zeeprogrammer
Well-Known Member
- Joined
- Mar 14, 2009
- Messages
- 3,362
- Reaction score
- 13
Thanks Robert. I'll have to try Sketchup again. See what I can do with it.
Marv has a good round-over tool too. Uses an end-mill if I remember. Someday I'll have to make one. I'm thinking the end-mill would be better about keeping out abrasive?
So here's the vise stop so far. Next step are the holes for the two screws. The bigger piece will be threaded. The other not.
The piece on the right is tilted because of the heavier weight.
A little unhappy with the gap...seems too big.
Another reason for squaring all sides of the stock...if you're going to sand/polish it and want it to look good...it's easier if the sides have been milled (faced) a tad.
I wasn't looking for high polish...just wanted it to look decent. I hit the corners and edges with a file to take off the sharpness.
Yep. Just a vice stop.
Marv has a good round-over tool too. Uses an end-mill if I remember. Someday I'll have to make one. I'm thinking the end-mill would be better about keeping out abrasive?
So here's the vise stop so far. Next step are the holes for the two screws. The bigger piece will be threaded. The other not.
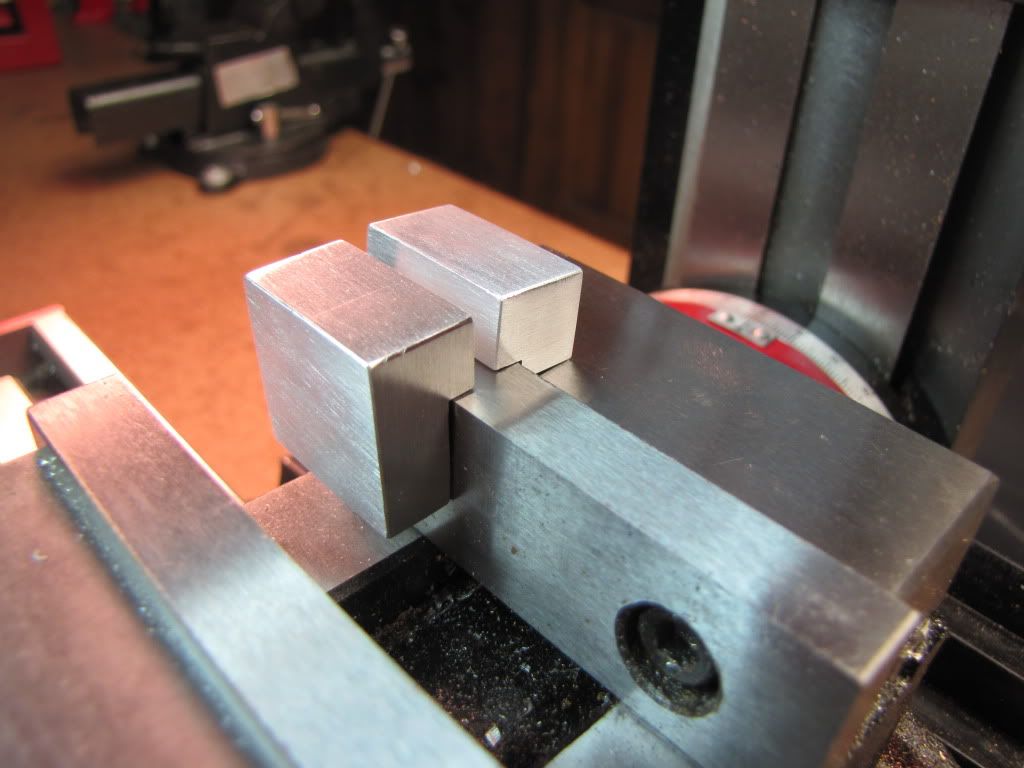
The piece on the right is tilted because of the heavier weight.
A little unhappy with the gap...seems too big.
Another reason for squaring all sides of the stock...if you're going to sand/polish it and want it to look good...it's easier if the sides have been milled (faced) a tad.
I wasn't looking for high polish...just wanted it to look decent. I hit the corners and edges with a file to take off the sharpness.
Yep. Just a vice stop.