Last year's "SPLIT MONO" engine was a unique effort and a successful build. What would a two cylinder version look like? There are two ways to go here......and inline twin with both cylinders on one side of the crankshaft or a cross cylinder design, like an opposed engine with one cylinder each side of the crankshaft. I got to play with a lot of gears in the process.....and it ended up in a surprise finish!
The road to the T.R. engine starting this week!
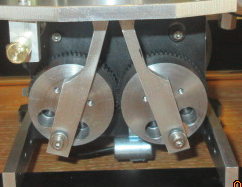
Last edited: