This afternoon I made a start on the cylinder. A great big scaly old piece of cast iron, with a finish on it like a ponderosa pine. It was about 2 3/8" diameter and had came right from the foundry that cast it that size. I used a brazed carbide tool to bring it down to within about 0.010" of finished size, then changed to a HSS tool for the final cut to bring it down to 2", running about 400 rpm. I don't want to take it out of the chuck, so I will move my tailstock back out of the way and rig my steady rest to support the end opposite the chuck while I drill/bore/ream the 7/8" hole in the center.
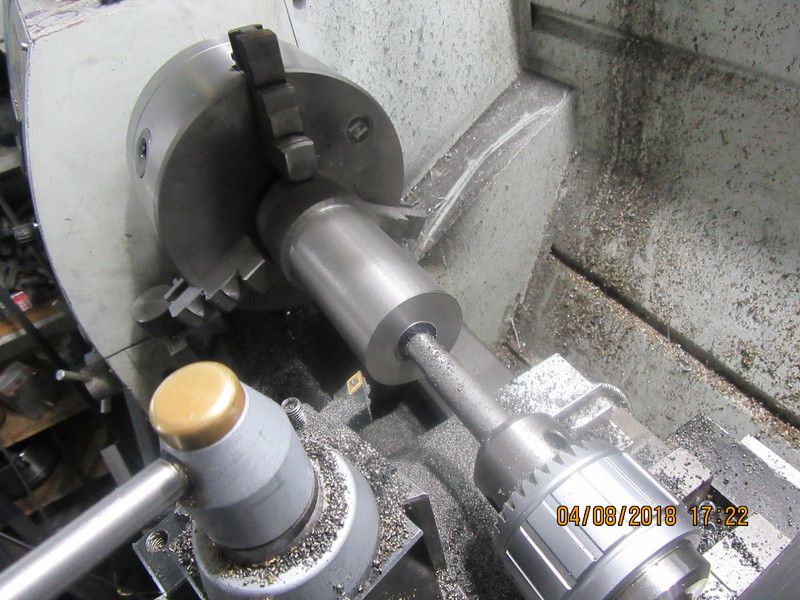