Generatorgus
Senior Member
- Joined
- Feb 25, 2010
- Messages
- 362
- Reaction score
- 167
Faux oiler/mixer.
Starting with a length of 3/8 hex stock, the sight glass, threaded center tube and pipe thread nipple were shaped, somewhat modeled after a real size oiler I have. The oil reservoir will only serve as an air passage to the mixer which will be inserted thru the hole where the actual sight glass should be.
Next a swing type filler hole closer was 'hacked' out of a piece of brass sheet, also a fake hold down nut made. The closeup looks rough under magnification, but doesn't hurt my eyes too bad if I don't look to hard. This closer will act as my air adjuster/ choke.
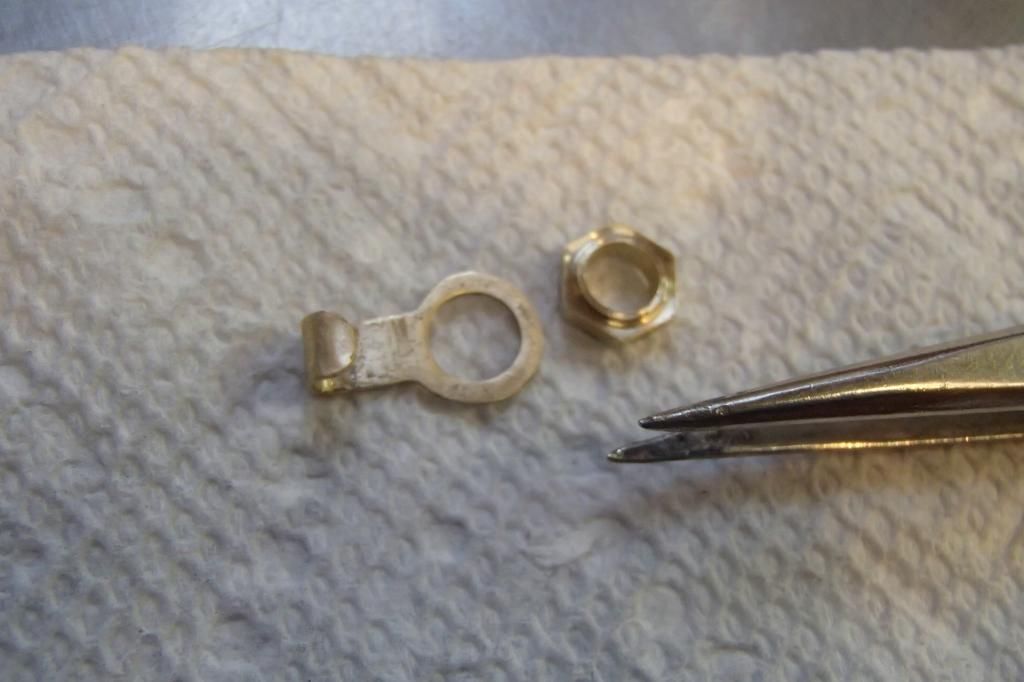
Then loctited together.
I made the top and bottom pieces earlier and forgot pics. I also substituted a length of 1/2 copper pipe for the glass. It may be permanent because the only 5/8 oiler glass I've found, seems too thick to work with my design. The top piece is threaded 1/4-40 to hold the oiler together.
After a bit of thought I started work on the spring loaded the spring loaded valve opening lever, which will only serve to hold the hole closer from moving.
Here all of the pieces laid out. The knurled piece serves only to cover the the spring hold down nut.
The needle valve body is 1/8 dia brass rod, drilled 1/32 partially thru from both ends and finished off with a #75 hole in the middle for the orifice. Seems a bit small to me, but I think it will be OK , if not I'll go a bit bigger, I'm only guessing.
One end threaded 5-48 for the needle holder/adjuster, the other end rounded a bit to accept the fuel tubing.
One end threaded 5-48 for the needle holder/adjuster, the other end rounded a bit to accept the fuel tubing.
The needle is a.024 dia needle which will be silver soldered in the holder.
For the holder, a 3/16dia brass bar drilled thru and tapped 5-48 then knurled and cut to length.
No real plan here, just making parts as I go.
The part that actually holds the needle is 1/8 rod threaded to match, with a .024 hole drilled thru, dimpled slightly at the end to help hold the solder and then cut off about an eighth inch long. The needle was pushed thru to approx. length and left long. This fit is very snug and will hold the needle in place while soldering. After soldering the piece will be threaded in and loctited in the end of the holder.
The part that actually holds the needle is 1/8 rod threaded to match, with a .024 hole drilled thru, dimpled slightly at the end to help hold the solder and then cut off about an eighth inch long. The needle was pushed thru to approx. length and left long. This fit is very snug and will hold the needle in place while soldering. After soldering the piece will be threaded in and loctited in the end of the holder.
Before I committed to the length of the needle, the valve body was loctited into the sight glass and drilled thru at the size of the venturi. Then the needle fitted for length.
I ended up with quite a few parts for something I didn't think would be this involved.
Next in line will be the exhaust valve.
GUS