wheeltapper
Senior Member
- Joined
- Jun 25, 2010
- Messages
- 143
- Reaction score
- 14
Hi all
I've been trying to make a single tooth gear cutter using a form tool with hardened buttons and got nowhere.
I read on another forum someone used a cone drill to form the cutter shape but I didn't have much luck with that either.
so I thought' if I can't tilt the milling cutter tilt the blank.
so this is what I did,
first I fixed my dividing head to the mill with packing under the l/h side to give 5 degrees of tilt to the spindle.
then I held the blank in a collet
then I fixed a 120 tooth gear to the div head and indexed the spindle so the blank was square to the bed and took a skim across the end
then I fitted a normal milling cutter of a diameter equal to the dia of the button you would use doing it the other way, indexed the spindle 1 tooth which is 3 degrees,fed the cutter up to the blank and fed in the recommended cutting distance.
I placed the cutter on the side of the blank which would put the leading (widest) edge of the tip at the bottom and took a cut.
when it's across far enough, raise the cutter, index 2 teeth the other way and take the other cut.
finally index back to zero then go round 180 degrees which puts the cutting edge on top and take a skim across the top with the end of the milling cutter to relieve the tip.
here's the finished cutter
here's an aluminium gear done as a test meshed with a change wheel.
the advantage of this is you can use any ordinary cutter.
there is a sad ending to this tho, I was so pleased that it worked I tried it on a steel gear blank , unfortunately I was in such a hurry to try it out I hardened the cutter but forgot to temper it and 5 teeth into the steel blank I chipped the end off.
but I can make another one.
so I did,
any comments welcome.
Roy
I've been trying to make a single tooth gear cutter using a form tool with hardened buttons and got nowhere.
I read on another forum someone used a cone drill to form the cutter shape but I didn't have much luck with that either.
so I thought' if I can't tilt the milling cutter tilt the blank.
so this is what I did,
first I fixed my dividing head to the mill with packing under the l/h side to give 5 degrees of tilt to the spindle.
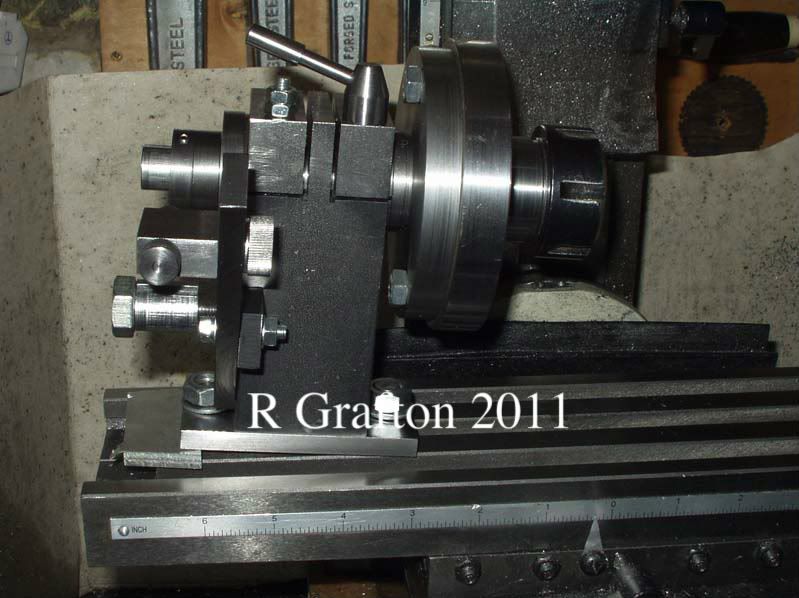
then I held the blank in a collet
then I fixed a 120 tooth gear to the div head and indexed the spindle so the blank was square to the bed and took a skim across the end
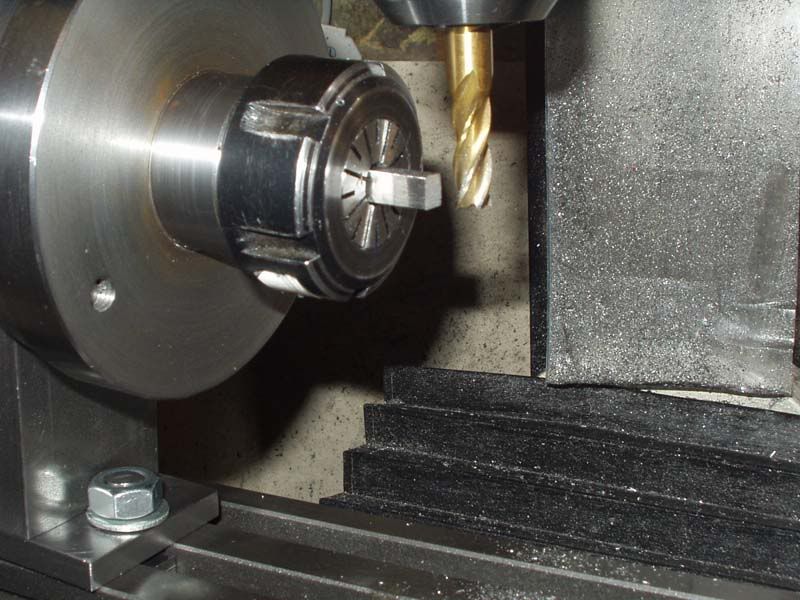
then I fitted a normal milling cutter of a diameter equal to the dia of the button you would use doing it the other way, indexed the spindle 1 tooth which is 3 degrees,fed the cutter up to the blank and fed in the recommended cutting distance.
I placed the cutter on the side of the blank which would put the leading (widest) edge of the tip at the bottom and took a cut.
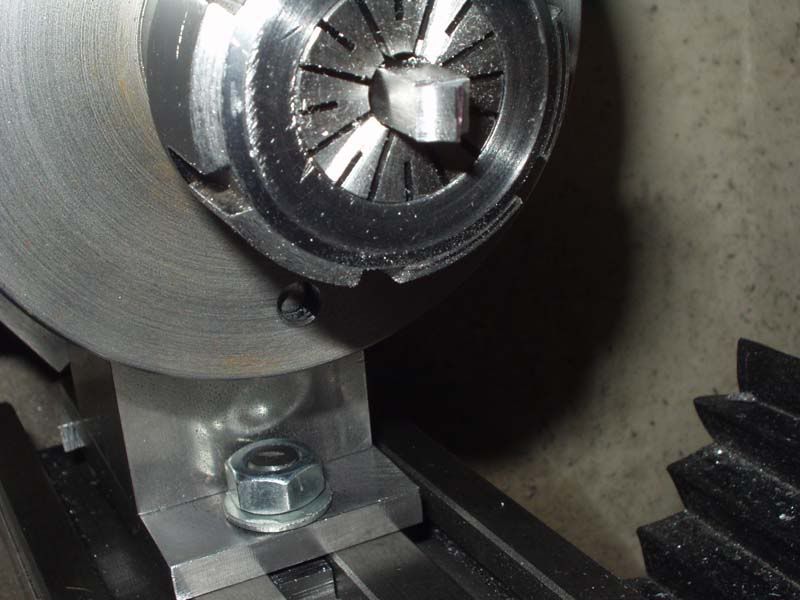
when it's across far enough, raise the cutter, index 2 teeth the other way and take the other cut.
finally index back to zero then go round 180 degrees which puts the cutting edge on top and take a skim across the top with the end of the milling cutter to relieve the tip.
here's the finished cutter
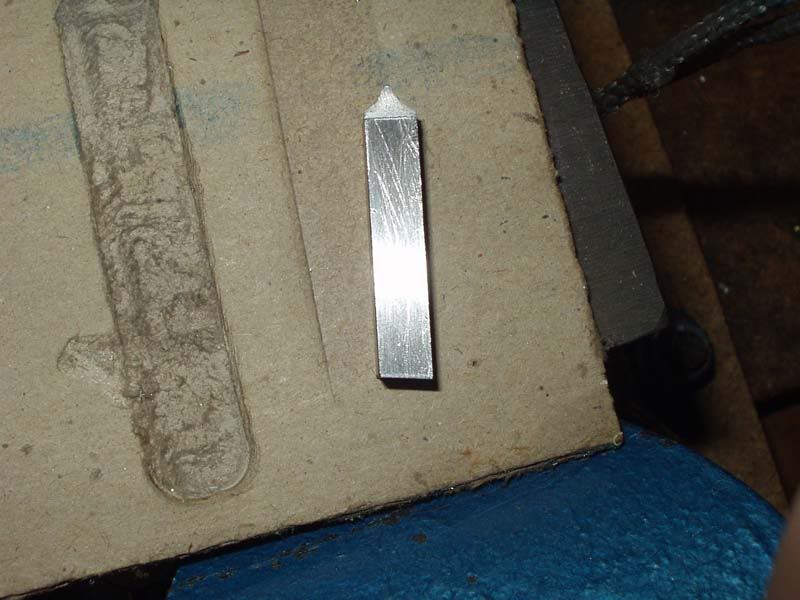
here's an aluminium gear done as a test meshed with a change wheel.
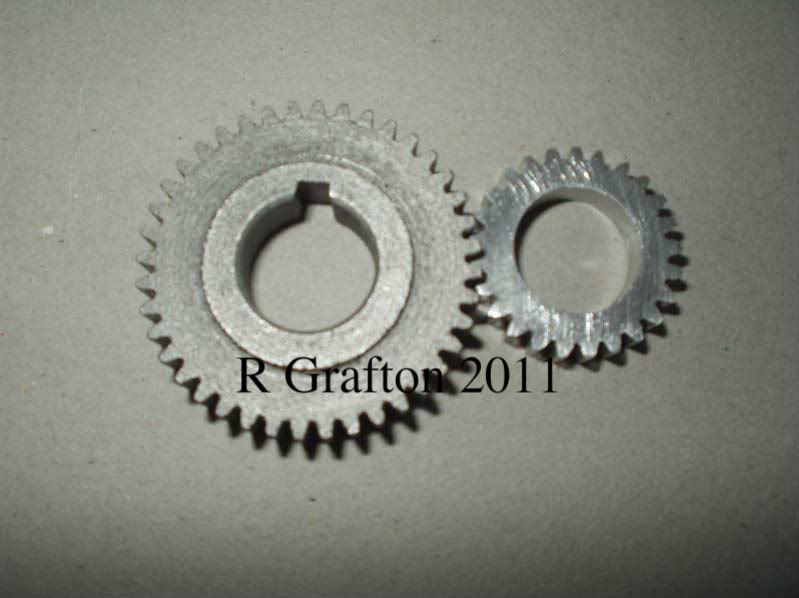
the advantage of this is you can use any ordinary cutter.
there is a sad ending to this tho, I was so pleased that it worked I tried it on a steel gear blank , unfortunately I was in such a hurry to try it out I hardened the cutter but forgot to temper it and 5 teeth into the steel blank I chipped the end off.
but I can make another one.
so I did,
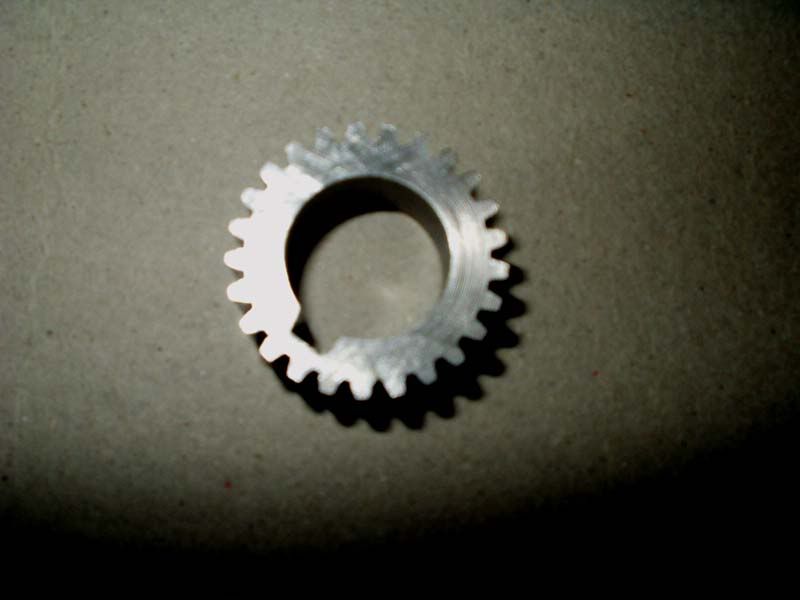
any comments welcome.
Roy