Late last year as my Quorn T&C grinder was nearing completion I was planning on starting an O gauge live steam loco but I came across the Demon V8 build log by Steve Huck I must say it impressed me and and I decided then to put off the loco project and swap it for a running V8 - as I had a few months to go on the Quorn I decided to have a go at my own design.
Not having any experience with model engine design there is always a chance that the design will be difficult to build or even worse may not be a good runner. In that event I would simply purchase a set of Little Demon plans, by all accounts Steve had done a great job of the plans and build details, the design is proven with quite a few examples built and running and being a forum member he is always ready to help out with advice.
The Quorn is now finished to the point where it is use able and my plans have reached the point where I could start actual machining. Bore and stroke is .625" - if this sounds like the PeeWee V4and the Steve Huck V8 that is because I copied these sizes from those two engines, mainly because I know rings can be made that size, I have not made rings before and being my first IC engine there is a lot of info in the forum posts on ring making to help me - the rest of the engine is my own design.
I started with the block, a square extrusion about 6inches long, final length will be a bit over 5.25 inches, extrusions may look square but are not good enough to use with out being squared up.
For this I used the lathe checking each time that the newly machined surface was parallel to the lathe bed, once squared up I mounted the block onto a steel back plate that was drilled to be bolted to my rotary table. The idea is that once the block is setup parallel to the mill table I can machine each surface by indexing the rotary table.
Before I set it up in the rotary table I spotted the holes for the crank and cam as I will probably machine away the face I am using as my datum point. Once bolted to the rotary table I set it square and parallel to the mill table with the rotary set on 0 deg. an angle plate clamped to the extrusion was needed to steady it as I could see it wobbling around once I started boring the holes for the cylinder liners. I don't have any sort of CNC setup but I do have the luxury of a DRO on my mill which does take some of the pain out of it.
Not having any experience with model engine design there is always a chance that the design will be difficult to build or even worse may not be a good runner. In that event I would simply purchase a set of Little Demon plans, by all accounts Steve had done a great job of the plans and build details, the design is proven with quite a few examples built and running and being a forum member he is always ready to help out with advice.
The Quorn is now finished to the point where it is use able and my plans have reached the point where I could start actual machining. Bore and stroke is .625" - if this sounds like the PeeWee V4and the Steve Huck V8 that is because I copied these sizes from those two engines, mainly because I know rings can be made that size, I have not made rings before and being my first IC engine there is a lot of info in the forum posts on ring making to help me - the rest of the engine is my own design.
I started with the block, a square extrusion about 6inches long, final length will be a bit over 5.25 inches, extrusions may look square but are not good enough to use with out being squared up.
For this I used the lathe checking each time that the newly machined surface was parallel to the lathe bed, once squared up I mounted the block onto a steel back plate that was drilled to be bolted to my rotary table. The idea is that once the block is setup parallel to the mill table I can machine each surface by indexing the rotary table.
Before I set it up in the rotary table I spotted the holes for the crank and cam as I will probably machine away the face I am using as my datum point. Once bolted to the rotary table I set it square and parallel to the mill table with the rotary set on 0 deg. an angle plate clamped to the extrusion was needed to steady it as I could see it wobbling around once I started boring the holes for the cylinder liners. I don't have any sort of CNC setup but I do have the luxury of a DRO on my mill which does take some of the pain out of it.
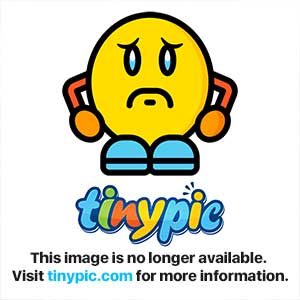
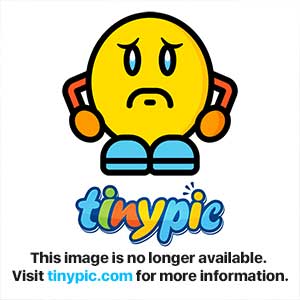
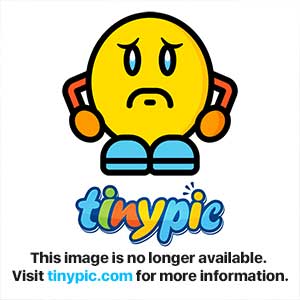
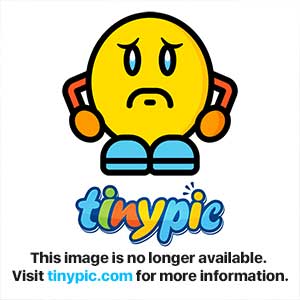
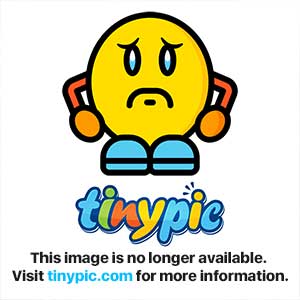
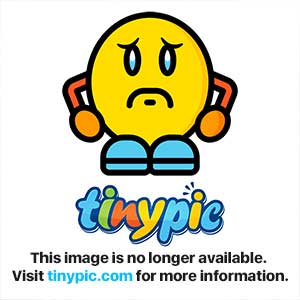
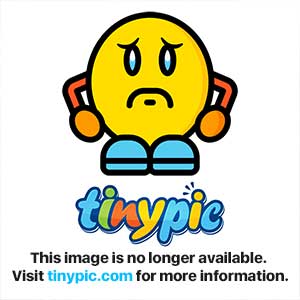
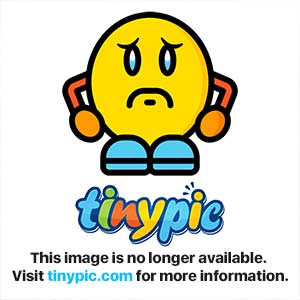
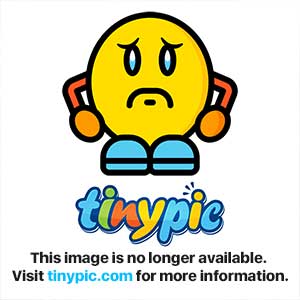
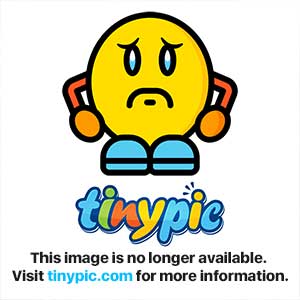
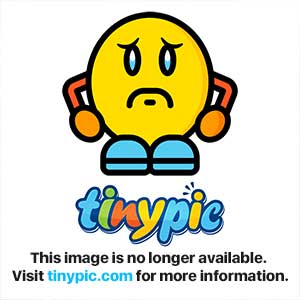
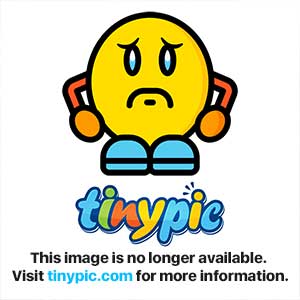
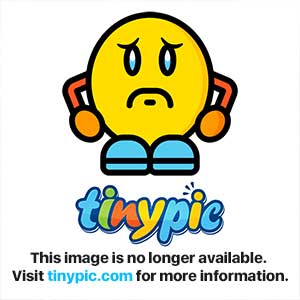
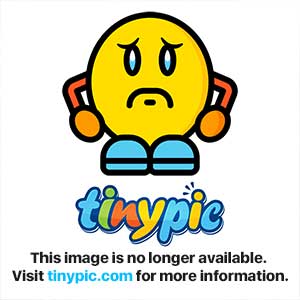
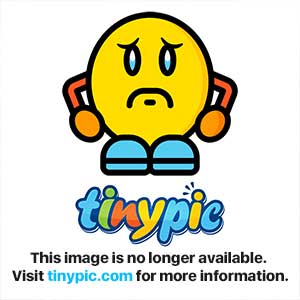