Bushing installed:
My 1st attempt (ever) at lapping. Turned a broom stick into an end-lap (nice fit at the end and smaller in the middle so I could run the cyl all the way past). Added a bit of valve grinding compound and had at it. Was looking more for a polish and smoothing than trying to change the size.
Rot-Roh Scooby! It revealed a small flaw. Looks like drilling for one of the cylinder mounts it almost broke through. You can see the pimple in the lower right--cannot feel it at all though:
Piston and Valve were next. 1st attempt was a biG fat PHAIL! But it gave me some good measurements to work from. .7105 fit but was way too tight and .7070 was way too small. This 2nd attempt ended up at .7095 and seems like it will work. I'm not doing them again unless they don't.
Parted off a chunk for the piston and this is the valve hollowed out:
It was a long day with a little bit of progress. That's where I stopped today.
This is a movie--click to view in Photobucket. It's the valve and a 4-40 screw substituting for the pivot stud and only the rough cut piston (not even hollowed out) installed in the cylinder. It's all completely dry and clean--no oil. Moving the valve makes the piston move! Hopefully this is close enough tolerances (and not too loose) for it to run.
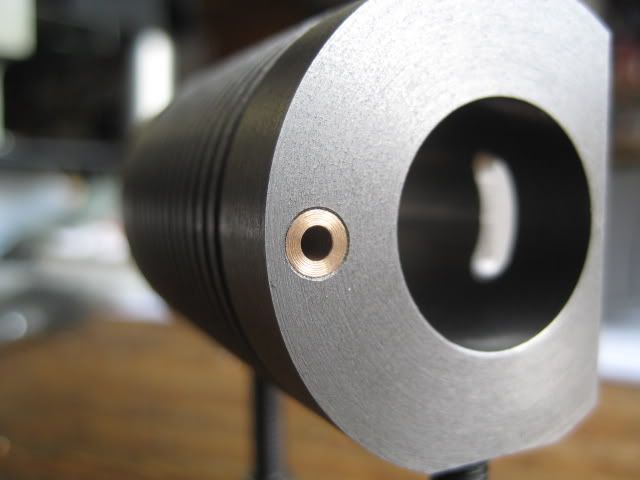
My 1st attempt (ever) at lapping. Turned a broom stick into an end-lap (nice fit at the end and smaller in the middle so I could run the cyl all the way past). Added a bit of valve grinding compound and had at it. Was looking more for a polish and smoothing than trying to change the size.
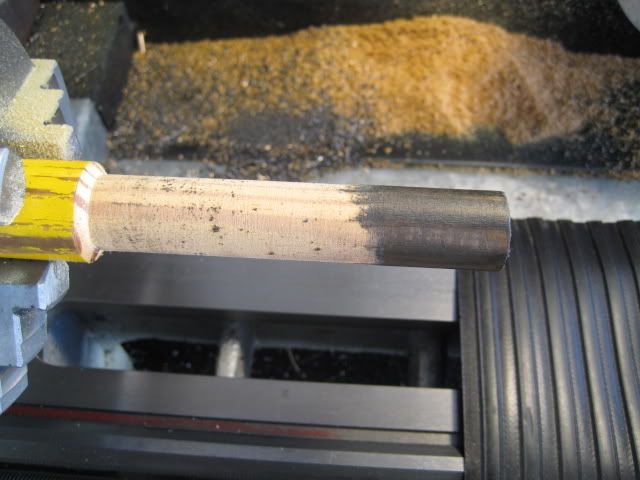
Rot-Roh Scooby! It revealed a small flaw. Looks like drilling for one of the cylinder mounts it almost broke through. You can see the pimple in the lower right--cannot feel it at all though:
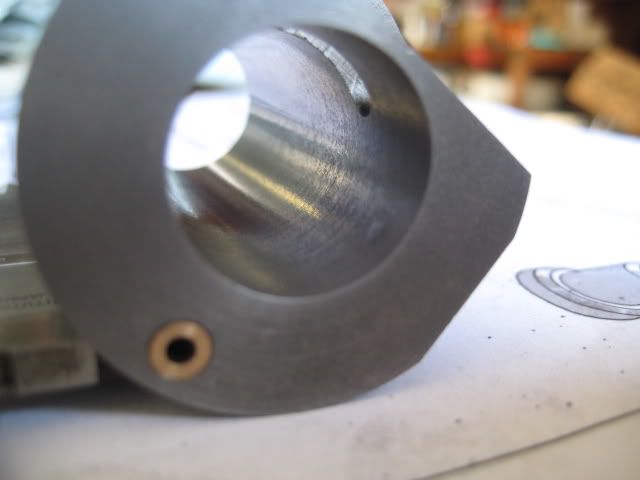
Piston and Valve were next. 1st attempt was a biG fat PHAIL! But it gave me some good measurements to work from. .7105 fit but was way too tight and .7070 was way too small. This 2nd attempt ended up at .7095 and seems like it will work. I'm not doing them again unless they don't.
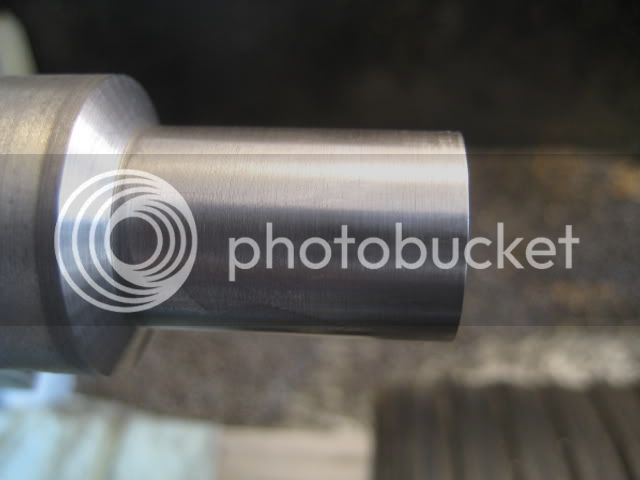
Parted off a chunk for the piston and this is the valve hollowed out:
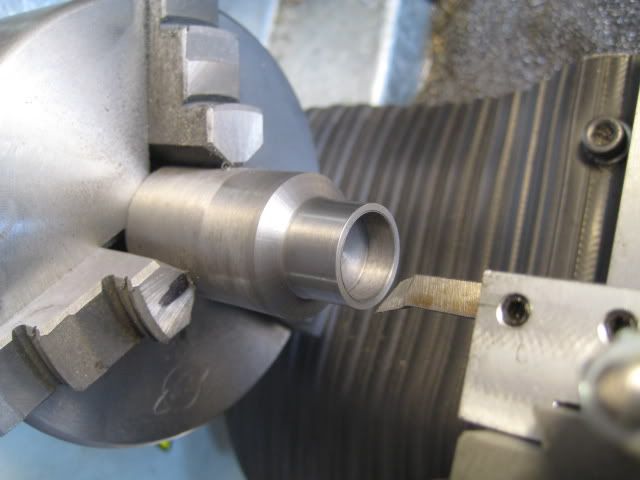
It was a long day with a little bit of progress. That's where I stopped today.
This is a movie--click to view in Photobucket. It's the valve and a 4-40 screw substituting for the pivot stud and only the rough cut piston (not even hollowed out) installed in the cylinder. It's all completely dry and clean--no oil. Moving the valve makes the piston move! Hopefully this is close enough tolerances (and not too loose) for it to run.
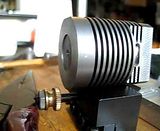