Making the endblock in two pieces is the only way I can make this part.
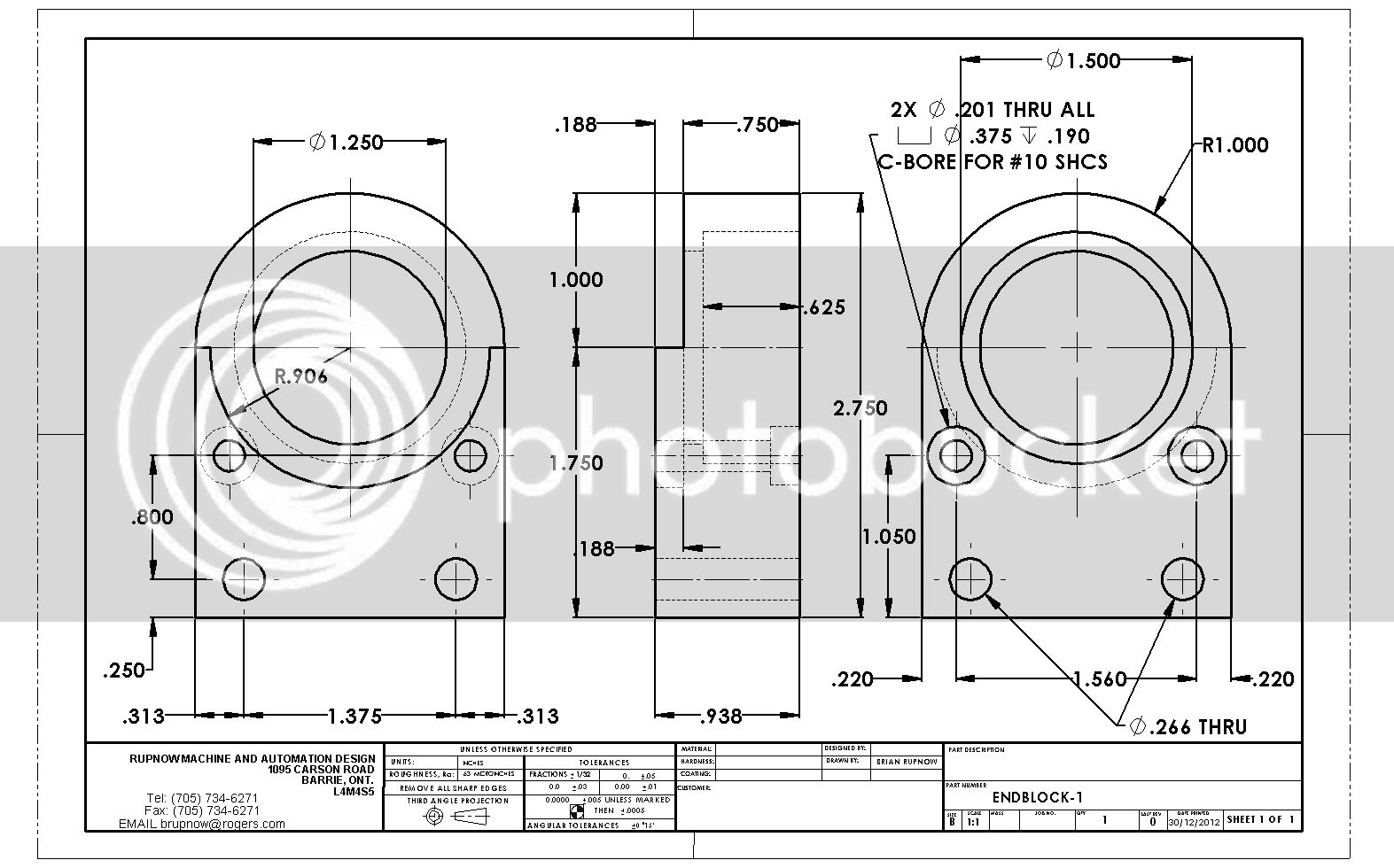
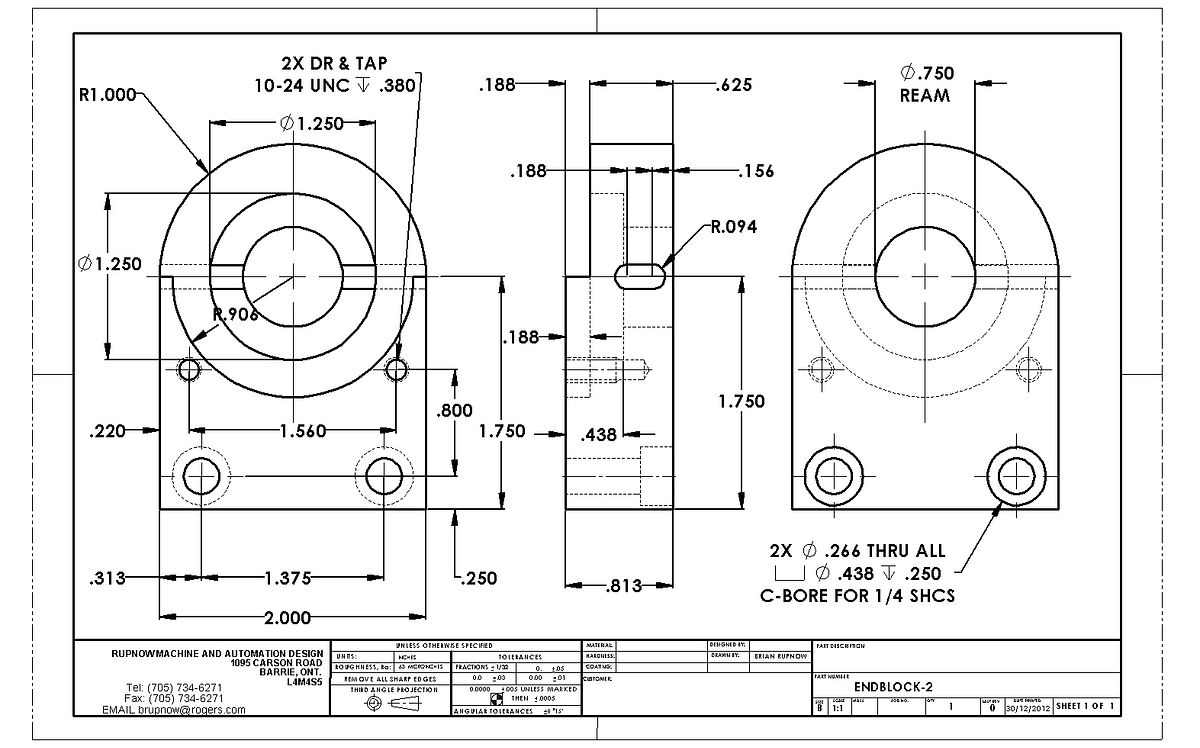
Just enough room--barely, barely---with a cut down allen wrench, to reach in and tighten the screws in the shaft collar.
![]()
Pat---I hadn't even noticed that. I had to play the video over again to see what you were talking about, and you're right, it was shaving off a cut the width of the blade. I have the clutch working much more freely now. I put a v-belt bulley on it and set it up with a belt drive from ny lathe and drove it at 550 rpm for about 20 minutes to take the stiffness out of it. Its too cold out in my big garage to mess with the atkinson engine now, but when the weather warms up (which may be the end of March) I hope to make a video of the sawmill cutting a log driven by the Atkinson thru the clutch.---BrianVery nice Brian. Your saw mill must really be built well to be able to take a cut that only produces sawdust the width of the blade and not wander out of the kerf. Good job!
Pat
Enter your email address to join: