis could be handy. I'm thinking a keypad to input numbers and decimals and a left and right cursor button.
So far, from a functional standpoint, I see being able to input a decimal number, then each time I press the left or right cursor key, the table would move in that direction the distance indicated by the number I input. It would speed up gear cutting even more with my electronic dividing head. Now I have to see what other functions might be easily implemented..
Chuck
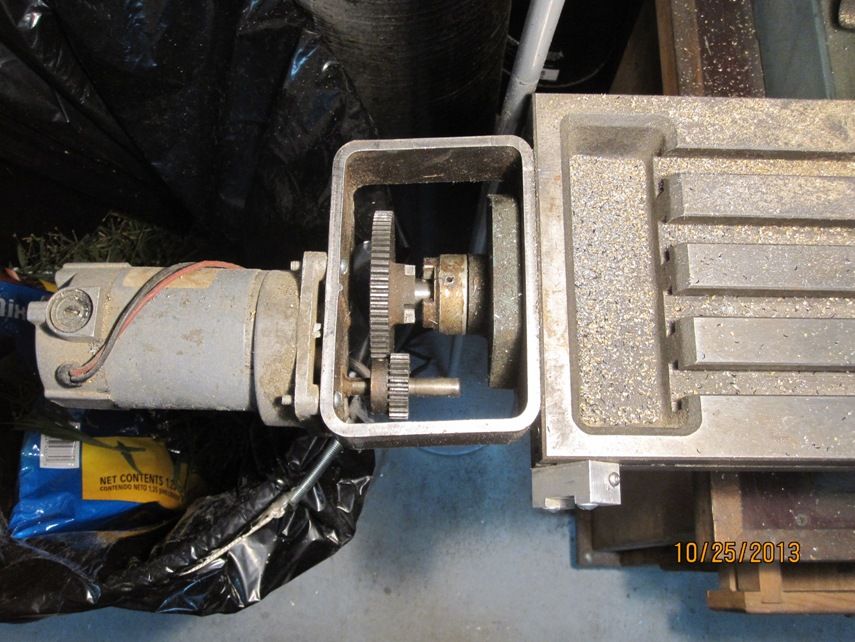
I've been slowly collecting parts to convert it to CNC and while I have most of the mechanicals, I've yet to get stepper drivers and controller box. So, in the meantime, I'm thinking it might be interesting to go ahead and swap out the DC gear motor for one of my steppers. An arduino powered stepper motor on the X-axis could be handy. I'm thinking a keypad to input numbers and decimals and a left and right cursor button.
So far, from a functional standpoint, I see being able to input a decimal number, then each time I press the left or right cursor key, the table would move in that direction the distance indicated by the number I input. It would speed up gear cutting even more with my electronic dividing head. Now I have to see what other functions might be easily implemented..
Chuck