- Joined
- Jun 4, 2008
- Messages
- 3,294
- Reaction score
- 636
Next I measured the relative heights of the 3 flat surfaces that will have tapped holes. The left side mounts the cylinder; the center has the crosshead guides and valve pedestals, and the right is the top of the main bearings. The unmachined surfaces are quite close to their relative differences per plan, withing .030".
Next I used a small face mill to flatten each of the surfaces, taking the minimum needed. This meant removing only about .020" max. Then machined the faces of the bearing stands and both sides to a depth of 1.40" and keeping the width of the stands at 1.25". I managed to hit the front one pretty dead on, but the back ended up 8 thou thinner. I'll need to make the grooves in the bearings to match.
The next major step is machining the openings in the stands for the bearings. Once done, the bottom of the opening becomes the reference datum for facing the other two mounting surfaces. The center of the opening becomes the zero point of the x-axis, and the two outer faces of the stands become the datums for determining the engine centerline. All the mounting holes are positioned using this derived point in the XY plane and should help ensure that all the motion gear is straight and parallel.
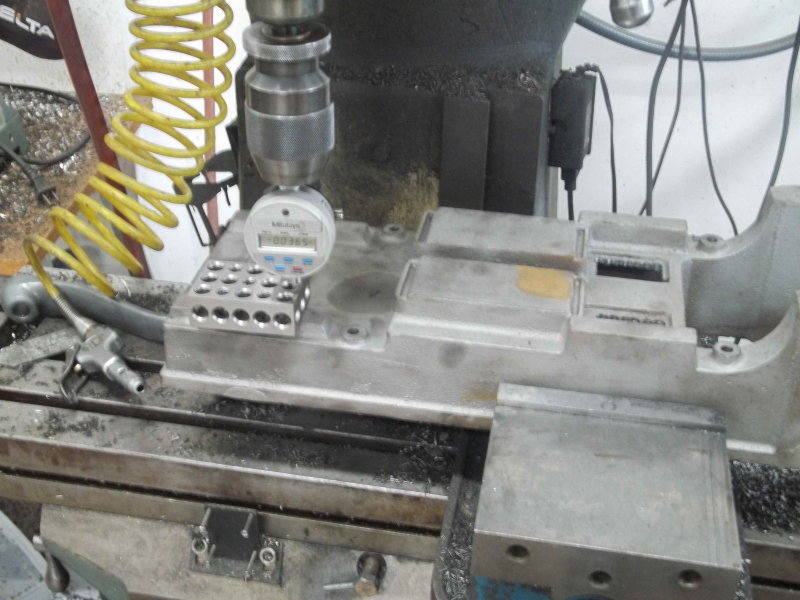
Next I used a small face mill to flatten each of the surfaces, taking the minimum needed. This meant removing only about .020" max. Then machined the faces of the bearing stands and both sides to a depth of 1.40" and keeping the width of the stands at 1.25". I managed to hit the front one pretty dead on, but the back ended up 8 thou thinner. I'll need to make the grooves in the bearings to match.
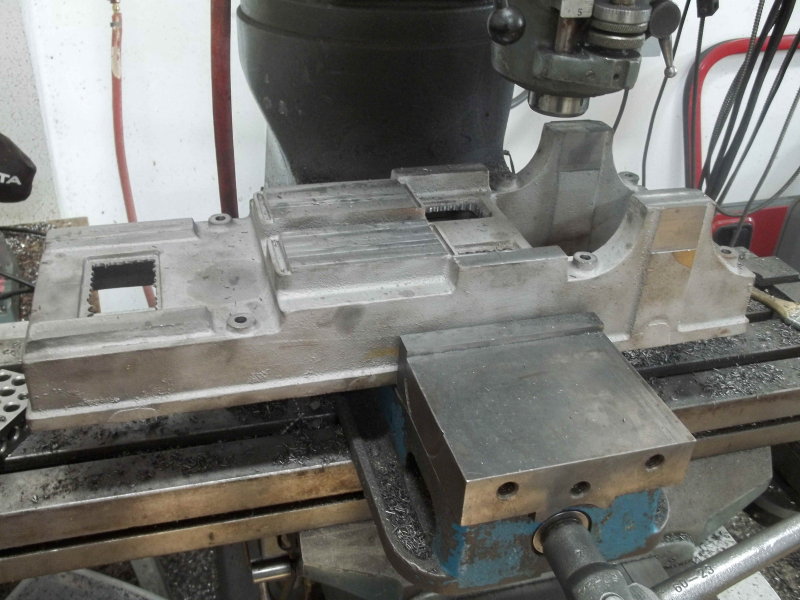
The next major step is machining the openings in the stands for the bearings. Once done, the bottom of the opening becomes the reference datum for facing the other two mounting surfaces. The center of the opening becomes the zero point of the x-axis, and the two outer faces of the stands become the datums for determining the engine centerline. All the mounting holes are positioned using this derived point in the XY plane and should help ensure that all the motion gear is straight and parallel.