- Joined
- Jun 4, 2008
- Messages
- 3,292
- Reaction score
- 635
Today I mounted the boiler inside the frame for a test fit.
I put some metal bars under the barrel and across the frame to get the boiler barrel approximately level with the firebox bottom sitting on the grate supports. Using a digital level the barrel is about 1 degree out of level with the frame top.
Next I wanted to find the height of the boiler's centerline above the top surface of the tee. I used a height gauge to measure the top plus a micrometer for the diameter and did a bit of arithmetic. Next I measured the OD of the smokebox using the DRO on the mill. Combining the two measurements allows computation of the length of the exhaust tube needed to support the smokebox and attached boiler to the tee.
Notice that there are 18 3/4" copper flues vs. the 7 1" flues that Kozo shows. So my total draft area is 8 inches square vs 5.5.
Another difference is that the smokebox is a slip fit over the front of the end of the boiler and will be just sealed with high-temp RTV, vs. being clamped as Kozo does. This allows expansion of both when hot.
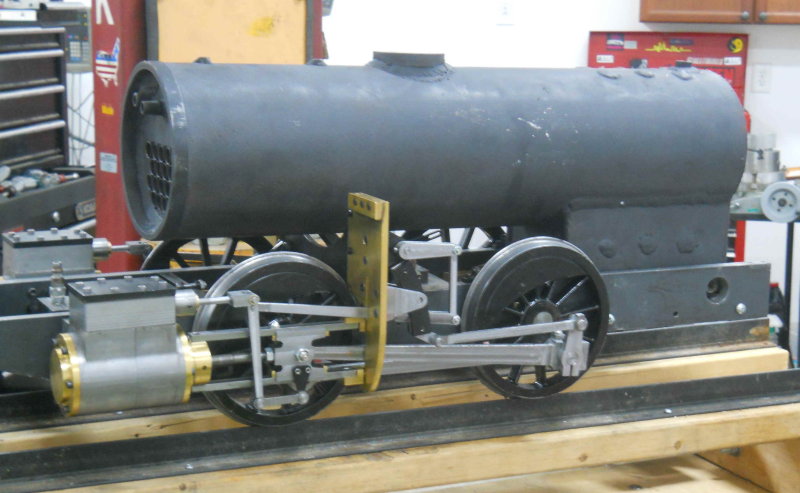
I put some metal bars under the barrel and across the frame to get the boiler barrel approximately level with the firebox bottom sitting on the grate supports. Using a digital level the barrel is about 1 degree out of level with the frame top.
Next I wanted to find the height of the boiler's centerline above the top surface of the tee. I used a height gauge to measure the top plus a micrometer for the diameter and did a bit of arithmetic. Next I measured the OD of the smokebox using the DRO on the mill. Combining the two measurements allows computation of the length of the exhaust tube needed to support the smokebox and attached boiler to the tee.
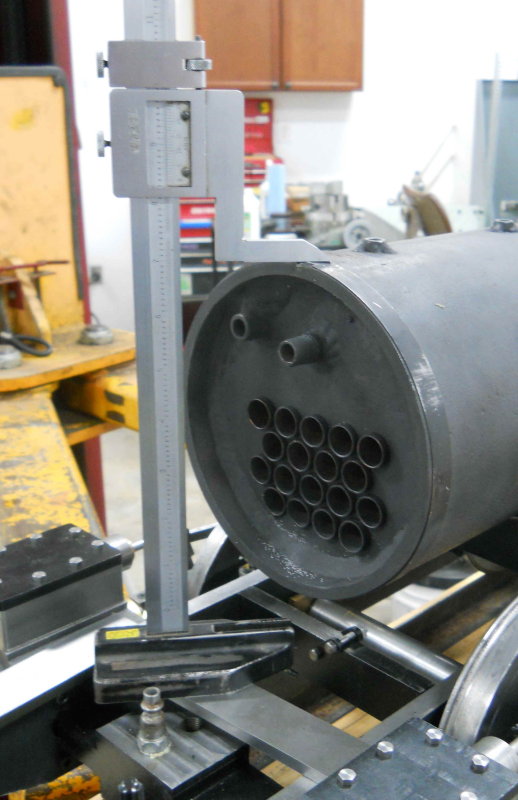
Notice that there are 18 3/4" copper flues vs. the 7 1" flues that Kozo shows. So my total draft area is 8 inches square vs 5.5.
Another difference is that the smokebox is a slip fit over the front of the end of the boiler and will be just sealed with high-temp RTV, vs. being clamped as Kozo does. This allows expansion of both when hot.