Next I tackled the carb. The top is turned from 1" brass bar and then transfered to the mill to have the hex formed
before being upended to have 4 holes drilled which are quite a tight fit.
Luckily the bronze casting for the main carb body has a large turning spigot incorporated which makes it quite east to hold so most of the turning can be done at one setting, then moved to the hill for the cross holes and also two rather tricky passages for the fuel.
I then machined a matching 1/2"x40 ME thread onto a scrap bit of stock so the bottom hole could be reamed and undercut. I used the same method to hold the body to drill & tap the fuel needle hole at the required angle.
A couple of plugs for the fuel passages were turned from the machining spigot and then silver soldered into counterbores at the ends of the passages, the bits of angle stop the plugs dropping out when soldering, still a bit hot here.
And here are the two parts after a quick clean up, the plugs now need filing to profile and the surface texturing to match the rest of teh cast body.
The remaining parts are mostly straight forward turning if a little bit on the small side, the main thing to get right is the 45deg seating for the "float" which need s to be lapped in so the fuel is shut off until there is a vacuum in the intake at which point the float lifts against a small spring and allows fuel to flow.
And this is how it all goes together.
It was then just a case of making up the fuel lines, intake pipework and fuel filler pipe & cap.
J
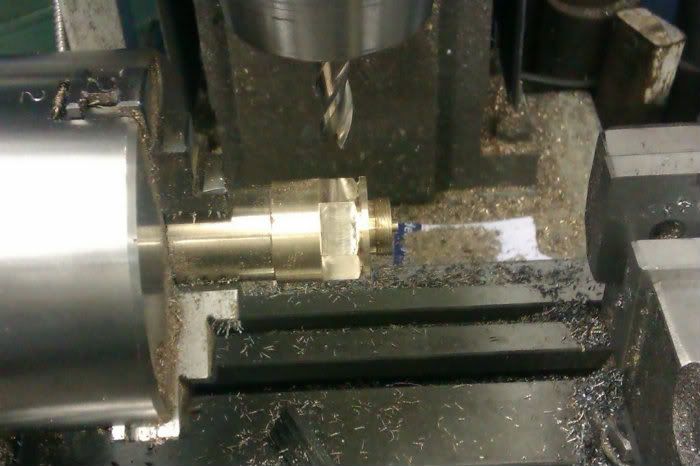
before being upended to have 4 holes drilled which are quite a tight fit.
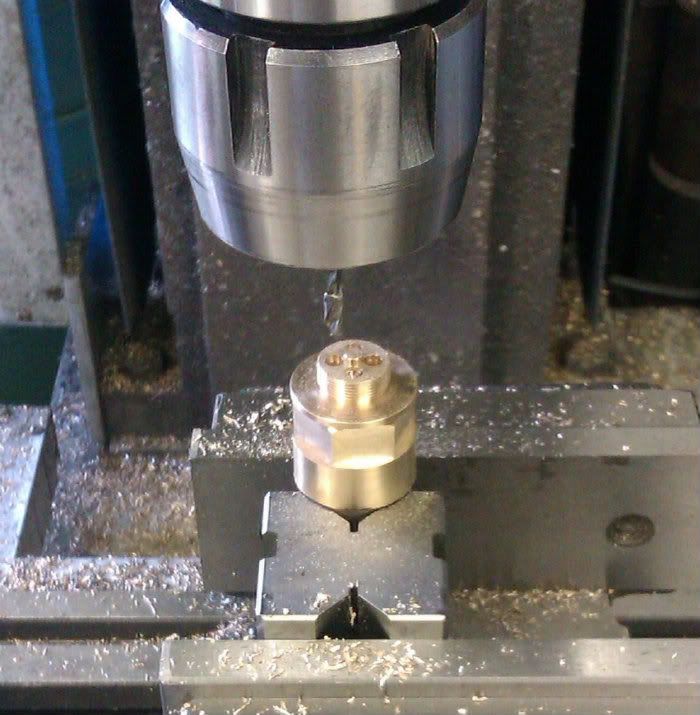
Luckily the bronze casting for the main carb body has a large turning spigot incorporated which makes it quite east to hold so most of the turning can be done at one setting, then moved to the hill for the cross holes and also two rather tricky passages for the fuel.
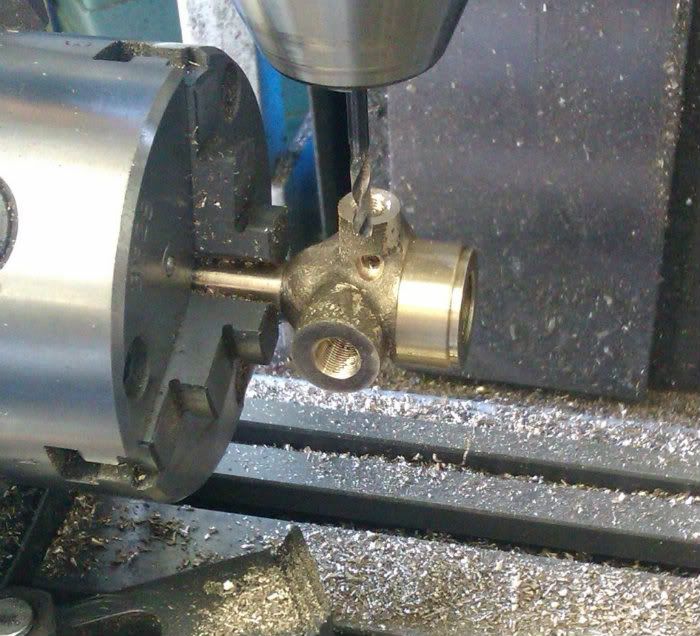
I then machined a matching 1/2"x40 ME thread onto a scrap bit of stock so the bottom hole could be reamed and undercut. I used the same method to hold the body to drill & tap the fuel needle hole at the required angle.
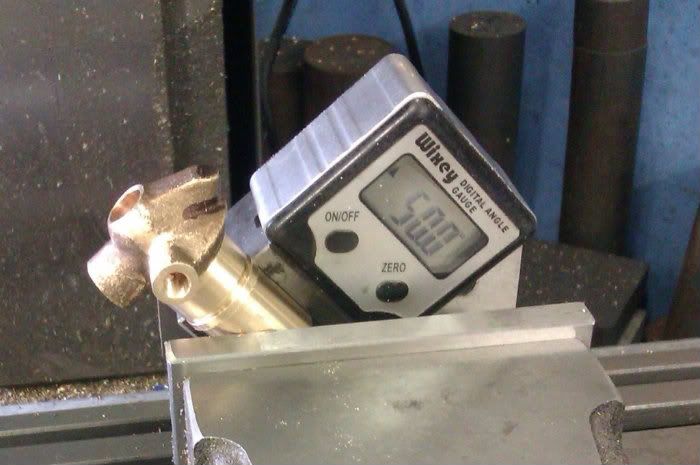
A couple of plugs for the fuel passages were turned from the machining spigot and then silver soldered into counterbores at the ends of the passages, the bits of angle stop the plugs dropping out when soldering, still a bit hot here.

And here are the two parts after a quick clean up, the plugs now need filing to profile and the surface texturing to match the rest of teh cast body.
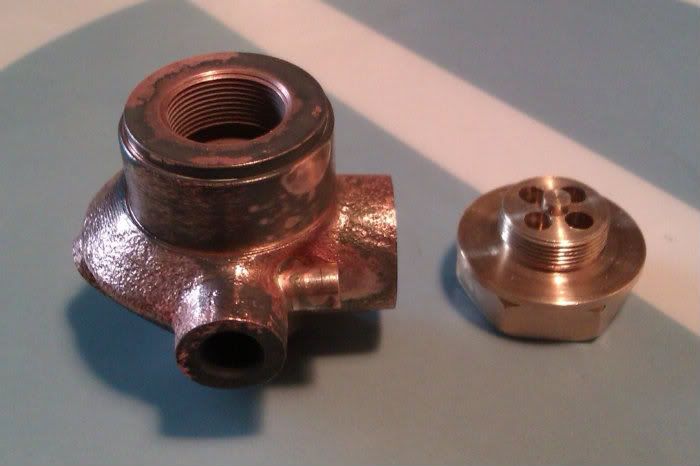
The remaining parts are mostly straight forward turning if a little bit on the small side, the main thing to get right is the 45deg seating for the "float" which need s to be lapped in so the fuel is shut off until there is a vacuum in the intake at which point the float lifts against a small spring and allows fuel to flow.
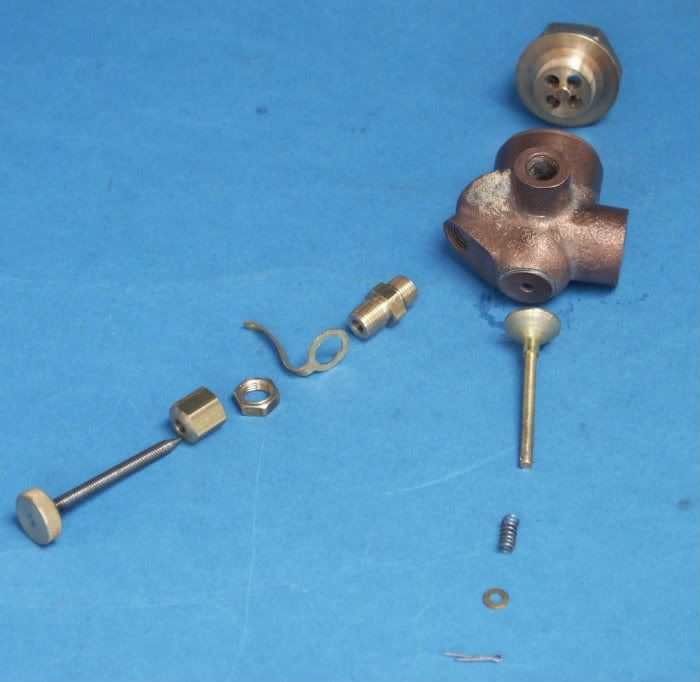
And this is how it all goes together.
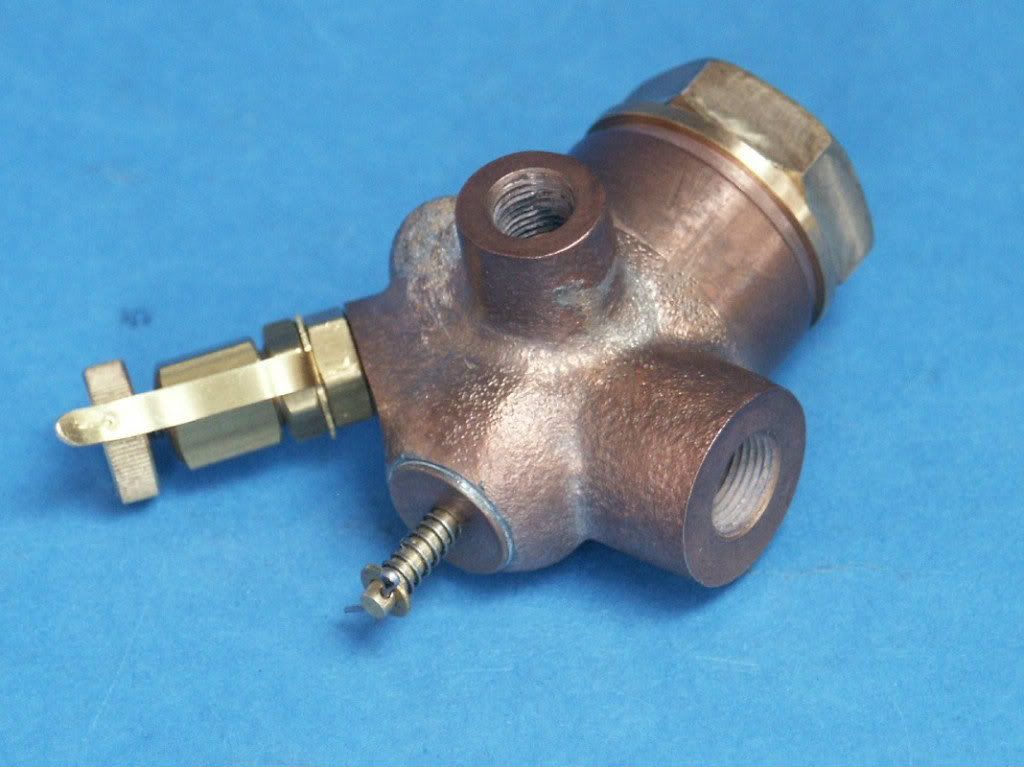
It was then just a case of making up the fuel lines, intake pipework and fuel filler pipe & cap.
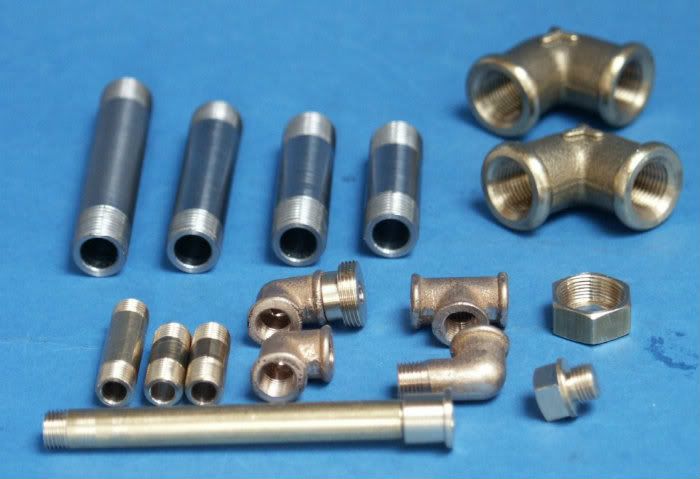
J